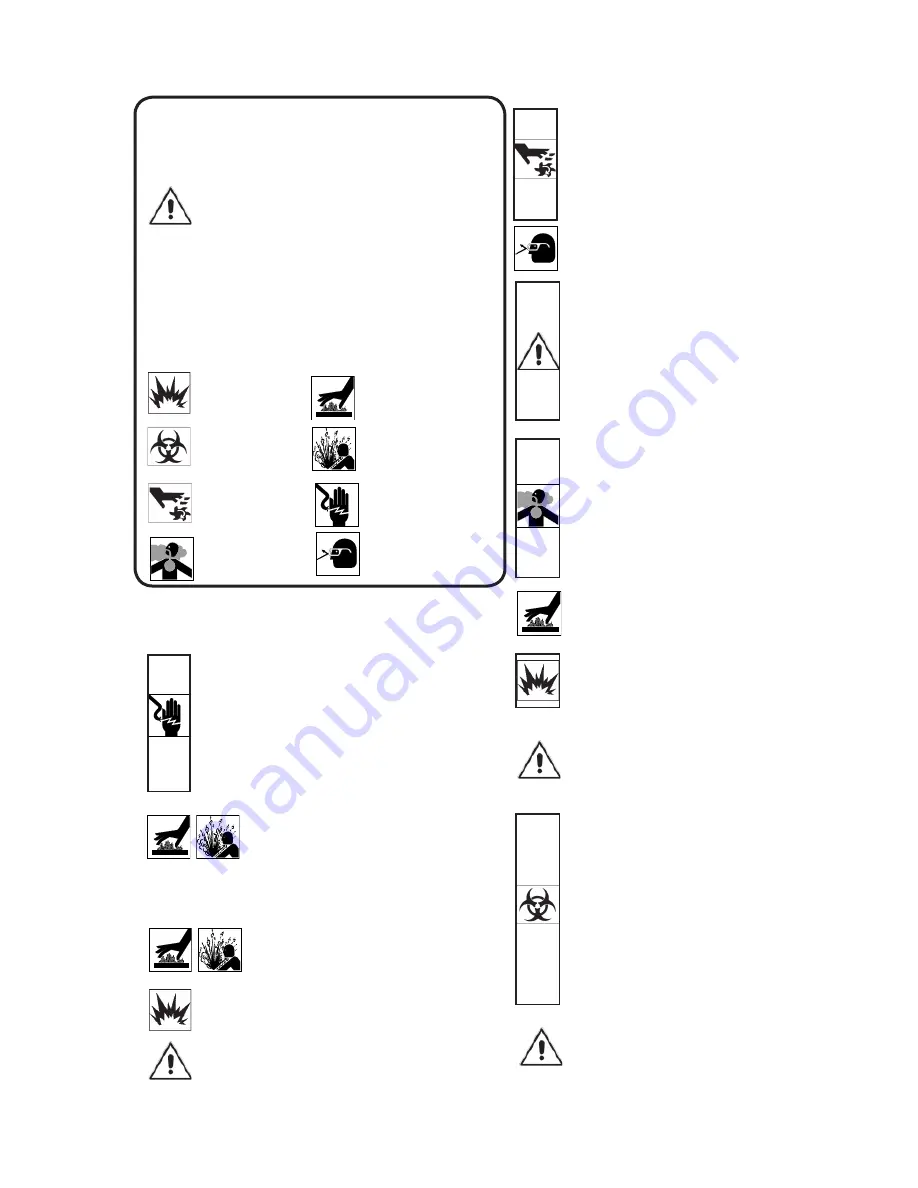
3
Please Read This Before Installing Or Operating Pump.
This information is provided for
SAFETY and to PREVENT
EQUIPMENT PROBLEMS
. To help recognize this information,
observe the following symbols:
IMPORTANT!
Warns about hazards that can result
in personal injury or Indicates factors concerned with
assembly, installation, operation, or maintenance which
could result in damage to the machine or equipment if
ignored.
CAUTION !
Warns about hazards that can or will cause minor
personal injury or property damage if ignored. Used with symbols
below.
WARNING !
Warns about hazards that can or will cause serious
personal injury, death, or major property damage if ignored. Used
with symbols below.
Only qualifi ed personnel should install, operate and repair
pump. Any wiring of pumps should be performed by a qualifi ed
electrician.
