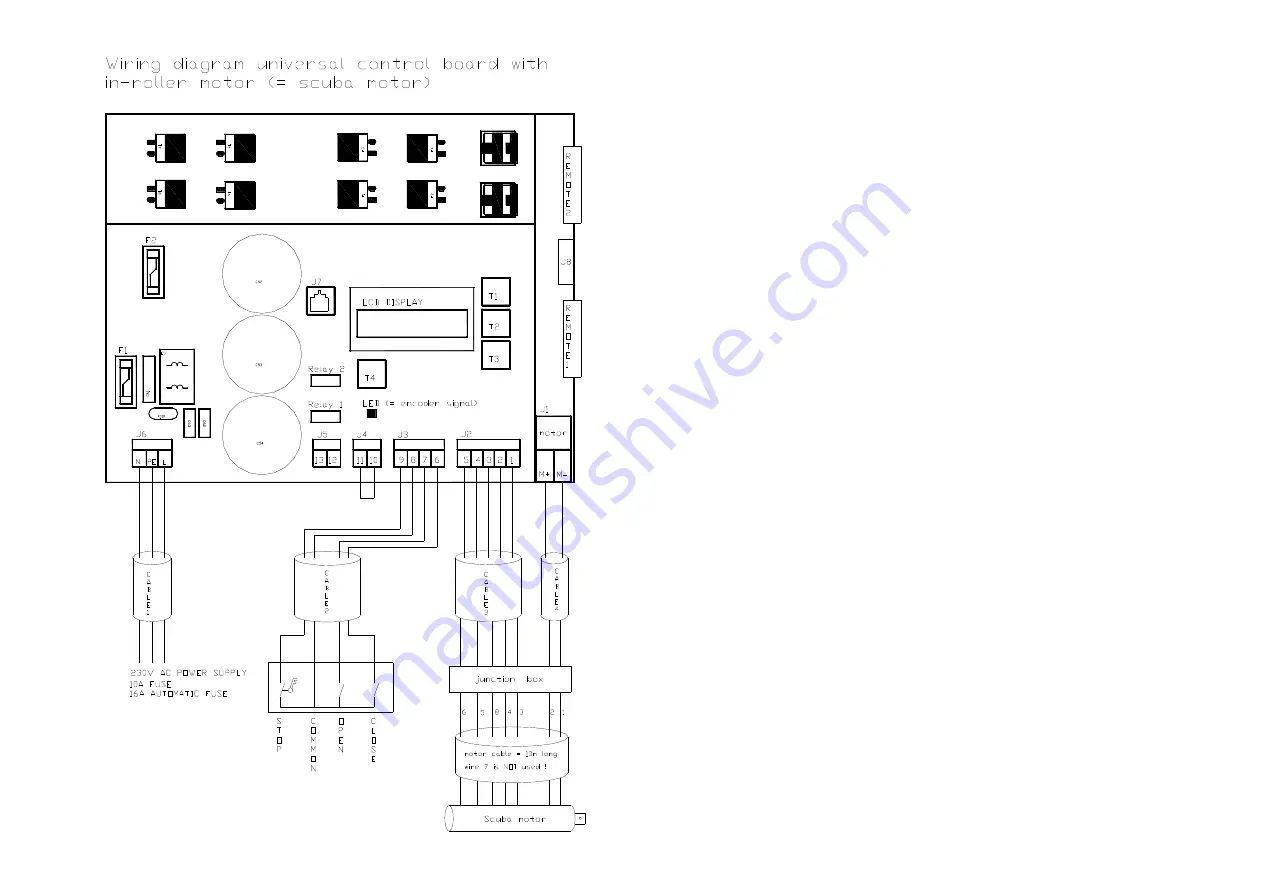
VII.3 : Wiring diagram
Attention:
•
Use shielded cable with
flexible wires
•
Motor cable = 10m long
•
Use the connection box to
extend the cable
•
Test the motor before filling
up the connection box with
resin
•
The resin makes the
connection waterproof
•
(Replace the bridge
between 10-11 by the water
level contact)
Summary of Contents for Rollo Cover
Page 1: ...CompassPools Rollo Cover Installation Manual ...
Page 6: ...II 1 Exploded view of the different parts of the mechanism ...
Page 22: ...III 1 Installation sequence Smooth the pool wall Inject enough silicone type INNOTEC ...
Page 26: ...IV 1 Technical drawing of the SS frame Earth connection Regulating bracket ...
Page 54: ...VII 1 Electrical preparations VII 1 Electrical preparations Motor cable is always 10m long ...