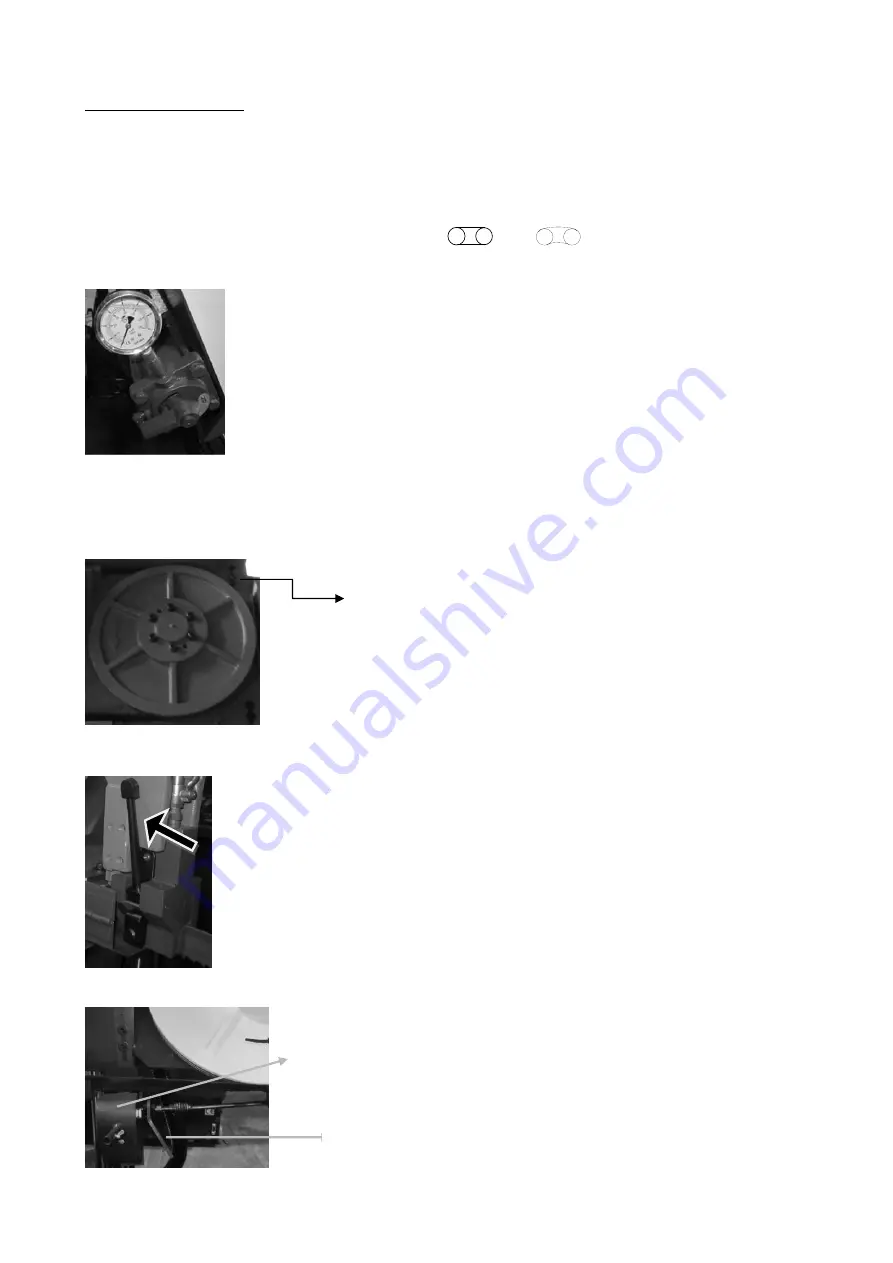
4
‐
11
Installing
a
new
blade
Step
1
‐
Select
the
most
suitable
saw
blade
for
your
workpiece
considering
the
size,
shape
and
material.
Step
2
‐
Turn
on
the
machine
power
by
switching
to
ON
and
turn
on
the
hydraulic
system.
Step
3
‐
Press
the
saw
bow
up
button
and
elevate
the
saw
bow
to
an
appropriate
height.
Step
4
‐
Turn
the
tension
controller
handle
from
“
”
to
“
”
position
to
release
tension.
The
idle
wheel
will
then
move
slightly
toward
the
direction
of
the
drive
wheel.
Step
5
‐
Open
the
idle
and
drive
wheel
covers.
Step
6
‐
Press
the
Blade
Clip
device
to
hold
onto
the
blade.
This
device
makes
blade
changing
easy
and
feasible
even
with
only
one
operator
available.
Step
7
‐
Loosen
the
left
and
right
carbide
inserts
by
unlocking
the
“lock
bars”
shown
below.
Step
8
‐
Open
the
wire
brush
cover.
Loosen
the
lock
lever
and
lower
the
wire
brush.
Easy
Blade
Replacement
Device
Lock
Lever
Wire
Brush
Case
Summary of Contents for SH-5542
Page 2: ......
Page 8: ......
Page 13: ...1 5 Illustration Emergency Stop Emergency Stop ...
Page 15: ...1 7 Illustration Safety Labels ...
Page 20: ...2 4 FLOOR PLAN Machine top view Machine front view ...
Page 21: ...2 5 Machine side view ...
Page 22: ......
Page 32: ......
Page 48: ......
Page 50: ...5 2 ...
Page 51: ...5 3 ...
Page 52: ...5 4 ...
Page 53: ...5 5 ...
Page 54: ...5 6 張 鴻 昌 1030821 ...
Page 55: ...5 7 1030823 張 鴻 昌 ...
Page 56: ...5 8 1030823 張 鴻 昌 ...
Page 57: ...5 9 1030823 張 鴻 昌 ...
Page 58: ......
Page 59: ...6 1 Section 6 HYDRAULIC SYSTEM HYDRAULIC CIRCUIT DIAGRAM ...
Page 60: ...6 2 ...
Page 66: ......
Page 78: ...10 2 ...
Page 79: ...10 3 ...
Page 80: ...10 4 ...
Page 82: ...10 6 ...
Page 83: ...10 7 ...
Page 84: ...10 8 ...
Page 85: ...10 9 ...
Page 86: ...10 10 ...
Page 87: ...10 11 ...
Page 88: ...10 12 ...
Page 89: ...10 13 ...
Page 90: ...10 14 ...
Page 91: ...10 15 ...
Page 92: ...10 16 ...
Page 93: ...10 17 ...
Page 94: ...10 18 ...
Page 95: ...10 19 ...
Page 96: ......
Page 98: ......
Page 99: ......