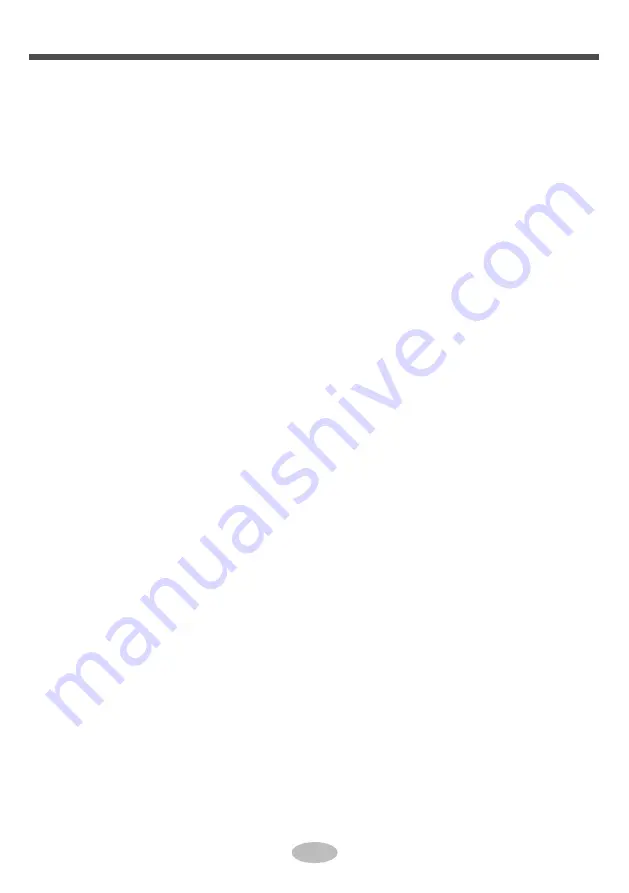
Specialist’s Manual
fire extinguishing equipment shall be available to
hand. Have a dry powder or CO
2
fire extinguisher
adjacent to the charging area.
The following checks shall be applied to instal-
lations using flammable refrigerants:
– the charge size is in accordance with the room size
within which the refrigerant containing parts are in-
stalled;
– the ventilation machinery and outlets are operat-
ing adequately and are not obstructed;
– if an indirect refrigerating circuit is being used, the
secondary circuit shall be checked for the presence
of refrigerant;
– marking to the equipment continues to be visible
and legible. Markings and signs that are illegible shall
be corrected;
– refrigeration pipe or components are installed in a
position where they are unlikely to be exposed to any
substance which may corrode refrigerant contain-
ing components, unless the components are const-
ructed of materials which are inherently resistant to
being corroded or are suitably protected against be-
ing so corroded.
Repair and maintenance to electrical compo-
nents shall include initial safety checks and com-
ponent inspection procedures. If a fault exists
that could compromise safety, then no electrical
supply shall be connected to the circuit until it
is satisfactorily dealt with. If the fault cannot
be corrected immediately but it is necessary
to continue operation, an adequate temporary
solution shall be used. This shall be reported
to the owner of the equipment so all parties are
advised.
●
Initial safety checks shall include:
– that capacitors are discharged: this shall be done
in a safe manner to avoid possibility of sparking;
– that no live electrical components and wiring are
exposed while charging, recovering or purging the
system;
– that there is continuity of earth bonding.
●
Checking for presence of refrigerant
The area shall be checked with an appropriate refri-
gerant detector prior to and during work, to ensure
the technician is aware of potentially toxic or flamm-
able atmospheres. Ensure that the leak detection
equipment being used is suitable for use with all app-
licable refrigerants, i.e. non-sparking, adequately seal-
ed or intrinsically safe.
●
Presence of fire extinguisher
If any hot work is to be conducted on the refrigera-
tion equipment or any associated parts, appropriate
●
●
Ventilated area
Ensure that the area is in the open or that it is ad-
equately ventilated before breaking into the system
or conducting any hot work. A degree of ventilation
shall continue during the period that the work is carri-
ed out. The ventilation should safely disperse any re-
leased refrigerant and preferably expel it externally
into the atmosphere.
●
Checks to the refrigeration equipment
Where electrical components are being changed,
they shall be fit for the purpose and to the correct
specification. At all times the manufacturer's main-
tenance and service guidelines shall be followed. If
in doubt, consult the manufacturer's technical depart-
ment for assistance.
●
Checks to electrical devices
– that capacitors are discharged: this shall be done
in a safe manner to avoid possibility of sparking;
– that no live electrical components and wiring are
exposed while charging, recovering or purging the
system.
●
Repairs to sealed components
During repairs to sealed components, all electrical
supplies shall be disconnected from the equipment
being worked upon prior to any removal of sealed
covers, etc. If it is absolutely necessary to have an
electrical supply to equipment during servicing, then
a permanently operating form of leak detection shall
be located at the most critical point to warn of a
potentially hazardous situation.
