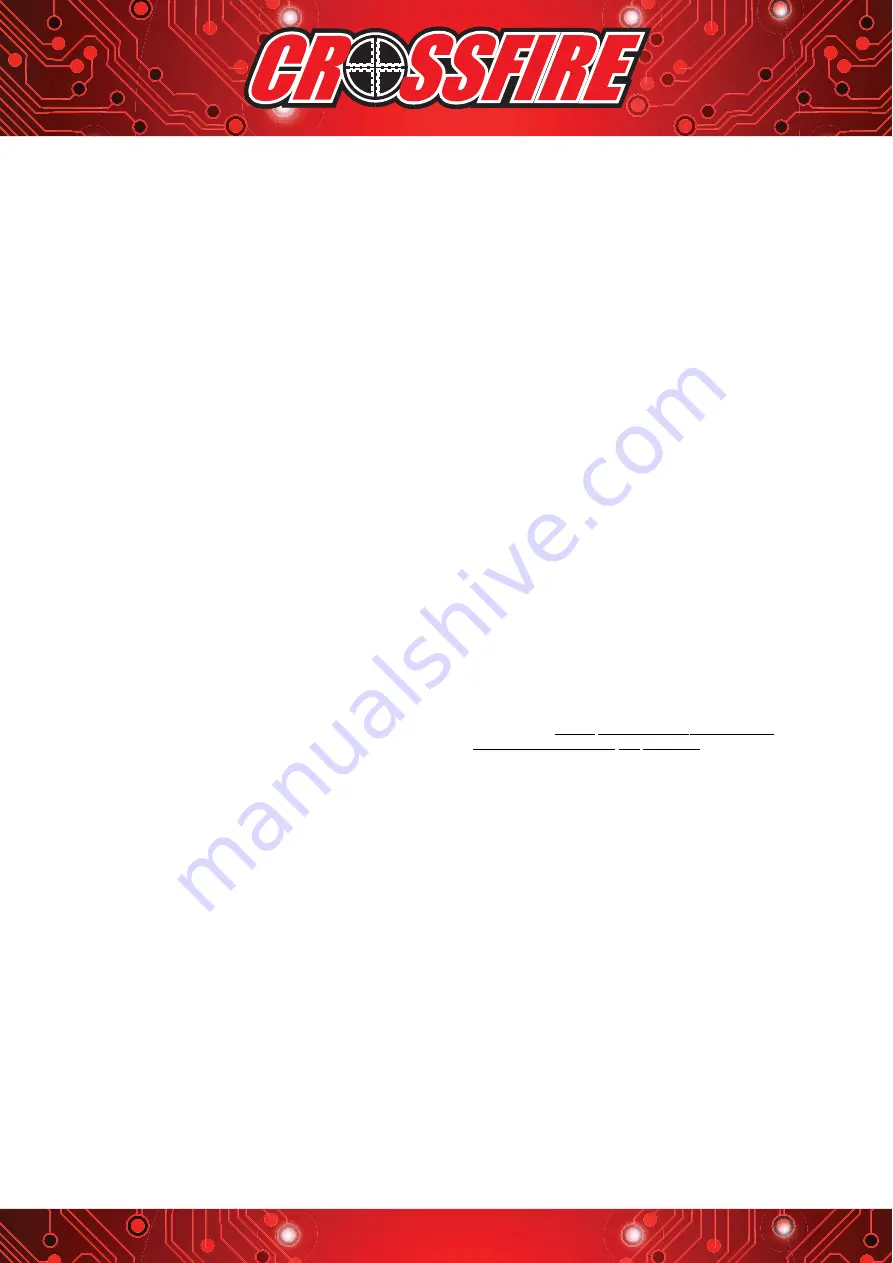
1
CROSSFIRE
®
LIMITED WARRANTY
Effective April 14, 2018
(This limited warranty supercedes all prior warranties and is exclusive with no other warranties or
garuntees implied.)
Warranty Claim
This is a parts and labour warra
nty. Warranty claim
options will be decided at the sole discrection of
Crossfire Welders, which exclusively include (1) repair; or
(2) replacement; or, if approved (3) cost of repair at an
approved Crossfire repair center; or (4) credit (less
depreciation).
