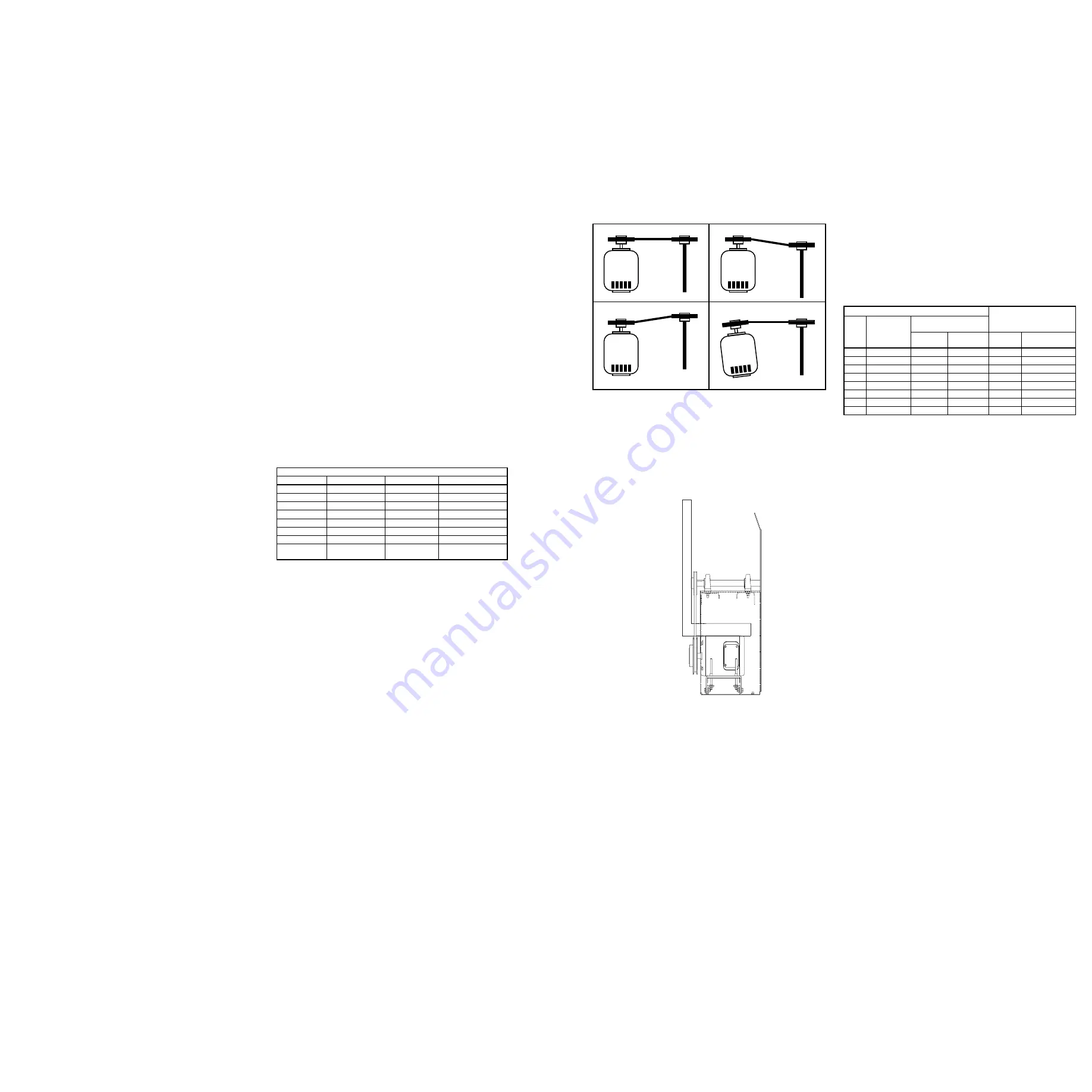
Pulley Alignment
Pulley alignment is adjusted by loosening the motor pul-
ley setscrew and by moving the motor pulley on the motor
shaft or by moving the entire motor along the motor mount-
ing bracket.
Figure 4
illustrates correct and incorrect pulley alignment.
A recommended method of inspecting the pulley alignment
with a square is shown below in
Figure 5
.
Final Installation Steps
a. Inspect fasteners and setscrews, particularly fan
mounting and bearing fasteners, and tighten according
to the recommended torque shown in the table
Rec-
ommended Torque for Setscrews/Bolts
.
b. Inspect for correct voltage with voltmeter.
c. Ensure all accessories are installed.
Operation
Pre-Start Checks
a. Lock out all the primary and secondary power sources.
b. Ensure fasteners and setscrews, particularly those
used for mounting the fan, are tightened.
c. Inspect belt tension and pulley alignment.
Correct
Incorrect
Incorrect
Incorrect
Figure 4
d. Inspect motor wiring.
e. Ensure belt touches only the pulleys.
f. Ensure fan and ductwork are clean and free of debris.
g. Inspect wheel-to-inlet clearance. The correct wheel-to-
inlet clearance is critical to proper fan performance.
h. Close and secure all access doors.
i. Restore power to the fan.
Start Up
Turn the fan on. In variable speed units, set the fan to its
lowest speed and inspect for the following:
• Direction of rotation.
• Excessive vibration.
• Unusual noise.
• Bearing noise.
• Improper belt alignment or tension (listen for squeal-
ing).
• Improper motor amperage or voltage.
If a problem is discovered, immediately shut the fan
off. Lock out all electrical power and check for the
cause of the trouble.
See
Troubleshooting
.