Particular attention shall be paid to the following to
ensure that by working on electrical components, the
casing is not altered in such a way that the level of
protection is affected. This shall include damage to
cables, excessive number of connections, terminals
not made to original specification, damage to seals,
incorrect fitting of glands, etc.
– Ensure that the apparatus is mounted securely.
– Ensure that seals or sealing materials have not de-
graded to the point that they no longer serve the pur-
pose of preventing the ingress of flammable atmos-
pheres. Replacement parts shall be in accordance
with the manufacturer’s specifications.
NOTE:The use of silicon sealant can inhibit the
effectiveness of some types of leak detection equi-
pment. Intrinsically safe components do not have to
be isolated prior to working on them.
●
28
Specialist’s Manual
Repair to intrinsically safe components
Do not apply any permanent inductive or capaci-
tance loads to the circuit without ensuring that this
will not exceed the permissible voltage and current
permitted for the equipment in use.
Intrinsically safe components are the only types that
can be worked on while live in the presence of a fl-
ammable atmosphere. The test apparatus shall be
at the correct rating.
Replace components only with parts specified by the
manufacturer. Other parts may result in the ignition
of refrigerant in the atmosphere from a leak.
●
Cabling
Check that cabling will not be subject to wear, cor-
rosion, excessive pressure, vibration, sharp edges
or any other adverse environmental effects. The
check shall also take into account the effects of
aging or continual vibration from sources such as
compressors or fans.
●
Detection of flammable refrigerants
Under no circumstances shall potential sources of
ignition be used in the searching for or detection of
refrigerant leaks. A halide torch (or any other detec-
tor using a naked flame) shall not be used.
●
Leak detection methods
Leak detection fluids are suitable for use with most
refrigerants but the use of detergents containing ch-
lorine shall be avoided as the chlorine may react
with the refrigerant and corrode the copper pipe-work.
●
Decommissioning
Before carrying out this procedure, it is essential that
the technician is completely familiar with the equip-
ment and all its detail. It is recommended good pr-
actice that all refrigerants are recovered safely.
Prior to the task being carried out, an oil and refri-
gerant sample shall be taken in case analysis is re-
quired prior to re-use of reclaimed refrigerant. It is
essential that electrical power is available before
the task is commenced.
a) Become familiar with the equipment and its opera-
tion.
b) Isolate system electrically.
c) Before attempting the procedure, ensure that:
– mechanical handling equipment is available, if
required, for handling refrigerant cylinders;
– all personal protective equipment is available
and being used correctly;
– the recovery process is supervised at all times
by a competent person;
●
d) Pump down refrigerant system, if possible.
e) If a vacuum is not possible, make a manifold so
that refrigerant can be removed from various parts
of the system.
f) Make sure that cylinder is situated on the scales
before recovery takes place.
g) Start the recovery machine and operate in accor-
dance with manufacturer's instructions.
h) Do not overfill cylinders. (No more than 80% vo-
lume liquid charge).
i) Do not exceed the maximum working pressure of
the cylinder, even temporarily.
j) When the cylinders have been filled correctly and
the process completed, make sure that the cylinders
and the equipment are removed from site promptly
and all isolation valves on the equipment are closed
off.
k) Recovered refrigerant shall not be charged into
another refrigeration system unless it has been clean-
ed and checked.
Labelling
●
Recovery
When removing refrigerant from a system, either
for servicing or decommissioning, it is recommend-
ed good practice that all refrigerants are removed
safely.
When transferring refrigerant into cylinders, ensure
that only appropriate refrigerant recovery cylinders
are employed. Ensure that the correct number of cy-
linders for holding the total system charge are av-
ailable. All cylinders to be used are designated for
the recovered refrigerant and labelled for that refri-
gerant (i.e. special cylinders for the recovery of refri-
gerant). Cylinders shall be complete with pressure-re-
lief valve and associated shut-off valves in good work-
ing order. Empty recovery cylinders are evacuated
and, if possible, cooled before recovery occurs.
The recovery equipment shall be in good working
order with a set of instructions concerning the
equipment that is at hand and shall be suitable for
the recovery of all appropriate refrigerants includ-
ing, when applicable, flammable refrigerants. In ad-
●
– recovery equipment and cylinders conform to
the appropriate standards.
29
Equipment shall be labelled stating that it has been
de-commissioned and emptied of refrigerant. The
label shall be dated and signed. For appliances con-
taining flammable refrigerants, ensure that there are
labels on the equipment stating the equipment con-
tains flammable refrigerant.
Summary of Contents for Arctic NG Wi-Fi Series
Page 39: ...1 2 3 4 5 6 7...
Page 40: ...R32 R32 R32 R32 Xm2 a R32 1 2400 2483 5 2 20 R32 675...
Page 42: ...5 3...
Page 43: ...6...
