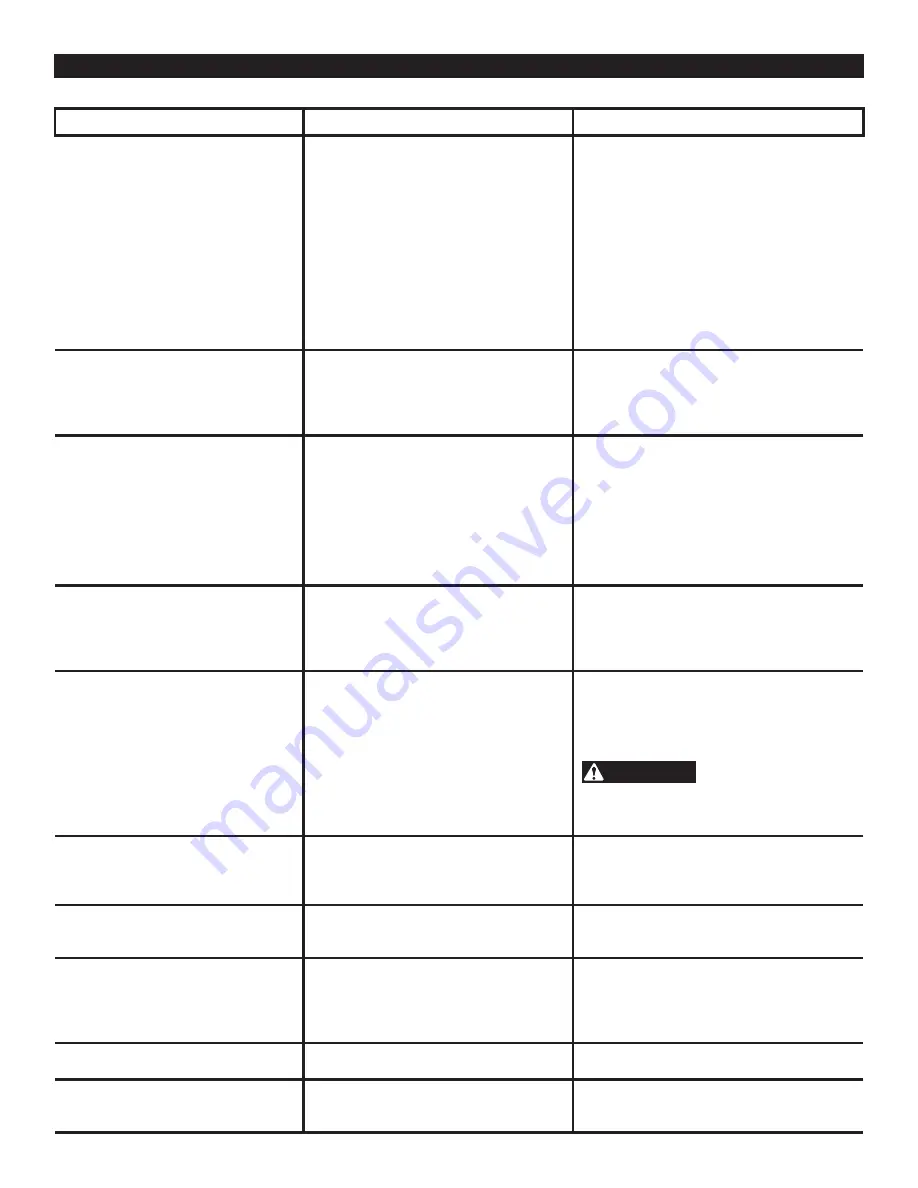
13
Problem
Possible Cause
Solution
The compressor does not run.
1. Loss of power or overheating.
2. There is no electrical power being
supplied to compressor or, the power
switch is in the OFF position.
3. A fuse has blown at the power supply.
4. A breaker has tripped at the power
supply.
5. Thermal overload open.
6. The pressure switch is bad.
7. Tank is full of air.
1. Check for proper use of extension cord.
2. Check to be sure the compressor is plugged
in and the power switch is in the ON position.
3. Replace the fuse at the power supply.
4. Reset the breaker at the power supply and
determine why the problem happened.
5. First unplugged the compressor and wait
until it becomes cool. Motor will restart when
cool.
6. Replace the pressure switch.
7. Compressor will turn on when tank pressure
drops to cut-in pressure.
The motor hums, but does not run or
runs slowly.
1. The voltage from the power supply is low.
2. The gauge wire or the length of extension
cord is wrong.
3. The motor winding is shorted or broken.
4. The unloader or check valve is defective.
1. Check the voltage with a voltmeter.
2. Use the correct wire gauge and length
extension cord.
3. Take the compressor to a service center.
4. Take the compressor to a service center.
The fuses blow or the circuit breaker
trips repeatedly.
1. The fuse size is incorrect or the circuit is
overloaded.
2. The gauge wire or the length of extension
cord is wrong.
3. The unloader or check valve is defective.
1. Check the fuse or breaker at the power
supply is the correct size and type. Be
sure to use only time-delay fuses to avoid
overloading a curcuit, disconnect other
electrical appliances from circuit or operate
compressor on its own branch circuit.
2. Use the correct wire gauge and length
extension cord.
3. Take the compressor to a service center.
The thermal overload protector cuts out
repeatedly.
1. The voltage from the power supply is low.
2. A poorly ventilated room is causing the
motor to overheat.
3. The gauge wire or the length of extension
cord is wrong.
1. Check the voltage with a voltmeter.
2. Move the compressor to well-ventilated area.
3. Check for proper gauge wire and cord
length.
The air receiver pressure drops when
the compressor shuts off.
1. The connections are loose or leaking
(fittings, tubing, etc.).
2. The drain valve is loose.
3. The check valve is leaking.
1. Check all the connections with soapy water
and look for bubbles. Tighten any loose
conections until the leak stops.
2. Tighten the drain valve.
3. Take the compressor to a service center.
Do not disassemble
check valve while air is in tank - empty
the all the air out of the tank before
dissasembly.
There is excessive moisture in the air
discharge.
1. There is excessive water in the air tank.
2. The humidity is high.
1. Drain the tank to remove water.
2. Move the compressor to an area of less
humidity or use an air line filter to reduce
moisture discharge in the tank.
Air is leaking from the compressor.
1. The hose connection is loose or
improperly sealed.
2. The air hose is broken or damaged.
1. Ensure connections are sealed with thread
sealing tape and tightened.
2. Replace the air hose.
The compressor runs continuously
1. The tank drain valve is open.
2. The pressure switch is defective.
3. The usage is excessive.
1. Ensure the tank drain valve is closed.
2. Take the compressor to a service center.
3. Decrease the amount of tool run-time; the
compressor is not large enough to supply the
air requirement of the tool.
The compressor vibrates.
1. The compressor mounting bolts are
loose.
1. Tighten mounting bolts.
The air output is lower than normal.
1. The inlet valves are broken.
2. The connections are leaking.
1. Take the compressor to a service center.
2. Apply thread sealing tape to fitting and
tighten.
WARNING
TROUBLESHOOTING
Summary of Contents for 107.10265
Page 27: ...27 ...