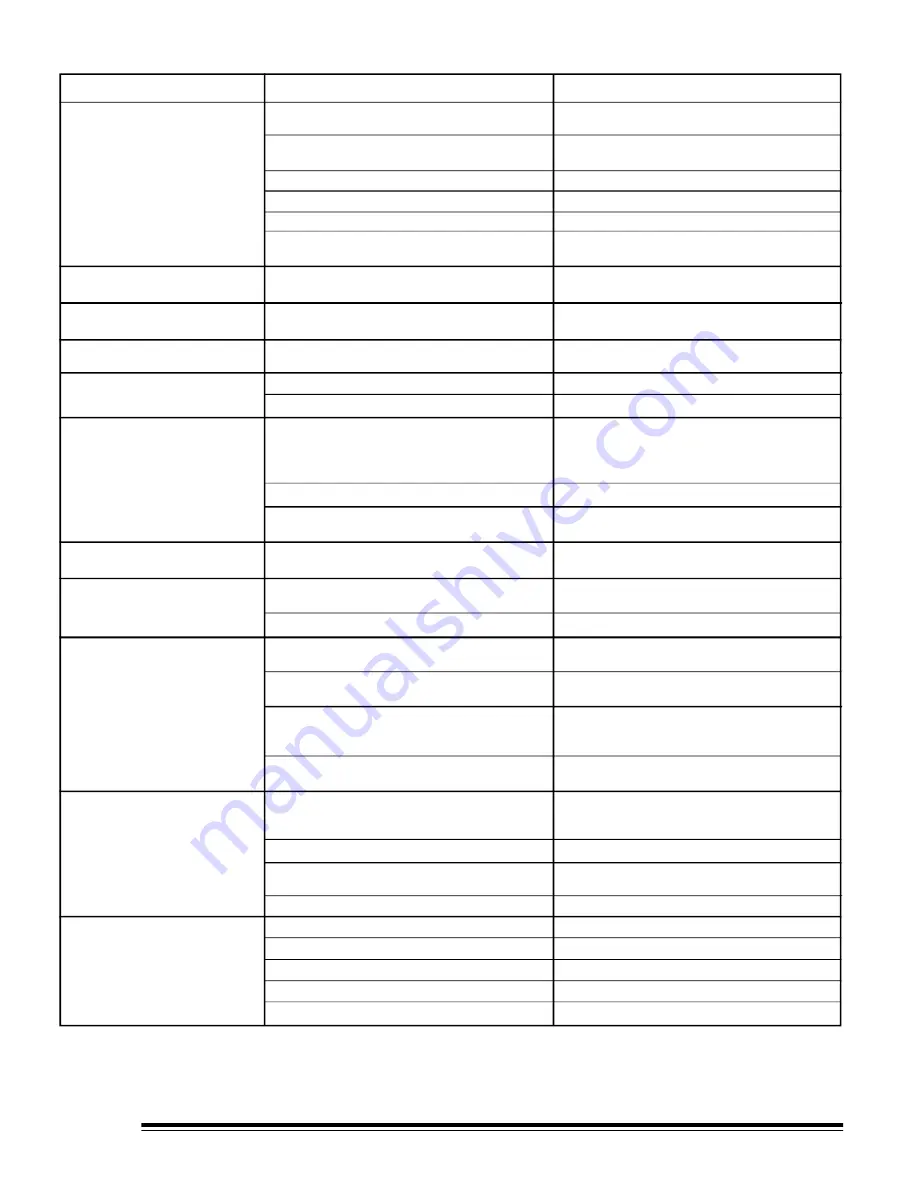
14
Lack of high frequency at tungsten
electrode, difficulty in starting and
arc.
5-2 TROUBLESHOOTING.
Tungsten electrode oxidizing and
not remaining bright after conclusion
of weld.
Unit provides only maximum or
minimum weld output.
Weld output always above or
always below set value.
Electronic board PC1.
Erratic weld output
No control of weld output.
No weld output, fan runs.
No weld output, unit completely
inoperative
TROUBLE
REMEDY
CAUSE
Gas shutting off too quickly after end of weld.
Loose gas fittings on regulator or gas line. This
will siphon oxygen into the weld zone.
Insuficient gas flow.
Drafts blowing gas shield away from tungten.
Contaminated tungten.
High frequency switch in OFF position.
Increase time settings of post-flow time control (See
figure 4-11).
Check and tighten all gas fittings.
Increase gas flow setting.
Shield weld zone from drafts.
Prepare tungsten as instructed in section 8.2.
Place HIGH FRECUENCY in START or CONTINUOUS
position.
Consult your dealer or Service Center to review unit.
Electronic board PC1.
Consult your dealer or Service Center to review unit.
Electronic board PC1.
Consult your dealer or Service Center to review unit.
AC Balance control R3.
Circuit Board PC1.
Amperage control switch S5 position.
Amperage adjustment control R1.
Check and replace R3.
Place S5 in PANEL position, if no remote control is
begin used. Place S5 in REMOTE position and be sure
remote control Is connected to REMOTE 14 receptacle
RC2 (See Section 3-5 & Figure 4-6).
Check And Replace R3.
Electronic board PC1.
Consult your dealer or Service Center to review unit.
No AC BALANCE control
No HIGH FREQUENCY, No gas flow,
and no spot time (If applicable)
Circuit Breaker CB1.
Check and reset CB1 if necessary.
Improperly prepared tugsten.
Wandering Arc - Poor Control Of
Direction Of Arc
Use of tungsten considerably larger
than recommended.
Prepare tungsten as instructed in section 8-2.
Use proper size tungsten (See Table 8-1).
Use of tungsten larger than recomended for
welding amperage.
Consult your dealer or Service Center to review unit.
Disipation of high frequency from SMAW electrode
holder lead.
Be sure to disconnect SMAW electrode cable from
weld output terminal when GTAW welding
Improper spark gap.
Weld cable leakage.
Check spark gaps and readjust if necessary (See
section 5.5)
Check cables and torch for cracked or deteriorated
insulation or bad connections. Repair or replace
necessary parts.
Consult your dealer or Service Center to review unit.
Output contactor switch S3 position
Remote control device.
Thermostat TP1 open (Thermal shutdown) or not
working.
Electronic board PC1
Place S3 in ON position if no remote control is
used.Place S3 in REMOTE position and be sure remote
control is connected to receptacle RC2.
Check and repair or replace remote control device.
Allow unit to cool for approximately 15 minutes with
fan on.
Consult your dealer or Service Center to review unit.
Line disconnet switch in the OFF position.
Line fuse (s) open.
Improper electrical input connections.
Input voltage jumpers links not in proper positions.
Power switch.
Place line disconnect switch in the ON position.
Check and replace line fuse(s).
See section 3-8 for proper input connections.
See section 3-8 for proper jumper link position.
Check and replace S1 if necessary.
Summary of Contents for ALPHA TIG 252 - DP
Page 6: ......
Page 30: ...NOTES...