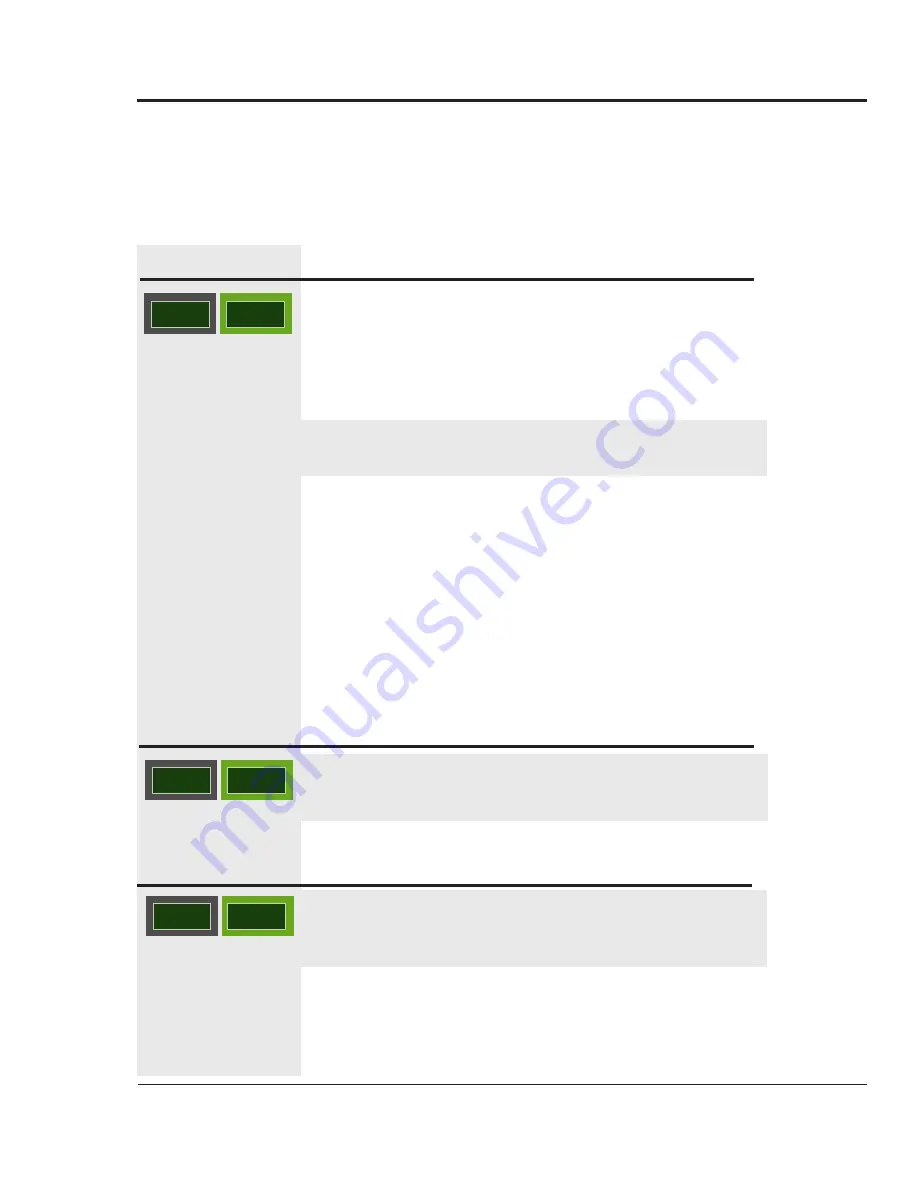
UGH004/0999
microKool Portable Chiller
T
ROUBLESHOOTING
6-5
S
HUT
D
OWN
A
LARMS
The chiller has detected a problem that could lead to equipment
damage or personal injury if it is not corrected.
◆
The Alarm LED lights and the STOP/RUN LED flashes red.
◆
The chiller automatically shuts down.
◆
The control displays a red LED or alarm code indicating the
source of the problem.
Alarm
Actual temperature
of water supplied to
the process is below
the programmed
10° F safety limit.
The thermocouple
in the process
return line failed.
The thermocouple
in the process
supply line failed.
Possible cause
Has the compressor
contactor failed closed?
Has the unloader valve
failed?
Has the freezestat failed?
Is the thermocouple
loose?
Has the thermocouple
failed?
Is the thermocouple
loose?
Has the thermocouple
failed?
Solution
Check phase continuity
through the compressor con-
tactor. If the contactor has
failed, replace it. See
R
EPLACING THE
C
OMPRESSOR
C
ONTACTOR
.
See
C
HECKING THE
U
NLOADER
V
ALVE
.
❒
Check the freezestat setting.
It should be set to cut out at
5° F above the freeze point
of the process fluid solution.
❒
Check for improper freezes-
tat installation. Verify the
freezestat sensor bulb is
well insulated and inserted
into the piping well.
If the freezestat is properly
installed and set, it may have
failed See
R
EPLACING THE
F
REEZESTAT
.
Check for a loose thermocou-
ple or loose wire connections
to the thermocouple.
Check the thermocouple and
replace if necessary.
Check for a loose thermocou-
ple or loose wire connections
to the thermocouple.
Check the thermocouple and
replace if necessary.
SAF
Lo
Err
Pbr
Err
PbS
Summary of Contents for microKool MPA
Page 1: ......
Page 8: ......
Page 42: ......
Page 82: ...PC 1 WIRING DIAGRAM UGH004 0999 PD 2...
Page 84: ...PC 2 WIRING DIAGRAM UGH004 0999 PD 4...
Page 86: ......