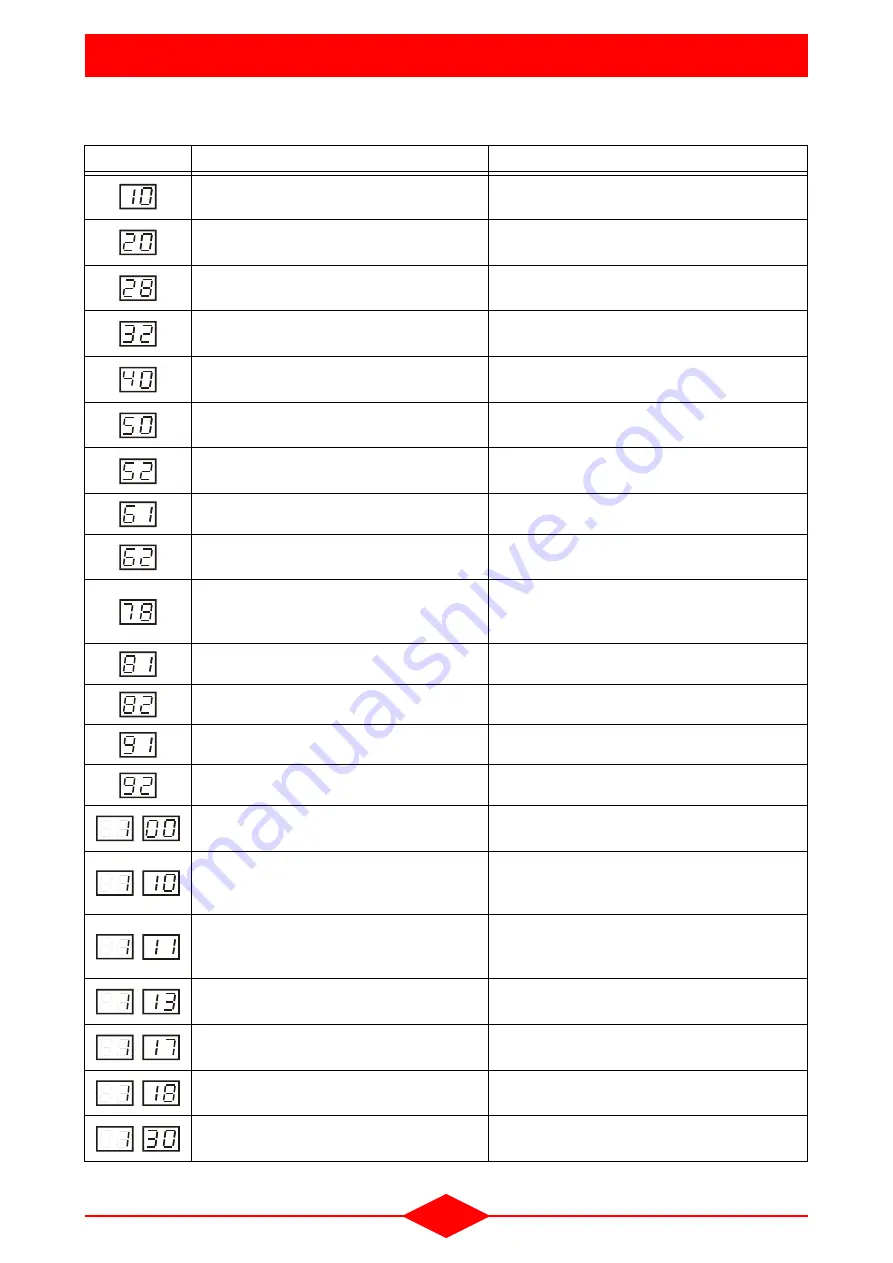
- 63 -
IX - OPERATING FAULTS
Display
Description
Solution
Outside sensor fault
Check that the sensor is correctly fitted and
connected
Boiler sensor 1 fault
Check that the sensor is correctly fitted and
connected
Flue gas detector fault
Check that the sensor is correctly fitted and
connected
Flow sensor 2 fault
Check that the sensor is correctly fitted and
connected
Return sensor 1 fault
Check that the sensor is correctly fitted and
connected
Domestic hot water sensor 1 fault
Check that the sensor is correctly fitted and
connected
Domestic hot water sensor 2 fault
Check that the sensor is correctly fitted and
connected
Room device 1 faulty
Check the boiler connections
Room device 1 error or radio clock error
Check compatibility of the room device or
clock
Water pressure sensor fault
Increase the pressure in the circuit
(if P < 0.2 bar), check the connections of the
pressure sensor
Short-circuit on LPB or no voltage
Check the wiring
Two identical addresses on the LPB
Check the addressing
Loss of data in the EEPROM
Change the LMU
Component fault in the LMU
Change the LMU
Two master clocks (only one normally),
programming problem
Check parameter 96 of the QAA73 (only one
device can have the message “QAA73”)
STB (boiler overheating safety) activated
Check that shunt X3-01 is present and
whether the installation water flow is sufficient
(circulating pump, isolation valve, etc.)
Response of the safety thermostat
Check whether the installation water flow is
sufficient (circulating pump, isolation valve,
etc.)
Flue gas alarm displayed (problem of the
flue gas temperature being too high)
Check whether the boiler is not on thermal
overload or that the exchanger is not clogged
Water pressure too high
Check and adjust the pressure level if
necessary with P < 4 bar
Water pressure too low
Check and adjust the pressure level if
necessary with P > 0.4 bar
Maximum flue gas temperature exceeded
Check whether the boiler is not on thermal
overload or that the exchanger is not clogged
Summary of Contents for THI 5-25c
Page 62: ... 77 NOMENCLATURE THI 5 25 C ...
Page 65: ... 98 NOMENCLATURE CONTROL BOX ...