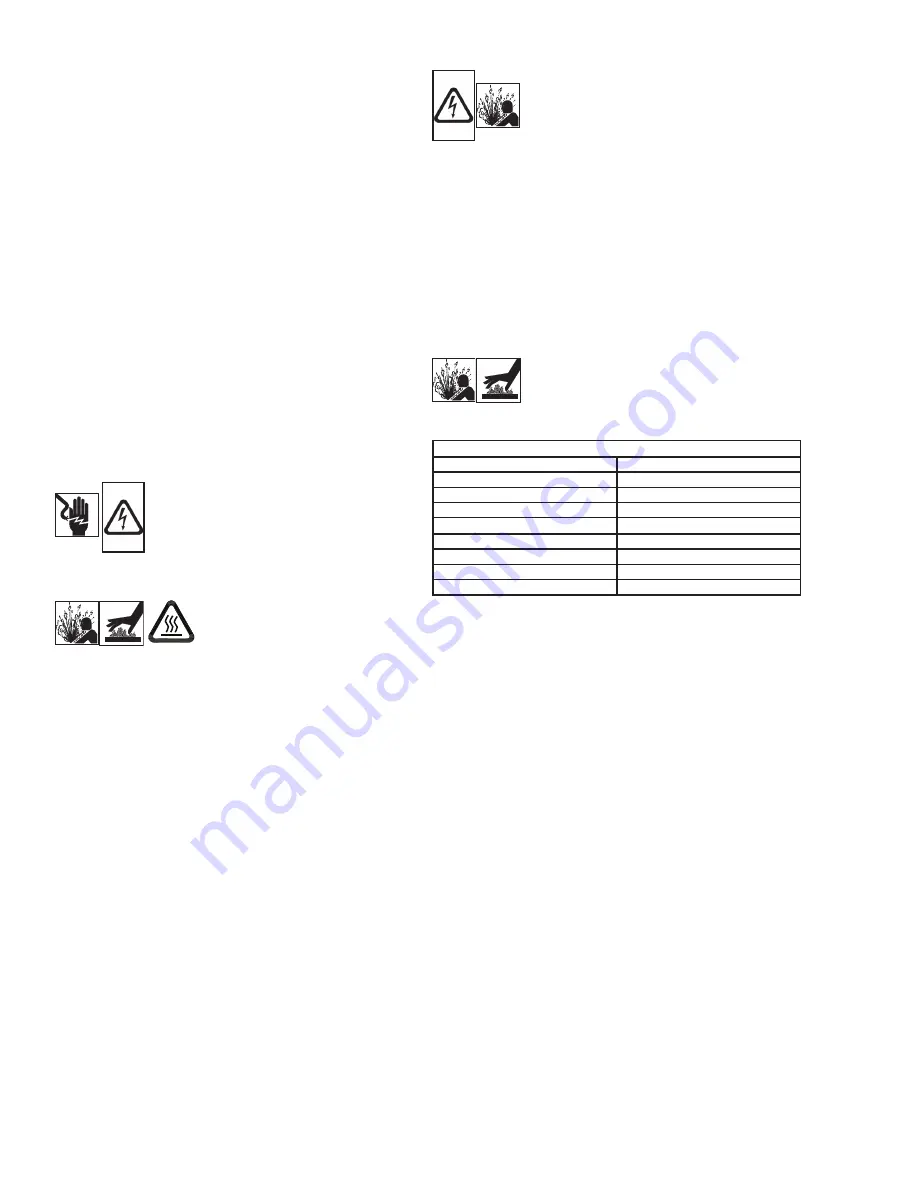
22
SECTION D: PREVENTATIVE MAINTENANCE
As the motor and seal chamber are oil-filled, no lubrication or
other maintenance is required, and generally Barnes Pumps
will give very reliable service and can be expected to operate
for years of normal sewage pumping without failing. However,
as with any mechanical piece of equipment a preventive
maintenance program is recommended and suggested to
include the following checks:
1) Test moisture detector control “Test Switch” for
continuity of circuit. Water in the seal chamber will
energize a seal leak warning light at the control
panel. This is a warning light only and does not
stop the motor. It indicates the seal has leaked
and must be repaired. This should be done within 2
or 3 weeks to prevent further damage. See section
C-2.2.
