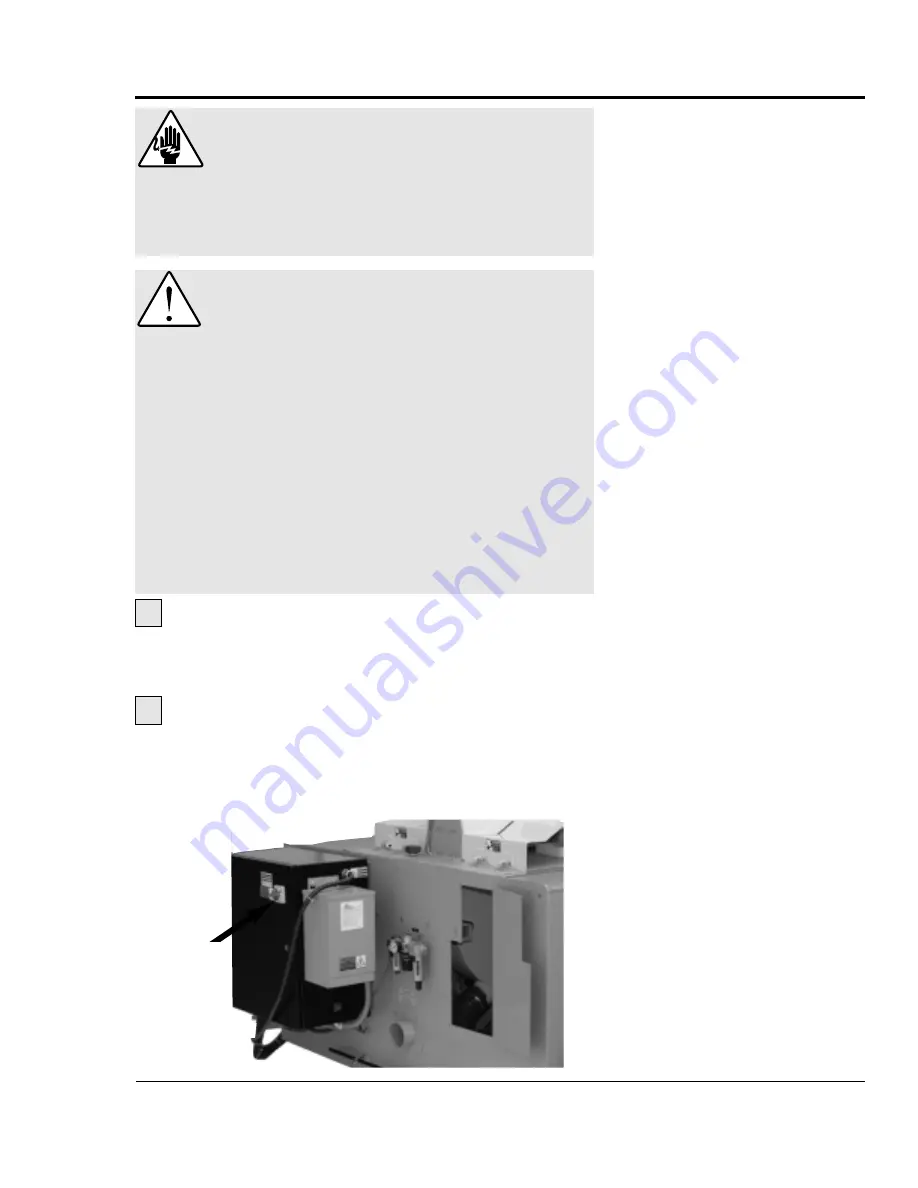
UGE058/0803
CTS Saw
M
AINTENANCE
5-7
Be sure the main power is disconnected and
the saw is locked out
. Always disconnect and
lock out the main power source before opening the unit or
servicing.
Turn the main power disconnect to the off
position
before opening the electrical enclosure on the
back of the saw or the back of the control. This is a safety
device to prevent you from opening the doors if the power
is still on.
C
HECKING
E
LECTRICAL
C
ONNECTIONS
WARNING: Electrical hazard
Before performing any work on this product,
disconnect and lock out electrical power
sources to prevent injury from unexpected ener-
gization or start-up. A lockable device has been
provided to isolate this product from potentially
hazardous electricity.
WARNING: Improper installation, oper-
ation, or servicing may result in
equipment damage or personal injury.
This equipment should only be installed, adjust-
ed, and serviced by qualified technical person-
nel who are familiar with the construction, oper-
ation, and potential hazards of this type of
machine.
All wiring, disconnects, and fuses should be
installed by qualified electrical technicians in
accordance with electrical codes in your region.
Always maintain a safe ground. Do not operate
the equipment at power levels other than what
is specified on the machine serial tag and data
plate.
1
2
Main power
safety
disconnect
continued on the next page