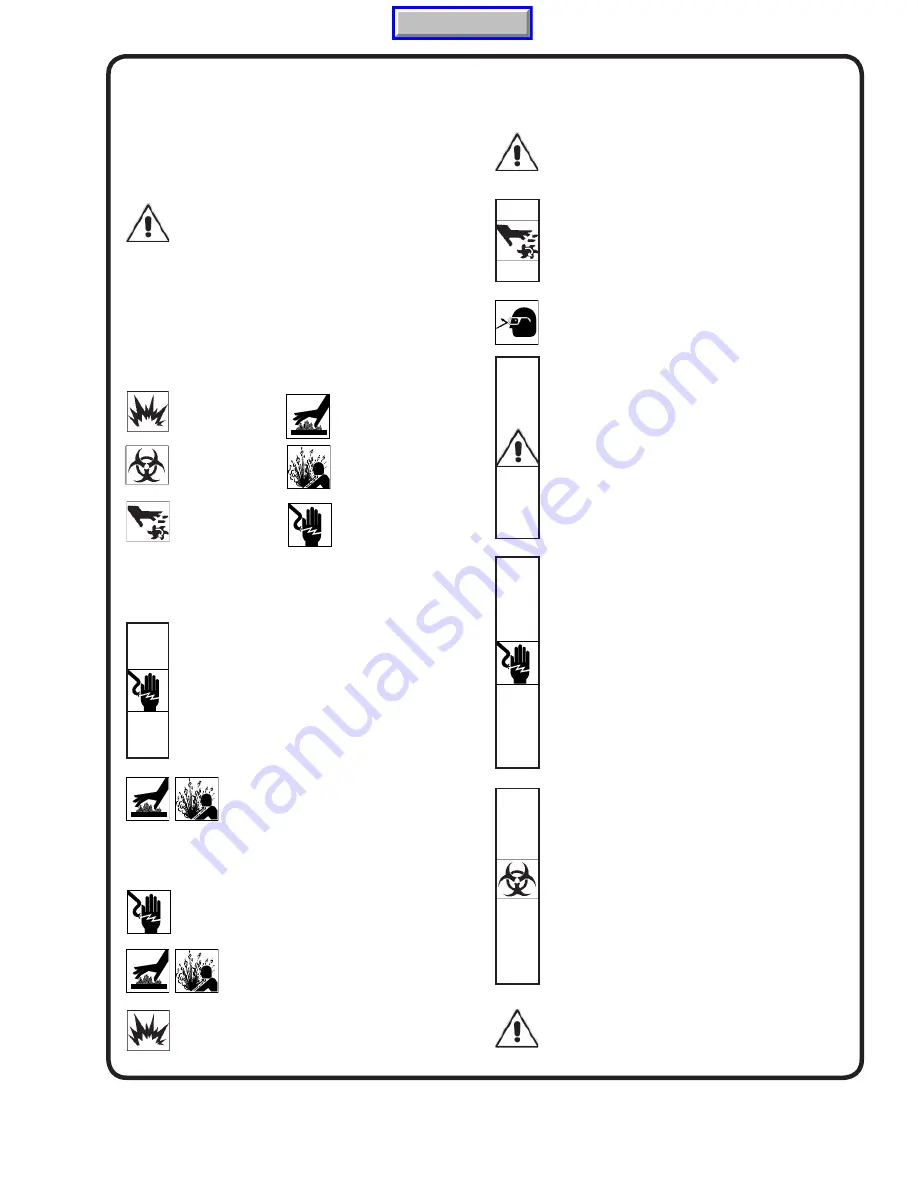
3
Please Read This Before Installing Or Operating Pump.
This information is provided for
SAFETY
and to
PREVENT
EQUIPMENT PROBLEMS.
To help recognize this information,
observe the following symbols:
IMPORTANT!
Warns about hazards that can result
in personal injury orIndicates factors concerned with
assembly, installation, operation, or maintenance which
could result in damage to the machine or equipment if
ignored.
