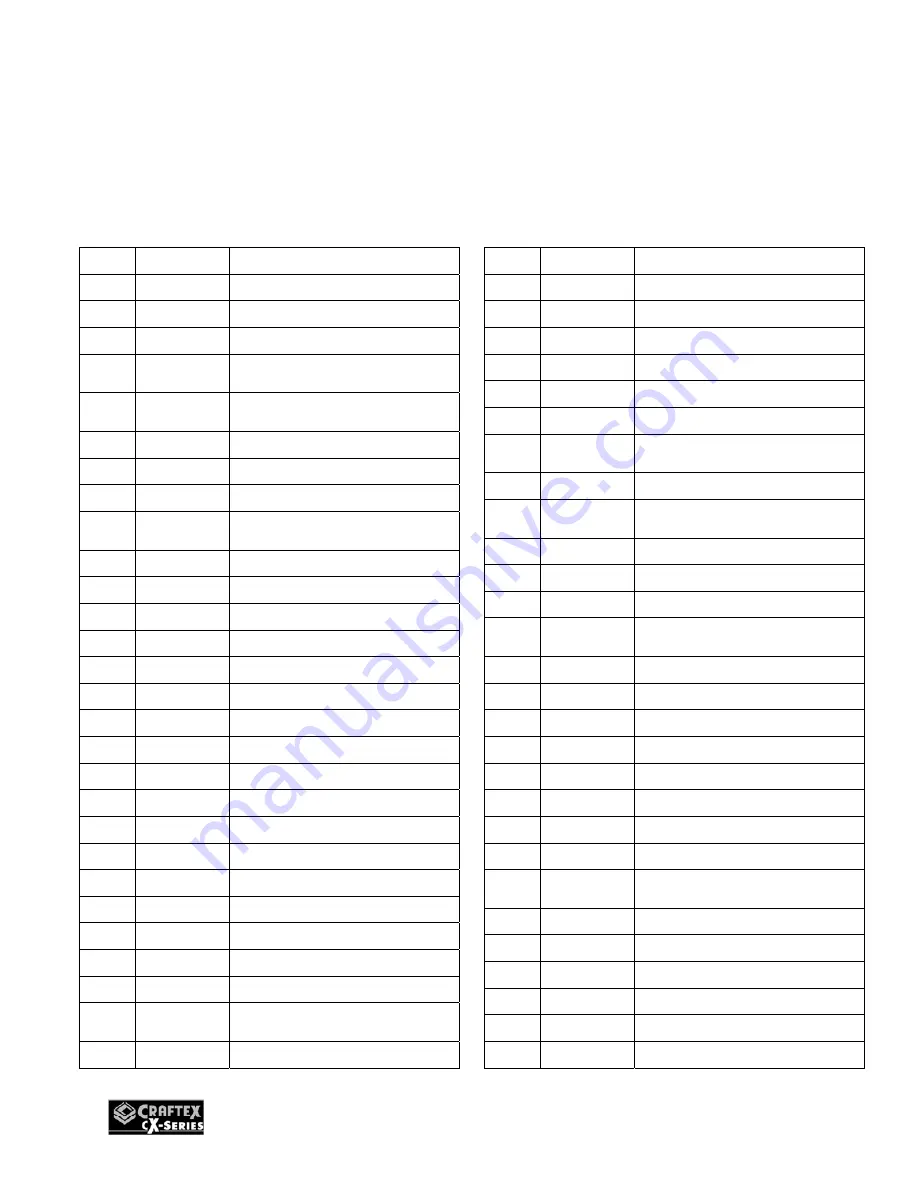
20
1 DJ-001 KNOB
2 DJ-002 STUD
3 DJ-003 BUSHING
4 DJ-004 ECCENTRIC
SHAFT
5 GB80
M6X16MM HEX SOC SET
SCR.
6 GB80
M8X12MM HEX SOC SET
SCR.
7 DJ-005 FENCE
CARRIAGE
8 GB6170
M6
HEX
NUT
9
GB5782
M6X25 HEX BOLT
10
FENCE CARRIAGE
WARNING LABEL
11 GB827 RIVET
12 DJ-008 COLLAR
13 DJ-012 SUPPORT
14 DJ-014 WASHER
12.7X38X5
15 GB6170 M12
HEX
NUT
16
GB70
M10X30MM SOC HD SCR
17 DJ-013 WASHER
10.4X30X3
18
GB70
M5X16MM SOC HD SCR
19 DJ-009 GIB
20 DJ-010 ECCENTRIC
STUD
21 DJ-011 WASHER
8.4X25X3
22 GB6170 M8
HEX
NUT
23 DJ-007 SHAFT
24
GB70
M8X30 SOC HD SCR
25 DJ-016 WASHER
6.5X16X3
26 DJ-015 POINTER
27 GB97
Φ
6MM FLAT WASHER
28 GB65
M6X16MM CHEESE HD
SCR
29 DJ-018 LOCK
LEVER
30 DJ-019 INDES
PIN
ASSEMBLY
31
GB879
3X20MM ROLL PIN
32 DJ-020 SPRING
33
GB5782
M6X25 HEX BOLT
34 GB6170 M6
HEX
NUT
35 DJ-017 SWIVEL
36 DJ-021 COLLAR
37 GB80
M8X12MM HEX SOC SET
SCR.
38 DJ-022 LOCK
39 GB80
M8X12MM HEX SOC SET
SCR.
40 DJ-023 CLAMP
41 DJ-024 THREAD
CLAMP
42 DJ-025 TILT
SCALE
43 GB65
M6X10MM CHEESE HD
SCR
44 GB97
Φ
6MM FLAT WASHER
45 DJ-026 BALL
HANDLE
46 DJ-027 STUD
47 DJ-028 FENCE
48 DJ-029 SCALE
49 GB827 RIVET
50 DJ-030B TABLE
RH
51 DJ-044B TABLE
SHAFT
52 DJ-032B
RABBETING TABLE
EXTENSION
53
GB70
M6X20MM SOC HD SCR
54 DJ-033B CHIP
DEFLECTOR
55
GB70
M6X12MM SOC HD SCR
56
GB70
M8X80MM SOC HD SCR
57 GB93 M8
LOCK
WASHER
58
DJ-034B
BEARING BLOCK LH
CX08HC JOINTER
TABLE PARTS LIST
REF# PART# DESCRIPTION
REF# PART# DESCRIPTION