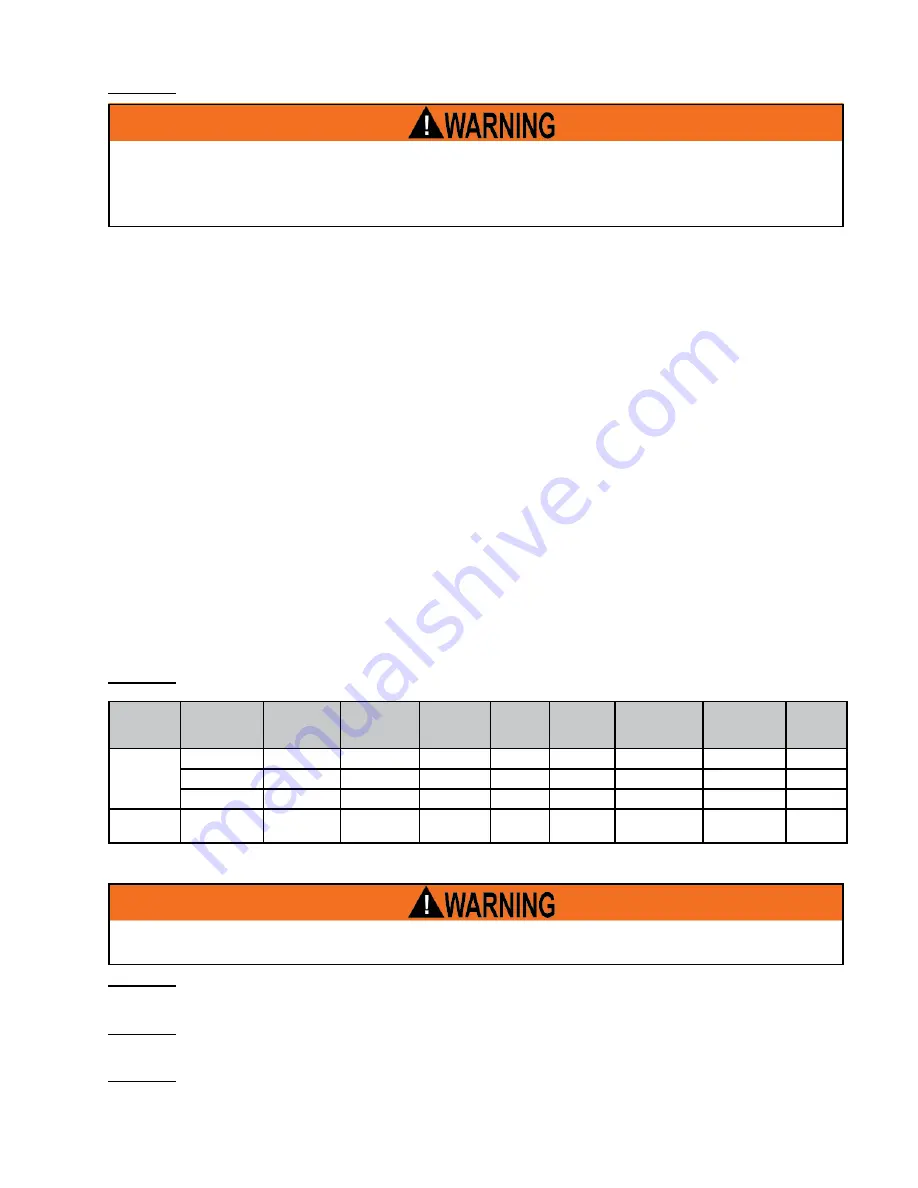
W415-1112 / 06.12.12
32
STEp #18
Connecting fuel to the oil module burner:
○ Storage tank: construction, location, size, inlet/vent sizing, in line filters, shut off's and safety valves are
dictated by the authority having jurisdiction and standards set by CSa b139-09 and nfPa31 (note: mini-
mum distance between the oil storage tank and the solid fuel furnace is 5 ft. 1.52 m), b365-01, section
7.2.5).
○ Plumbing:
○ Piping between the storage tank and the oil burner shall consist of 3/8" or 1/2" pipe (pipe specifica-
tions as per local authority and CSa 139-09).
○ Joins in piping should be kept to absolute minimum,
○ flare fittings are permissible, CauTion: ComPreSSion fiTTinGS SHall noT be uSed.
○ for pipe thread fittings the use of pipe dope is required, CauTion: Teflon TaP SHall noT be
uSed.
○ Choosing 3/8" or 1/2" diameter pipe, single line (gravity feed) or two line (lift system).
○ Pipe sizing and type of plumbing system is dependant upon distance between the storage tank,
burner and relative elevation between the storage tank and the burner.
○ Single line systems are typical of gravity fed burners (storage tank outlet above burner inlet),
where as two line systems are more typical where piping lengths are excessive or suction lines
start below the level of the oil burner.
○ for more detail on which method is more suited for a particular installation, see appropriate burner
manual accompanying the oil burner, in the oil furnace module kit.
○ details on installation and priming of given piping arrangement, also given in specific burner
manual.
ALL INSTALLATION AND MAINTENANCE MUST BE pERFORMED BY A qUALIFIED/LICENSED IN-
STALLER. INCORRECT INSTALLATION, ADjUSTMENT, AND USE OF THE OIL BURNER COULD RE-
SULT IN SEvERE pERSONAL INjURY, DEATH OR SUBSTANTIAL pROpERTY DAMAgE FROM FIRE,
CARBON MONOxIDE pOISONINg, SOOT OR ExpLOSION.
STEp #19
oil burner SeT uP and STarTinG ParameTerS:
STEp #20
STEp #21
○ See SeCTion 6.0 - Plenum and venTinG inSTallaTion.
○ See SeCTion 7.0 - eleCTriCal ConneCTionS and SCHemaTiCS.
STEp #22
○ See SeCTion 8.0 - oPeraTinG inSTruCTionS.
ALL TROUBLE SHOOTINg AND REpAIR MAINTENANCE MUST BE pERFORMED BY A qUALIFIED/
LICENSED SERvICE pERSON.
burner
model
inPuT @
140,000 bTu/
uS Gal
nozzle
(delavan)
PumP
PreSSure
(PSi)
inleT air
damPer
SeTTinG
Co
2
%
STaCk
TemP
(°f)
STaCk
drafT (W.C.)
SS
effiCienCy
(%)
ouTPuT
riello
40f3
64,400
0.4 / 60°a
135
2
-0.02 To -0.04
85%
54,740
77,000
0.5 / 60°a
120
1.8
-0.02 To -0.04
83%
63,910
* 91
,
000
0.65 / 60°a
120
2
12 To 14
500 - 550
-0.02 To -0.04
82%
74,620
beCkeTT
nx
91,000
0.60 / 60°a
120
2
12 To 14
615
-0.02 To -0.04
82%
74,620
* aS equiPPed: To SeT aT zero Smoke SeT uP To TraCe and baCk off 2% Co
2