WARNING ! -
To reduce risk of electrical shock, pumps
and control panels must be properly grounded in
accordance with the National Electric Code (NEC) or
the Canadian Electrical Code (CEC) and all applicable
state, province, local codes and ordinances. Improper
grounding voids warranty.
WARNING! -
To reduce risk of electrical shock, always
disconnect the pump from the power source before
handling or servicing. Lock out power and tag.
WARNING!
Operation against a closed
discharge valve will cause premature bearing
and seal failure on any pump, and on end
suction and self priming pump the heat build
may cause the generation of steam with resulting dangerous
pressures. It is recommended that a high case temperature
switch or pressure relief valve be installed on the pump body.
CAUTION!
Pumps build up heat and pressure
during operation-allow time for pumps to cool
before handling or servicing.
WARNING!
-
DO NOT
pump hazardous materials
(fl ammable, caustic, etc.) unless the pump is specifi cally
designed and designated to handle them.
CAUTION!
- Do not block or restrict discharge hose, as
discharge hose may whip under pressure.
WARNING! - DO NOT
wear loose clothing that may
become entangled in the impeller or other moving parts.
Always wear appropriate safety gear, such as safety
glasses, when working on the pump or piping.
WARNING! -
Keep clear of suction and discharge
openings.
DO NOT
insert fi ngers in pump with power
connected.
Always wear eye protection when working on pumps.
Make sure lifting handles are securely fastened each
time before lifting.
DO NOT
operate pump without safety
devices in place. Always replace safety devices that
have been removed during service or repair. Secure the
pump in its operating position so it can not tip over, fall
or slide.
DO NOT
exceed manufacturers recommendation for
maximum performance, as this could cause the motor
to overheat.
WARNING!
If Engine driven, never operate in an
enclosed building or area where exhaust gases can
accumulate. Never operate near a building where
exhaust gases can seep inside. Never operate in a
pit or sump without making provisions for adequate
ventilation.
WARNING!
Do not breathe exhaust fumes when
working in the area of the engine. (Exhaust gases are
odorless and deadly poison.)
WARNING!
Allow exhaust system to cool before
touching.
Never add fuel to the tank while the engine is running.
Stop engine and allow to cool.
Do not smoke while refueling the engine
Do not refuel near open fl ame
Carefully read instruction manuals supplied by engine
manufacture before attempting to assemble, operate
or service the engine or any part. The “WARNING”
statements indicate potentially hazardous conditions for
operator or equipment.
WARNING!
Products Returned Must Be Cleaned,
Sanitized, Or Decontaminated As Necessary Prior
To Shipment, To Insure That Employees Will Not Be
Exposed To Health Hazards In Handling Said Material.
All Applicable Laws And Regulations Shall Apply.
Bronze/brass and bronze/brass fi tted pumps may
contain lead levels higher than considered safe for
potable water systems. Lead is known to cause cancer
and birth defects or other reproductive harm. Various
government agencies have determined that leaded
copper alloys should not be used in potable water
applications. For non-leaded copper alloy materials of
construction, please contact factory.
IMPORTANT! -
Crane Pumps & Systems, Inc. is not
responsible for losses, injury, or death resulting from a
failure to observe these safety precautions, misuse or
abuse of pumps or equipment.
SAFETY FIRST!
Hazardous fl uids can
cause fi re or explosions,
burnes or death could
result.
Extremely hot - Severe
burnes can occur on contact.
Biohazard can cause
serious personal injury.
Hazardous fl uids can Hazard-
ous pressure, eruptions or ex-
plosions could cause personal
injury or property damage.
Rotating machinery
Amputation or severe
laceration can result.
Hazardous voltage can
shock, burn or cause death.
Toxic Fumes -
Breathing can cause
nausea, fainting or death
Eye protectiong required
Summary of Contents for Crown B12 Series
Page 12: ...12 MODEL B4 B6 B9 ...
Page 14: ...14 MODEL SB4 SB6 SB9 ...
Page 16: ...16 MODEL B12 ...
Page 18: ...18 MODEL SB12 ...
Page 20: ...20 MODEL BH7 ...
Page 22: ...22 MODEL SBH7 ...
Page 24: ...24 MODEL B19 B21 ...
Page 26: ...26 MODEL SB19 SB21 ...
Page 32: ...Notes ...