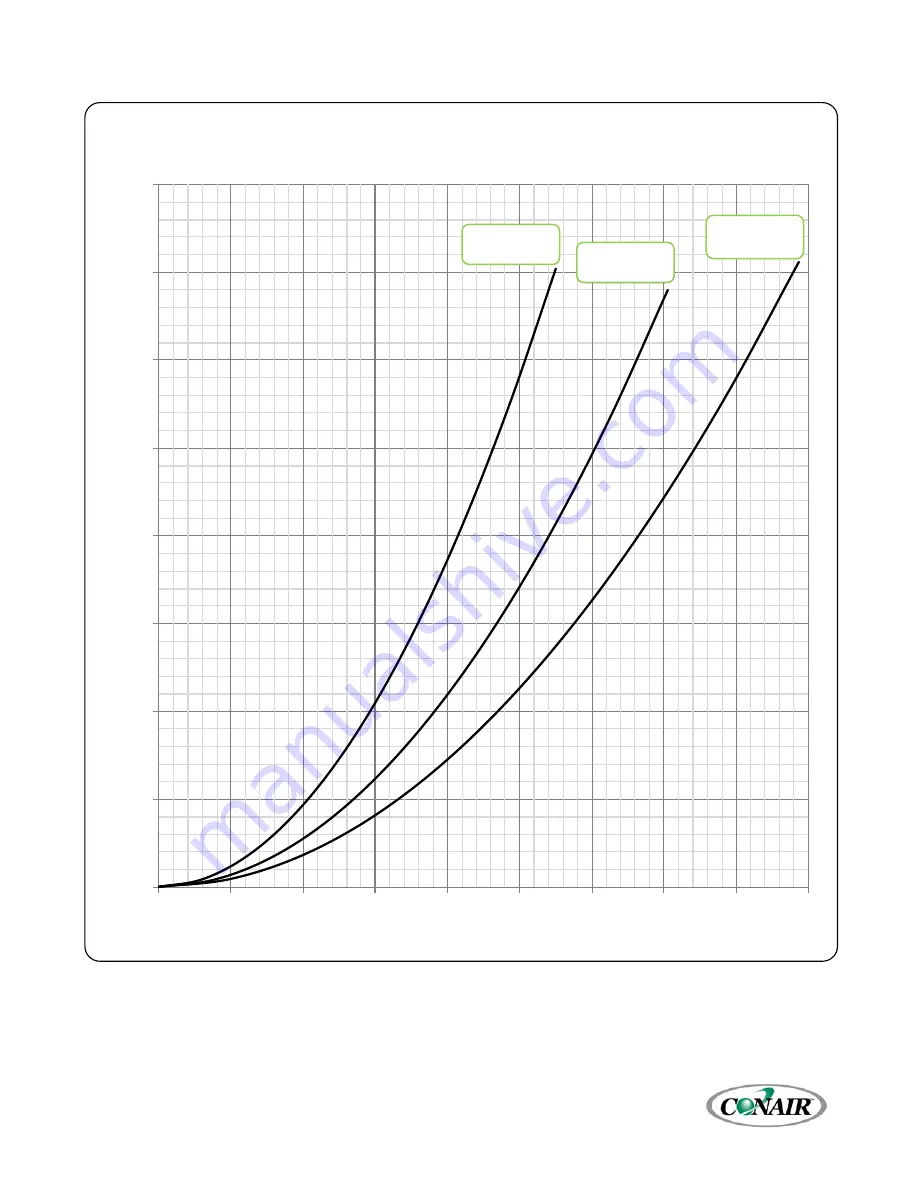
Corporate Office: 724.584.5500
Instant Access 24/7 (Parts and Service): 800.458.1960
Parts and Service
:
814.437.6861
16
Figure 6 – High Flow Chiller Coolant Pressure Drop (30 through 50 ton Single-Circuit Chillers)
0
5
10
15
20
25
30
35
40
0
50
100
150
200
250
300
350
400
450
Pr
ess
ur
e
Lo
ss (
psi
)
Flow (gpm)
High Flow Chiller Coolant Circuit Pressure Drop
(Water at 50°F)
TSEW50S
& TSER50S
TSEW40S
& TSER40S
TSEW30S
& TSER30S
ESEW-030S
ESER-030S
ESEW-040S
ESER-040S
ESEW-050S
ESER-050S