CAUTION!
Warns about hazards that
can or will cause minor
personal injury or property damage if ignored. Used with symbols
below.
WARNING!
Warns about hazards that can or will cause serious
personal injury, death, or major property damage if ignored. Used
with symbols below.
Only qualifi
ed personnel should install, operate and repair
pump. Any wiring of pumps should be performed by a qualifi ed
electrician.
WARNING !
To reduce risk of electrical shock, pumps and
control panels must be properly grounded in accordance
with the National Electric Code (NEC) or the Canadian
Electrical Code (CEC) and all applicable state, province,
local codes and ordinances. Improper grounding voids
warranty.
WARNING!
To reduce risk of electrical shock, always
disconnect the pump from the power source before
handling or servicing. Lock out power and tag.
WARNING!
Operation against a closed
discharge valve will cause premature bearing
and seal failure on any pump, and on end
suction and self priming pump the heat build
may cause the generation of steam with resulting dangerous
pressures. It is recommended that a high case temperature
switch or pressure relief valve be installed on the pump body.
CAUTION !
Never operate a pump with a plug-in type
power cord without a ground fault circuit interrupter.
CAUTION !
Pumps build up heat and pressure
during operation-allow time for pumps to cool
before handling or servicing.
WARNING !
Do not pump hazardous materials
(fl ammable, caustic, etc.) unless the pump is specifi cally
designed and designated to handle them.
CAUTION !
Do not
block or restrict discharge hose, as
discharge hose may whip under pressure.
WARNING !
Do not wear loose clothing that may
become entangled in moving parts.
WARNING !
Keep clear of suction and discharge
openings.
DO NOT
insert fi ngers in pump with power
connected.
Always wear eye protection when working on pumps.
Make sure lifting handles are securely fastened each
time before lifting.
DO NOT
operate pump without safety
devices in place. Always replace safety devices that
have been removed during service or repair. Secure the
pump in its operating position so it can not tip over, fall
or slide.
DO NOT
exceed manufacturers recommendation for
maximum performance, as this could cause the motor
to overheat.
DO NOT
remove cord and strain relief.
DO NOT
connect
conduit to pump.
WARNING !
Cable should be protected at all times to
avoid punctures, cut, bruises and abrasions. Inspect
frequently. Never handle connected power cords with
wet hands.
WARNING !
To reduce risk of electrical shock, all wiring
and junction connections should be made per the NEC
or CEC and applicable state or province and local
codes. Requirements may vary depending on usage
and location.
WARNING!
Submersible Pumps are not approved for
use in swimming pools, recreational water installations
decorative fountains or any installation where human
contact with the pumped fl uid is common.
WARNING!
Products returned must be cleaned,
sanitized, or decontaminated as necessary prior to
shipment, to insure that employees will not be exposed
to health hazards in handling said material. All Applicable
Laws And Regulations Shall Apply.
Bronze/brass and bronze/brass fi tted pumps may
contain lead levels higher than considered safe for
potable water systems. Lead is known to cause cancer
and birth defects or other reproductive harm. Various
government agencies have determined that leaded
copper alloys should not be used in potable water
applications. For non-leaded copper alloy materials of
construction, please contact factory.
Crane Pumps & Systems, Inc. is not responsible for
losses, injury, or death resulting from a failure to observe
these safety precautions, misuse or abuse of pumps or
equipment.
SAFETY FIRST!
Hazardous fl uids can
cause fi re or explo-
sions, burnes or death
could result.
Extremely hot - Severe
burnes can occur on contact.
Biohazard can cause
serious personal injury.
Hazardous fl uids can Hazard-
ous pressure, eruptions or ex-
plosions could cause personal
injury or property damage.
Rotating machinery
Amputation or severe
laceration can result.
Hazardous voltage can
shock, burn or cause death.
Manual Index
Summary of Contents for Barnes SE51 Series
Page 13: ...13 FIGURE 10 Manual Index ...
Page 14: ...14 FIGURE 11 Manual Index ...