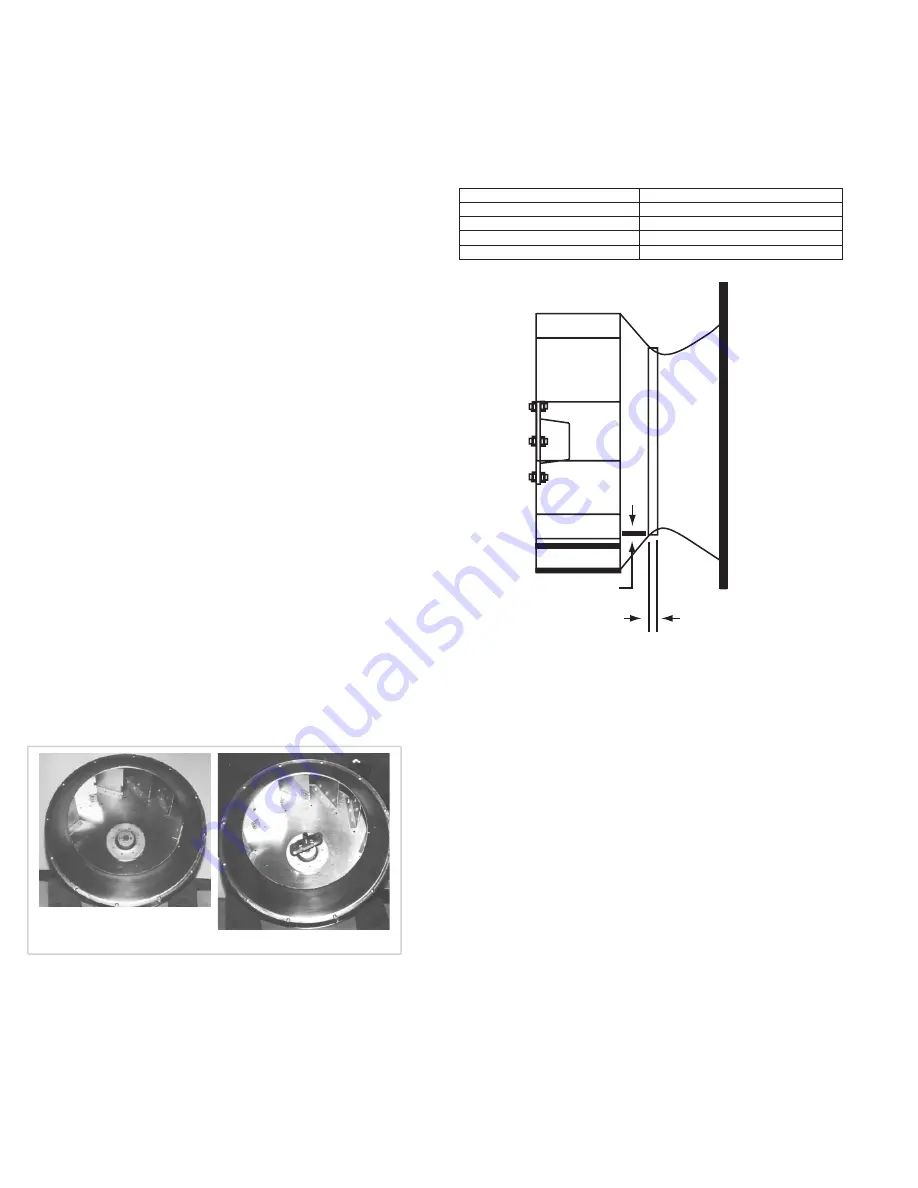
8
SQN IO&M
B51141-004
Bearing Replacement
The fan bearings are pillow block ball bearings.
1. Loosen screws on bearing cover.
2. Push bearing cover toward the wheel. As the bearing
cover moves toward the wheel it will slide down to re-
veal the bearings and shaft.
3. Remove the old bearing.
4. Remove any burrs from the shaft by sanding.
5. Slide new bearings onto the shaft to the desired lo-
cation and loosely mount bearings onto the bearing
support. Bearing bolts and setscrews should be loose
enough to allow shaft positioning.
6. Correctly position the wheel and tighten the bearing
bolts securely to the bearing support.
7. Align setscrews bearing to bearing and secure tightly
to the shaft.
NOTICE! Never tighten both pairs of setscrews before
securing bearing mounting bolts. This may damage
the shaft.
8. Inspect the wheel position again. If necessary, read-
just by loosening the bearing bolts and setscrews and
repeat from step 5.
Wheel Replacement
1.
Drill two 1/4” diameter holes, 180° apart centered ap
-
proximately between the shaft and the outside diam-
eter of the hub, 3/8” to 1/2” in depth.
2.
Tap 1/4” holes to 5/16” thread with a 5/16” hole tap. Do
not drill or tap greater than recommended.
3. Screw the puller arms to the full depth of the threads
into the tapped holes. Align center of the puller with
the center of the shaft. Ensure all setscrews in the
hub, normally two, are fully removed.
4. Slowly remove wheel from the shaft.
Recommended Puller
Lisle No. 45000 Sterling Wheel Puller. This puller is
available at most automotive parts retail outlets.
Wheel Replacement Components
Drilled hole placement.
Wheel puller.
Wheel-to-Inlet Clearance
The correct wheel-to-inlet clearance is critical to prop-
er fan performance. This clearance should be verified be
-
fore initial start-up since rough handling during shipment
could cause a shift in fan components. Refer to
Wheel/
Inlet
drawing for correct overlap.
Adjust the overlap by loosening the wheel hub and mov-
ing the wheel along the shaft to obtain the correct value.
A uniform radial gap (space between the edge of the
cone and the edge of the inlet) is obtained by loosening the
inlet cone bolts and repositioning the inlet cone.
Wheel/Inlet Overlap
Size
Maximum Overlap
100- 195
5/8”
210-270
3/4”
300-445
1”
490 730
1-1/4”
Radial Clearance
Overlap