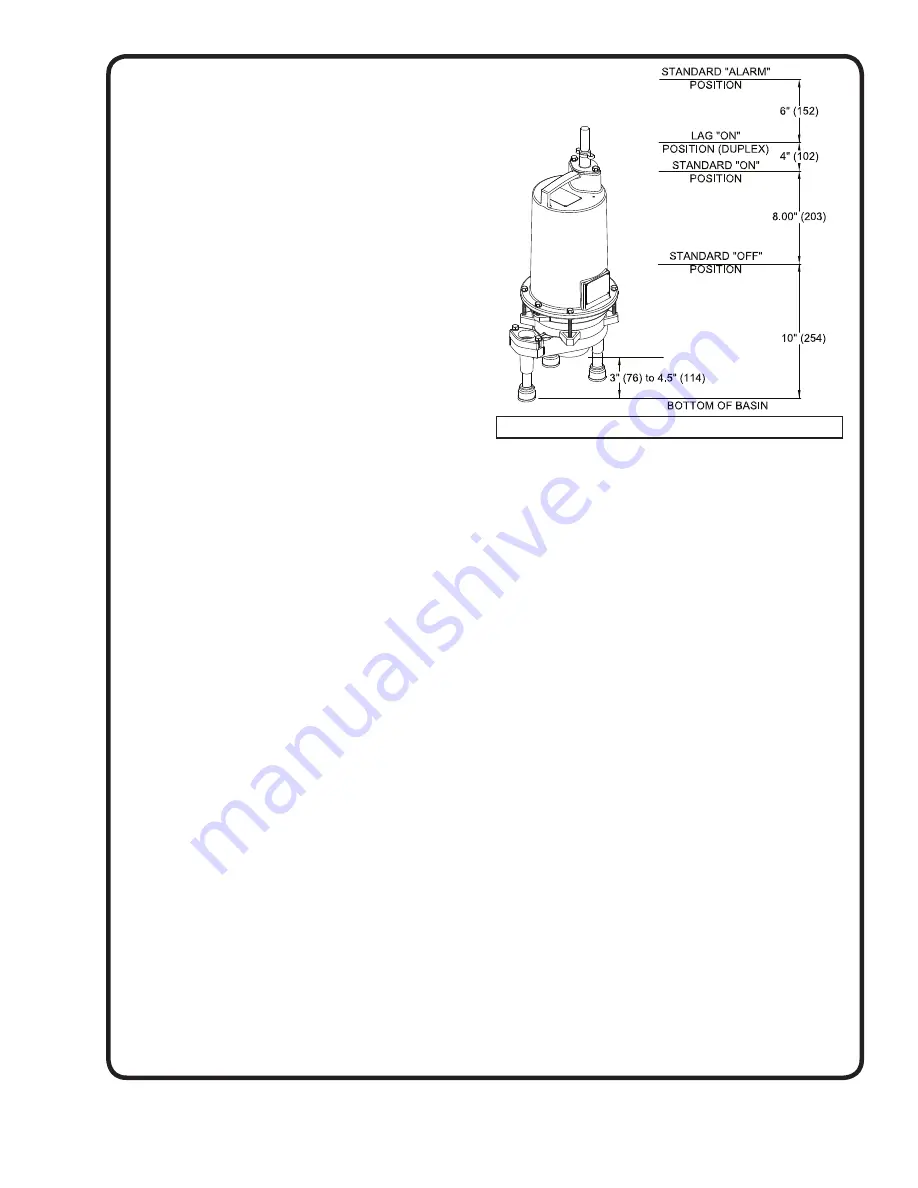
7
RECEIVING/UNPACKING:
Upon receiving the pump, it should be inspected for dam-
age or shortages. If damage has occurred,
fi
le a claim
immediately with the company that delivered the pump.
Unpack pump and record pump serial and model number
before installing. If the manual is removed from the pack-
aging, do not lose or misplace.
