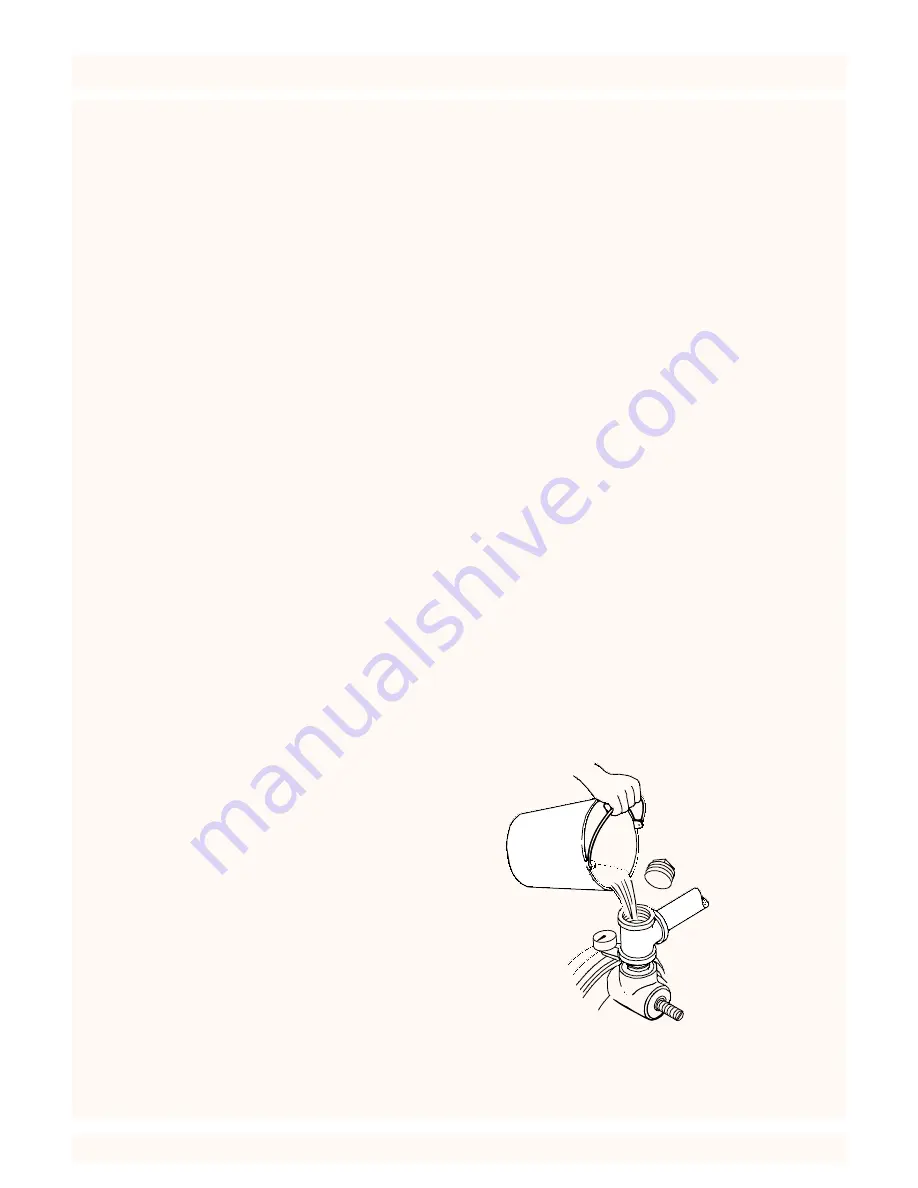
INSTALLATION
STEEL PIPING INSTALLATIONS
When steel pipe is used to install the jet, be sure all pipes
are clean and the ends are reamed. Screw both 1-1/4” NPT
suction pipe and 1’’ NPT drive pipe directly into the jet
body. The special adapter nipple furnished with the jet is
not used on steel pipe installations, and should be discarded.
Add sufficient piping, using pipe thread compound on the
joints until proper depth is reached.
NOTICE:
Pipe compound can damage plastic components
in pump. Use only Teflon tape or Plasto-Joint Stik1 when
connecting pipe to pump.
SINGLE PIPE JETS - 2” OR 3” WELLS
Before installing jet in well, it is necessary to soften jet
leathers by soaking in water for a minimum of one hour.
Single pipe jets must be installed with steel suction piping
in the well. Make sure all pipes are clean and ends are
reamed before lowering any piping into the well. Look
through pipe to make certain there are no obstructions.
During the process of lowering pipe into the well, always in-
stall coupling on top end of pipe and above clamp. This will
prevent accidental dropping of pipe into well.
Attach the jet to the first length of suction pipe 1-1/4” (NPT).
Use turned couplings (furnished) on 2” wells. Standard cou-
plings may be used for suction piping on 3” wells. Use pipe
compound on male threads only.
Tighten each length of pipe as it is lowered into the well.
Lower it to proper depth which is 10-15 feet below the
drawdown water level. This is the level to which the water
will drop while the well is being pumped continuously.
NOTICE:
Due to normal irregularities in the leather of the
cup seals and the inner walls of the drop pipe, 2” packer jets
do not form a perfect seal. In a dormant system, water will
leak back into well over time and pump will normally start
and cycle to maintain system pressure level.
PRIMING PIPE (OR PIPES) IN WELL
Fill piping in well with water as each length is added, or after
piping is complete in well. This serves to double check for
leaks in piping and foot valve, and simplifies final priming of
pump.
INSTALLING CASING ADAPTER
Slide adapter on to well casing as far as it will go. Tighten
three bolts to seal the adapter to the casing. Place a 1” nip-
ple of proper length in the drive pipe opening in the casing
adapter, and tighten top nuts. This will seal the glands on to
both suction and drive piping. Add elbows and flexible pipe
adapters for horizontal installations.
1
Lake Chemical Co., Chicago, Illinois.
SHALLOW WELL INSTALLATION
AND OPERATION
Installing the Pump on a Shallow Well
A shallow well jet is available for use when the SEARS jet
pump is installed on wells 20 feet or less to drawdown water
level.
Install this jet as follows:
a. Loosen the stainless steel clamp until it fits over the flange
on the jet body.
b. Place O-Ring in circular groove on face of suction-drive
line flange. If necessary, use petroleum jelly to hold in
place.
c. Venturi that protrudes from the jet body must be inserted
in top (1-1/4” NPT) tapping. For ease of assembly, lubri-
cate the small O-Ring on the end of the venturi and push
the shallow well jet assembly into place.
d. Align lugs on jet body with slots in pump.
e. Place clamp over the flanges and tighten securely.
For standard tank installations, an air volume control is nec-
essary and is connected to the 1/8” tapping in the jet body.
Connect as shown in installation drawing, Figure 4, Page 5.
PIPING IN THE WELL
A shallow well jet pump can be installed on a dug well,
drilled well or with a driven point. SEARS shallow well jet
pumps have a built-in check valve. In a dug or cased well, a
foot valve and strainer is recommended and should be in-
stalled 5 to 10 feet below the lowest level to which the water
will drop while the pump is operating (pumping water
level). See Figure 4, Page 5. Your well driller can furnish this
information. The strainer should not be too close to the bot-
tom, or sediment may clog it. Before installing foot valve,
check to see if it works freely.
When using a foot valve, a priming tee and a plug as shown
in Figure 7 is recommended.
7
182 0893
Figure 7