Do not return your unit
to the retail or
distribution area where it was purchased
. Retain your
receipt in case a warranty claim is needed. No warranty
will be provided without the
original receipt from retailer.
To make a warranty claim, please contact
[email protected]. No Crossfire warranty service
can begin without a service file number including – Model
# - Serial Number – Purchase Date.
This warranty applies to the original purchaser and is
subject to the terms and conditions listed below. This
Limited Warranty is for new equipment sold after the
above date, providing coverage for defects in
material and workmanship at the time it is shipped
from the factory.
Limited to the warranty periods below, Crossfire
Equipment or an approved Crossfire Repair Centre
will repair or replace the item under warranty that
fails due to defects in material and workmanship.
Crossfire must be notified within 30 days of the
failure, so as to provide instructions on how to
proceed with the repair of you welder and warranty
claim processing. Warranty period begins at the time
the welder is purchased from Crossfire
, or 1 year
after delivery to a distrbutor, whichever comes first
.
Keep your receipt as proof of purchase.
1. 3 Years - Parts
&
Labour
Crossfire Welders and Plasma Cutters including -
transformer, reactor, rectifiier, solenoid valve, PC
Board, switches, controls, gas vavle, drive motor,
drive system (drive roll excluded), and any other part
the requires the removal of sheet metal.
2. 1 Year - Parts & Labour
CG1-Dart Track Cutter
(excluding tracks)
Welding
po
sitioners
,t
urning
r
ollers
, Auto
darkening lens, PAPR blower & battery
,
Rheostat
, Water Cooling Systems.
3. 90 Days - Parts & Labour
Parts for Crossfire MIG guns,
TIG
Torches,
Plasma
Torches,
Spool Guns,
Regulators & Gauges,
welding carts, and welding cabinets. This warranty
covers the absense of defective parts or those
parts as listed under "Warranty Exclusions".
4. Engine Warranty
The engine on this unit is warranted seperately by
the engine manufacturer. Please see the engine
manual.
5. Warranty Exclusions
This limited warranty shall not apply to:
consumables such as; contact tips, nozzles, liners,
drive rollers, plasma cutting torch tips and
electrodes, welding gloves, auto-darkening helmet
outside/inside lens, weld cables, ground clamps
,
and any crossfire products that fail due to normal
wear.
Items furn
ished
by
Crossfire Welders
, but
manufactured by others, such as accessories and
engines.
6. Voiding Warranty
The limited warranty is void if the Crossfire product has
been repaired, changed, or modified by anyone other then
Crossfire Welders
or an Authorized Crossfire Repair
Centre. Equipment that has been improperly installed,
misued based on standard operating procedures and
industry standards,
or has not been reasonably
maint
ained
.
ANY AND ALL WARRANTY CLAIM TRANSPORTATION
,
FREIGHT COST
,
AND RISKS WILL BE AT THE SOLE
RESPONSIBILITY OF THE OWNER.
TO THE EXTENT PERMITTED BY LAW, THIS LIMITED
WARRANTY AND THE REMEDIES HEREIN ARE THE SOLE
AND EXCLUSIVE REMEDIES OF THE PURCHASER IN
RESPECT TO
CROSSFIRE
PRODUCTS. IN NO EVENT SH
ALL
CROSSFIRE WELDERS
BE LIABLE FOR ALL INDIRECT,
DIRECT, SPECIAL, INCEDENTAL AND CONSEQUENTIAL
DAMAGE, LOSS, EXPENSES OR LOSS OF PROFIT. ANY
WARRANTY NOT PROVIDED HEREIN AND ANY IMPLIED
WARRANTY GAURANTY OR REPRESENTATION ARE
EXCLUDED AND DISCLAIMED BY
CROSSFIRE WELDERS.
HAVE QUESTIONS?
Toll-Free: 1-800-757-4445
Email: [email protected]
Rev
2
- 0
9
/
09
/1
9
Summary of Contents for ALPHA TIG 252 - DP
Page 6: ......
Page 30: ...NOTES...