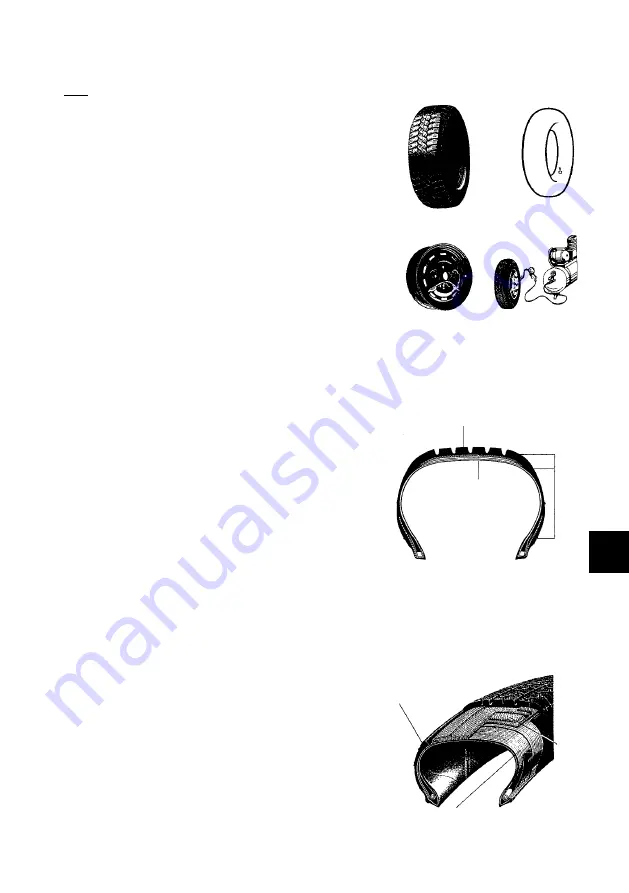
Artiglio Master Code
User Manual
109
UK
3
5
9
13. GlossARY
Tyre
A tyre consists of:
I-the actual tyre,
II- the rim
(wheel),
III-the air chamber
(in tube type tyres),
IV-pressurised air.
The tyre must:
- withstand a load,
- ensure driving power,
- steer the vehicle,
- aid handling and braking,
- aid vehicle suspension.
I - Tyre
The actual tyre is the main part of the overall
tyre in contact with the road and is therefore designed
to withstand internal air pressure and all other stress
arising from use.
A tyre section shows the various parts it consists of:
1 - The tread
. This is the part in contact with the ground
when the tyre rolls. It comprises a rubber compound and
a “pattern” that is suitable for ensuring good resistance
to abrasion and good grip in dry and wet conditions, as
well as quiet operating conditions.
2 - Edge or bracing
. This is a metal fabric or textile insert,
in the area of the outer bead part. It protects the casing
plys from rubbing against the rim.
3 - Casing
. This is the resistant structure and comprises
one or more layers of rubber plys. The way the plys
comprising the casing are arranged give the structure
its name. The following structures are possible:
Conventional:
the plys are inclined and arranged so that
the strands comprising a ply overlap with those of the
adjacent ply. The tread, which is the part of the tyre in
contact with the ground, is part of the sidewalls and so
during rolling, sidewall flexure is transmitted to the tread.
Radial:
the casing consists of one or more plys with the
cords in a radial direction.
A radial casing in itself is quite unstable. To make it
stable and prevent bad tread movement in the area of
contact with the ground, the casing and the undertread
are reinforced with an annular structure, usually called
belt. The tread and sidewall work with different, inde-
pendent rigidities, so during rolling, sidewall flexure is
not transmitted to the tread.
4 - Side ring.
This is a metal ring comprising several steel
strands. The casing plys are secured to the side ring.
I
III
II
IV
1
12
13
8
Summary of Contents for Artiglio Master Code
Page 13: ...Artiglio Master Code User Manual 13 UK 1 5 6 7 8 9 11 12 14 15 16 7 18 12...
Page 114: ...114 Artiglio Master Code User Manual M13 M14 M11 M7 M2 M9 A M16 STANDARD RIM...
Page 115: ...Artiglio Master Code User Manual 115 UK M6 M5 M11 M7 M9 B M16 DROPPED CENTRE HOLE RIM...
Page 116: ...116 Artiglio Master Code User Manual C M11 M2 REVERSED RIM...
Page 117: ...Artiglio Master Code User Manual 117 UK D M10 M2 M15 M9 PICK UP RIM...
Page 118: ...118 Artiglio Master Code User Manual E CLOSED CENTRE RIM...
Page 119: ...Artiglio Master Code User Manual 119 UK F OPEN CENTRE RIM with delicate hole edges...
Page 120: ...Notes 120...
Page 123: ...Artiglio Master Code User Manual 123 UK 81...
Page 124: ...124 Artiglio Master Code User Manual...
Page 125: ...Artiglio Master Code User Manual 125 UK 82...
Page 126: ...126 Artiglio Master Code User Manual 83...
Page 127: ...Artiglio Master Code User Manual 127 UK 84...
Page 128: ...128 Artiglio Master Code User Manual 85...
Page 129: ...Artiglio Master Code User Manual 129 UK 86...
Page 134: ...Notes 134...
Page 135: ...Notes 135...