Inspection
Inspection of the fan should be conducted at the
fi
rst
30
minute, 8 hour
and
24 hour
intervals of satisfactory opera-
tion. During the inspections, stop the fan and inspect as per
the
Conditions Chart
.
30 Minute Interval
Inspect bolts, setscrews, and motor mounting bolts.
Adjust and tighten as necessary.
8 Hour Interval
Inspect belt alignment and tension. Adjust and tighten as
necessary.
24 Hour Interval
Inspect belt tension, bolts, setscrews, and motor mount-
ing bolts. Adjust and tighten as necessary.
Recommended Torque for Setscrews/Bolts (IN/LB.)
Setscrews
Hold Down Bolts
Size
Key Hex
Across Flats
Recommended Torque
Inch-lbs.
Min.
Max.
Size
Wrench Torque
(inch-lbs)
No.10
3/32”
28
33
3/8”-16
240
1/4”
1/8”
66
80
1/2”-13
600
5/16”
5/32”
126
156
5/8”-11
1200
3/8”
3/16”
228
275
3/4”-10
2100
7/16”
7/32”
348
384
7/8”- 9
2040
1/2”
1/4”
504
600
1”- 8
3000
5/8”
5/16”
1104
1200
1-1/8” - 7
4200
3/4”
3/8”
1440
1800
1-1/4” - 7
6000
3
6
Conditions Chart
RPM
Temperature
Fan Status
Greasing Interval
100
Up to 120
˚
F
Clean
6 to 12 months
500
Up to 150
˚
F
Clean
2 to 6 months
1000
Up to 210
˚
F
Clean
2 weeks to 2 months
1500 Over
210
˚
F
Clean
Weekly
Any Speed
Up to 150
˚
F
Dirty
1 week to 1 month
Any Speed
Over 150
˚
F
Dirty
Daily to 2 weeks
Any Speed
Any Temperature
Very Dirty
Daily to 2 weeks
Any Speed
Any Temperature
Extreme
Conditions
Daily to 2 weeks
Current Switch Set-UP
General Notes:
1. The current sensor is preset at factory.
2. The sensor is designed to shut down the broiler in the
event that the motor current drops below normal. This
will re
fl
ect a problem such as a broken belt.
3. Current sensor shall be enclosed in a (UL Listed for
Outdoor Use) conduit box. Wire shall be ran through
(UL Listed for Outdoor Use) conduit and connectors.
Notes for Current Sensor:
1. Typical operation: Line voltage applied continuously.
After seven seconds of fault, relay trips. If current is
below set point, red LED will light. Current window is
adjustable between 1-10 amps. Adjustments are inde-
pendent.
2. Typical setup: Adjust undercurrent pot to minimum,
clockwise is maximum. Apply current. Once current has
stabalized, adjust undercurrent pot by turning up until red
LED lights. Then turn down within seven seconds until red
light turns off. If a light remains on for more than ten sec-
onds, disconnect supply voltage to reset. Fault window var-
ies by how far the pots are adjusted. Now if a fault occurs
for greater than seven seconds, the relay will trip until sup-
ply voltage is removed.
Maintenance
Establish a schedule for inspecting all parts of the fan.
The frequency of inspection depends on the operating con-
ditions and location of the fan.
Inspect fans exhausting corrosive or contaminated air
within the
fi
rst month of operation. Fans exhausting contam-
inated air (airborne abrasives) should be inspected every
three months.
Regular inspections are recommended for fans exhaust-
ing non-contaminated air.
It is recommended the following inspection be conducted
twice per year.
• Inspect bolts and setscrews for tightness. Tighten as
necessary. Worn setscrews should be replaced immedi-
ately.
• Inspect belt wear and alignment. Replace worn belts
with new belts and adjust alignment as needed. See
Belt and Pulley Installation
, page 3.
• Bearings should be inspected as recommended in the
Conditions Chart
.
• Inspect springs and rubber isolators for deterioration
and replace as needed.
• Inspect for cleanliness. Clean exterior surfaces only.
Removing dust and grease on motor housing assures
proper motor cooling. Removing dirt from the wheel and
housing prevent imbalance and damage.
Lubricants
Loren Cook Company uses petroleum lubricant in a lithium
base. Other types of grease should not be used unless the
bearings and lines have been
fl
ushed clean. If another type
of grease is used, it should be a lithium-based grease con-
forming to NLGI grade 2 consistency.
A NLGI grade 2 grease is a light viscosity, low-torque,
rust-inhibiting lubricant that is water resistant. Its tempera-
ture range is from -30
°
F to +200
°
F and capable of intermit-
tent highs of +250
°
F.
Motor Bearings
Motor bearings are pre-lubricated and sealed. Under nor-
mal conditions they will not require further maintenance for
a period of ten years. However, it is advisable to have your
maintenance department remove and disassemble the
motor, and lubricate the bearings after three years of opera-
tion in excessive heat and or in a contaminated airstream
consisting of airborne abrasives.
Fan Bearings
Greasable fan bearings are lubricated through a grease
fi
tting on the bearing and should be lubricated by the sched-
ule,
Conditions Chart
.
For best results, lubricate the bearing while the fan is in
operation. Pump grease in slowly until a slight bead forms
around the bearing seals. Excessive grease can burst seals
thus reducing bearing life.
In the event the bearing cannot be seen, use no more
than three injections with a hand-operated grease gun.
Motor Services
Should the motor prove defective within a one-year
period, contact your local Loren Cook representative or
your nearest authorized electric motor service representa-
tive.
Figure 5
Figure 5