2) Inspect impeller and body for excessive build-up or
clogging and repair as required per section E-2.
3) Inspect outer shaft seal and replace as required per
section E-3.
4) Check motor for ground leakage and proper amp draw.
SECTION E: SERVICE AND REPAIR
NOTE: All item numbers in ( ) refer to Figures 10 thru 17.
WARNING ! - Electrical power to the
pump motors must be disconnected and
locked out to prevent any dangerous
electrical hazards or personnel danger
before any service work is done to the
pump.
CAUTION ! - Operating pump
builds up heat and pressure;
allow time for pump to cool
to room temperature before
handling or servicing.
E-1) Lubrication
E-1.1) Checking Oil
1. Place pump on it’s side, and drain oil into a clean, dry
container.
2. Check oil for contamination using an oil tester with a
range to 30 Kilovolts breakdown.
3. If oil is found to be clean and uncontaminated (measure
above 15 KV. breakdown), refill the seal chamber as per
section E-1.2.
4. If oil is found to be dirty or contaminated (or measures
below 15 KV. breakdown), the pump must be carefully
inspected for leaks at the shaft seal (4), before refilling
with oil. To locate the leak, perform a pressure test as per
section E-1.3. After leak is repaired, refill with new oil as
per section E-1.2.
E-1.2) Replacing Oil:
Seal Chamber - Drain all oil from seal chamber and dispose
of properly. Refill with (see parts list for amount) new cooling
oil as per Table 2. An air space must remain to compensate
for oil expansion (See Fig. 9 and 12). Set unit on side and
fill.
IMPORTANT! - Do not overfill oil.
Overfilling of seal chamber with oil
can create excessive and dangerous
hydraulic pressure which can destroy the
pump and create a hazard. Overfilling oil
voids warranty.
E-1.3) Pressure Test:
Seal Chamber - Before checking the pump for leaks around
the shaft seal, the oil level should be full. Remove pipe plug.
Apply pipe sealant to pressure gauge assembly and tighten
into pipe plug hole. Pressurize motor housing to 10 P.S.I.
Use a soap solution around the sealed area and inspect
joints for “air bubbles”. If, after five minutes, the pressure
is still holding constant, and no “bubbles” are observed,
slowly bleed the pressure and remove the gauge assembly.
Replace the pipe plug using a sealant. If the pressure does
not hold, then the leak must be located.
CAUTION! - Pressure builds up extremely
fast, increase pressure by “tapping” air
nozzle. Too much pressure will damage
seal. Do Not exceed 10 P.S.I. in seal
chamber.
TABLE 2 - COOLING OIL - Dielectric
SUPPLIER
GRADE
BP
Enerpar SE100
Conoco
Pale Paraffin 22
Mobil
D.T.E. Oil Light
G & G Oil
Circulating 22
Imperial Oil
Voltesso-35
Shell Canada
Transformer-10
Texaco
Diala-Oil-AX
Woco
Premium 100
E-2) Impeller and Volute Service:
E-2.1) Disassembly and Inspection:
To clean out the volute (10), or clean out or replace impeller
(6), disconnect power, remove cap screws (2) then vertically
lift motor assembly from the pump body (10). Clean out
the volute, if necessary, clean and examine impeller (6)
for pitting or wear, replace if required. To remove Impeller
(6), remove cap screw (8) and washer (8A). The impeller is
keyed onto the shaft with a square key (7) and to remove,
pull impeller straight off the shaft using a wheel puller if
required. Inspect o-ring (9) and replace if cut or damaged.
Before reinstallation, check the motor shaft and impeller
bore for damage.
E-2.2) Reassembly:
To install impeller (6), apply a thin film of oil to motor shaft
and slide impeller straight onto shaft, keeping keyways
lined up. Drive key (7) into keyway. Thread cap screw (8)
and washer (8A) into shaft and torque to 45 ft. lbs. Rotate
impeller to check for binding. Place o-ring (9) on seal plate
pilot diameter lining up holes and install impeller and motor
assembly onto volute (10). Loctite cap screws (2), insert into
volute and motor assembly and torque to 35 ft. lbs. Check
for free rotation of motor and impeller.