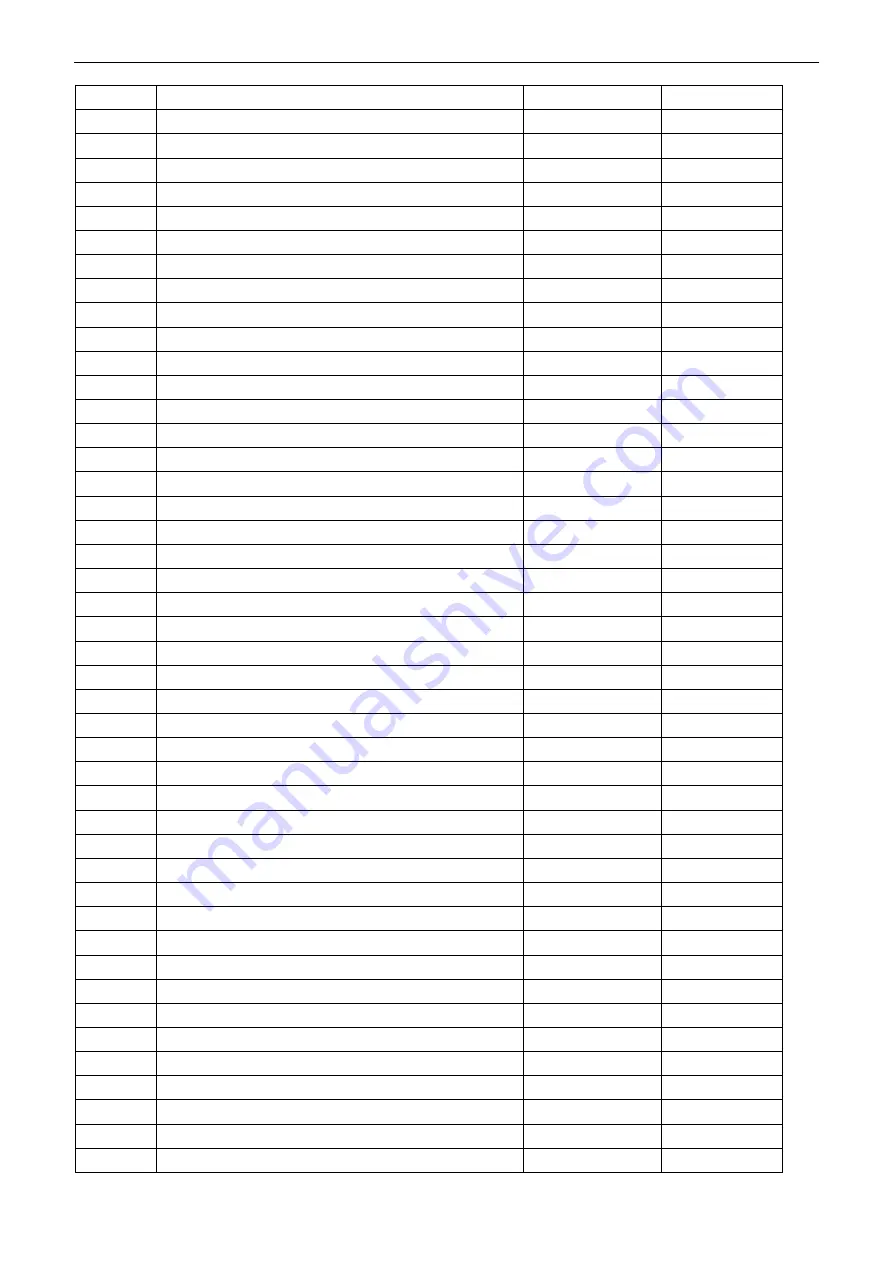
Rooftop Packaged Service Manual MAINTENANCE
102
8
Brushless DC Motor
'016001000009
1
9
Blower(Right)
'4304000425
1
10
Filter Sub-Assy
'4304000430
1
11
Evaporator Assy
'43000054
1
12
Bidirection Strainer
'00204100003
2
13
Electric Box Assy
'06130002
3
14
Radiator 2
'76710247
3
15
Radiator 1
'4304413214
1
16
Main Board
'4304413220
1
17
Rectifier
'43044100190
2
18
Electric Box Assy
'04324001
1
19
Radiator
'4602001535
1
20
Radiator
'4304000402
1
21
Main Board
'43000072
1
22
Terminal Board
'07220019
1
23
Terminal Board
'4602001587
1
24
Main Board
'07130118
2
25
Filter Board
'4304000414
1
26
Main Board
'43003091
2
27
Handle
'4602001531
1
28
Side Plate 2
'4304000413
1
29
Reactor
'07219056
1
30
Phase Reverse Protector
'07220016
1
31
AC Contactor
'4300040030
1
32
Main Board
'072007000003
1
33
Main Board
'011002000196
1
34
Side Plate 1
'016001000008
1
35
Reactor
'07424188
1
36
Rear Grill 1
'07423204
1
37
Base Frame Sub-Assy
'017000000083P
1
38
Chassis sub-assy 1
'017055000032P
1
39
Water Tray Sub-Assy
'017000000084P
1
40
Chassis Sub-Assy 2
'017033000008
1
41
Oil Separator
'016001000007
1
42
Gas-liquid Separator
'4313017403
2
43
Grill 2
'012010000097P
1
44
Condenser Assy
'300027000088
1
45
4-Way Valve
'300027000021
1
46
Magnet Coil
'44010245
1
47
Bidirection Strainer
'32214101
1
48
Filter
'43130189
1
49
Magnet Coil
'012010000096P
1
50
Pressure Switch
'26235253
6
51
Electromagnetic Valve
'30223000032
2
52
Magnet Coil
'30223000118
2
Summary of Contents for CH-IRT05NM
Page 4: ...Rooftop Packaged Service Manual PRODUCT 1 PRODUCT ...
Page 10: ...Rooftop Packaged Service Manual CONTROL 7 CONTROL ...
Page 12: ...Rooftop Packaged Service Manual CONTROL 9 1 2 HEATING OPERATION ...
Page 36: ...Rooftop Packaged Service Manual INSTALLATION 33 INSTALLATION ...
Page 39: ...Rooftop Packaged Service Manual INSTALLATION 36 CH IRT08NM CH IRT15NM ...
Page 49: ...Rooftop Packaged Service Manual INSTALLATION 46 CH IRT15NM CH IRT15NM ...
Page 50: ...Rooftop Packaged Service Manual MAINTENANCE 47 MAINTENANCE ...
Page 110: ...Cooper Hunter International Corporation www cooperandhunter com ...