Page 44: ...7 8...
Page 45: ...8...
Page 46: ...9 15 300 250 30 40 1 1 2 3 4 5 6 7 8 9 10 11 12 13 14 15 15...
Page 47: ...10 1 2 3 4 5 6 7 8 1 2 3 4 5 6 2 5 7 8 1 2 3 4 5 6 7 8 9 1 2 3 4 5 3...
Page 48: ...5 10 55 2 70 1 4 1 2 3 1 1 2 1 2 3 2 3 55 70 5 10 3 5 11 150 150 55 70 55 70...
Page 49: ...15 20 30 40 45 55 70 75 6 7 12 4 1 1 2 2 3...
Page 50: ...9 8 13 N 1 2 2 3 3 3 4 1 2 3 4 5 4 5 1 2...
Page 51: ...1 2 3 4 5 1 2 3 1 C5 F0 F1 F2 E1 E5 E6 E8 H6 U8 14 1 2 2 4 3 45 C...
Page 52: ...15 3 3 16 C 30 C 8...
Page 53: ...16 R R W W G O G O...
Page 54: ...17 8 C X FAN Wi Fi Timer ON Timer OFF I Feel...
Page 55: ...18 1 5 16 30 C 61 86 F X FAN 2 X FAN X FAN X FAN 2 X FAN FAN FAN FAN FAN...
Page 61: ...24 1 2 7 AAA 1 5 3 8...
Page 62: ...25 1 2 MODE 16 C...
Page 64: ...A C 6 6 35 1 4 1 3 0 7 9 9 52 3 8 12 12 7 1 2 1 8 1 0 15 8 16 5 8 2 4 2 2 27 B D E F A 1 6 1 0...
Page 65: ...28...
Page 66: ...29 80...
Page 67: ...30...
Page 68: ...31...
Page 69: ...50 50 200 30 30 32 30 40 1...
Page 71: ...3 34 1 4 3 2 1 2 1 2 1 2 3 1 2 3 20 2300 5000 6 6000 8000 8 10000 16000 10...
Page 73: ...Lo Hi Lo Hi 36 1 2 3 10 15 0 1 4 1 2 0 1 5 6 7 1 2 3 1 2 MODE 16 C...
Page 74: ...Cooper Hunter...
Page 76: ...1 2 3 4 5 6 7...
Page 77: ...R32 R32 R32 R32 Xm2 a R32 1 2400 2483 5 2 20 R32 675...
Page 79: ...5 3...
Page 80: ...6 c...
Page 81: ...7 8...
Page 82: ...8...
Page 83: ...9 15 15 300 250 30 40 1 1 2 3 4 5 6 7 8 9 10 11 12 13 14 15...
Page 84: ...10 1 2 3 4 5 6 7 8 1 2 3 4 5 6 2 5 7 8 1 2 3 4 5 6 7 8 9 1 2 3 4 5 3...
Page 85: ...5 10 2 3 2 2 3 55 2 70 1 4 1 3 1 5 1 1 11 150 150 2 3 55 70 5 10 55 70 55 70...
Page 86: ...15 20 30 40 45 55 70 75 4 1 2 2 6 7 1 12 3...
Page 87: ...3 1 5 2 3 4 9 4 2 3 8 1 13 N 1 2 2 3 4 5...
Page 88: ...2 1 2 3 4 3 4 5 1 1 2 3 C5 F0 F1 F2 E1 E5 E6 E8 H6 U8 2 1 14 45 C...
Page 89: ...15 3 8 3 16 C 30 C...
Page 90: ...16 R R W W G O G O...
Page 91: ...17 8 C X FAN Wi Fi I Feel...
Page 92: ...18 1 5 16 30 C 61 86 F X FAN 2 X FAN X FAN X FAN 2 X FAN FAN FAN FAN FAN...
Page 93: ...2 1 C F 2 Sleep 1 Sleep 2 Sleep 3 Sleep Sleep 1 1 1 2 19 2 2 2 2 2 2...
Page 98: ...24 AAA 1 5 8 1 2 3...
Page 99: ...25 1 2 ON OFF MODE 16 C...
Page 101: ...A C 6 6 35 1 4 1 3 0 7 9 9 52 3 8 12 12 7 1 2 1 8 1 0 15 8 16 5 8 2 4 2 2 27 B D E F A 1 6 1 0...
Page 102: ...28...
Page 103: ...29 80...
Page 104: ...30...
Page 105: ...31...
Page 106: ...50 50 200 30 30 32 30 40 1...
Page 108: ...3 34 1 2 3 1 1 2 3 2 2 1 1 2 3 3 20 2300 5000 6 6000 8000 8 10000 16000 10...
Page 110: ...1 2 1 1 2 7 Lo Hi 36 3 4 5 6 2 10 15 0 1 1 2 0 1 3 ON OFF MODE 16 C...
Page 111: ...Co o oo o oper Hu unter...