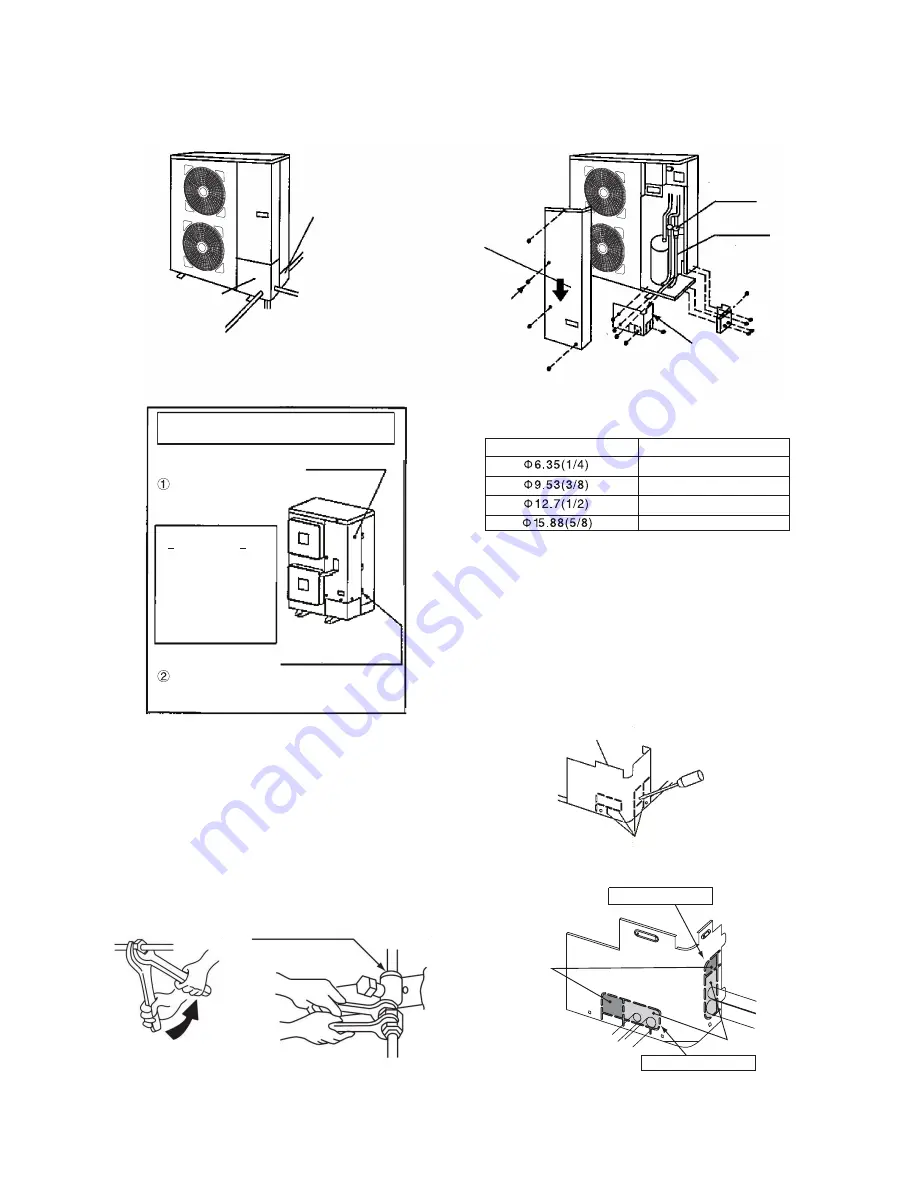
Front Side Piping Cover
(4) Pipes can be connected from 4 directions
Tightening Torque for Flare Nut
Pipe Size
Right Side Piping Work
5.4 Piping Connection
Pipes can be connected from 4 directions.
Rear Side
Piping Cover
(Knock-Out Hole)
Rear Side Piping Work
(Knock-Out Hole)
(Knock-Out Hole)
Right Side Piping Work
Bottom Side
Piping Work
(Knock-Out Hole)
Front Side
Piping Work
(Knock-Out Hole)
Front Side Piping Cover
Fig. 5.1 Piping Direction
Front Side Piping Cover
Stop Valve
Distribution
Pipe
Remove Direction of
Service Cover
Note Item for Remove Service Cover
Main Points for Remove
Service Cover
Service Cover
Remove the bolts of
service cover follow
Note
Press the service cover
right Fig.
when remove the bolts.
It is possible for service
cover to slide down.
Fix Hook (3 Points)
Fig. 5.2 Remove Service Cover
(1) Confirm that the valve is closed.
(2) Prepare a field-supplied bend pipe for
liquid line. Connect it to the liquid valve by
flare nut through the square hole of bottom
base.
(3) For Gas Piping Connection
Prepare a field-supplied bend pipe for gas
line. Braze it and the factory-supplied pipe
flange at the outside of the unit.
Do not apply the double
spanner work here.
Refrigerant leakage shall
occur.
Double Spanner Work
Tightening Work for Stop Valve
Table 5.8
as shown Fig. 5.1. Make a knock-out hole
in the front pipe cover or bottom base to
pass through the hole.
After removing the pipe cover from the unit,
punch out the holes following the guide line
with screwdriver and a hammer.
Then, cut the edge of the holes and attach
insulation (Field-Supplied) for cables and
pipes protection.
Gap
Connect Front and Right Side Pipe
B
A
Front Side Piping Hole
Right Side Piping Hole
Press the service cover at front,
then remove it down slowly.
12
( )
Torque
14.7 ft ·lbs (20 N·m)
29.5 ft ·lbs (40 N·m)
44.3 ft ·lbs (60 N·m)
59.0 ft ·lbs (80 N·m)
Summary of Contents for CHV6-36URBM
Page 31: ...26 Table 8 1 Checking of Wire Connection by Test Run...
Page 32: ...SPWT J01 27 7...
Page 34: ...able 8 3 Alarm Code T 29...