STORAGE:
Short Term-
For best results, pumps can be retained in
storage, as factory assembled, in a dry atmosphere with
constant temperatures for up to six (6) months.
Long Term-
Any length of time exceeding six (6) months,
but not more than twenty-four (24) months. The units
should be stored in a temperature controlled area, a roofed
over walled enclosure that provides protection from the
elements (rain, snow, wind-blown dust, etc.), and whose
temperature can be maintained b40 deg. F and
+120 deg. F. If extended high humidity is expected to be
a problem, all exposed parts should be inspected before
storage and all surfaces that have the paint scratched,
damaged, or worn should be recoated with a air dry
enamel paint. All surfaces should then be sprayed with a
rust-inhibiting oil.
Pump should be stored in its original shipping container.
On initial start up, rotate shaft by hand to assure seal
and motor rotate freely. If it is required that the pump be
installed and tested before the long term storage begins,
such installation will be allowed provided:
1.) The pump is not installed under water for more than
one (1) month.
2.) Immediately upon satisfactory completion of the
test, the pump is removed, thoroughly dried,
repacked in the original shipping container, and
placed in a temperature controlled storage area.
3.) Before placing pump into service, pump should be
brought to operational temperature range.
Excessive or direct heating or cooling should
NOT
be
used.
OPERATION TEMPERATURE RANGE:
+35ºF (2ºC) to
104ºF (40ºC).
SERVICE CENTERS:
For the location of the nearest Barnes Service Center,
check your Barnes representative or Crane Pumps
& Systems, Inc., Service Department in Piqua, Ohio,
telephone (937) 778-8947 or in Brampton, Ontario,
Canada (905) 457-6223.
INSTALLATION:
Location -
The pump is designed with pipe legs to
keep a minimum of 3 inch clearance.
THIS PUMP
MUST BE INSTALLED WITH A MINIMUM OF 3
INCHES CLEARANCE UNDER THE PUMP FOR THE
ENTRANCE OF SEWAGE SOLIDS.
Discharge -
Assemble discharge piping or hose assembly
(whichever is required by your application), to the pump.
Discharge piping should be as short as possible. Both a
check valve and a shut-off valve are required for each pump
being used. The check valve is used to prevent back
fl
ow
into the sump. Excessive back
fl
ow can cause
fl
ooding and/
or damage to the pump. The shut-off valve is used to stop
system
fl
ow during pump or check valve servicing. If pump
is installed with a discharge hose rather than a moveable
fi
tting assembly, make sure the discharge pipe has a 1/8”
dia. hole approx. 5” from end nearest volute and oriented
towards the pump body.
ELECTRICAL CONNECTIONS:
Pump Cords -
The quick connect cord assembly mounted
to the pump must
NOT
be modi
fi
ed in any way except for
shortening to a speci
fi
c application. Any supply cables con-
nections between the pump and the control panel must be
made in accordance with the National Electric Code or the
Canadian Electric Code and all applicable state, province
and local electric codes. It is recommended that a junction
box, be mounted outside the sump or be of at least Nema
4 (EEMAC-4) construction if located within the wet well.
DO NOT USE THE POWER OR CONTROL CABLES TO
LIFT PUMP!
Overload Protection -
The type of in-winding overload
protector used is referred to as an inherent overheating
protector and operates on the combined effect of temperature
and current. This means that the overload protector will trip
out and shut the pump off if the windings become too hot,
or the load current passing through them becomes too high.
It will then automatically reset and start the pump up after
the motor cools to a safe temperature. In the event of an
overload, the source of this condition should be determined
and recti
fi
ed immediately.
DO NOT LET THE PUMP CYCLE
OR RUN IF AN OVERLOAD CONDITION OCCURS !
Wire Size -
If additional cord is required consult a quali
fi
ed
electrician for proper wire size.
FIGURE 3 - L Series
(For Automatic see Level Control manual)
Summary of Contents for Barnes PGPH Series
Page 10: ...10 FIGURE 6 ...
Page 12: ...Notes ...