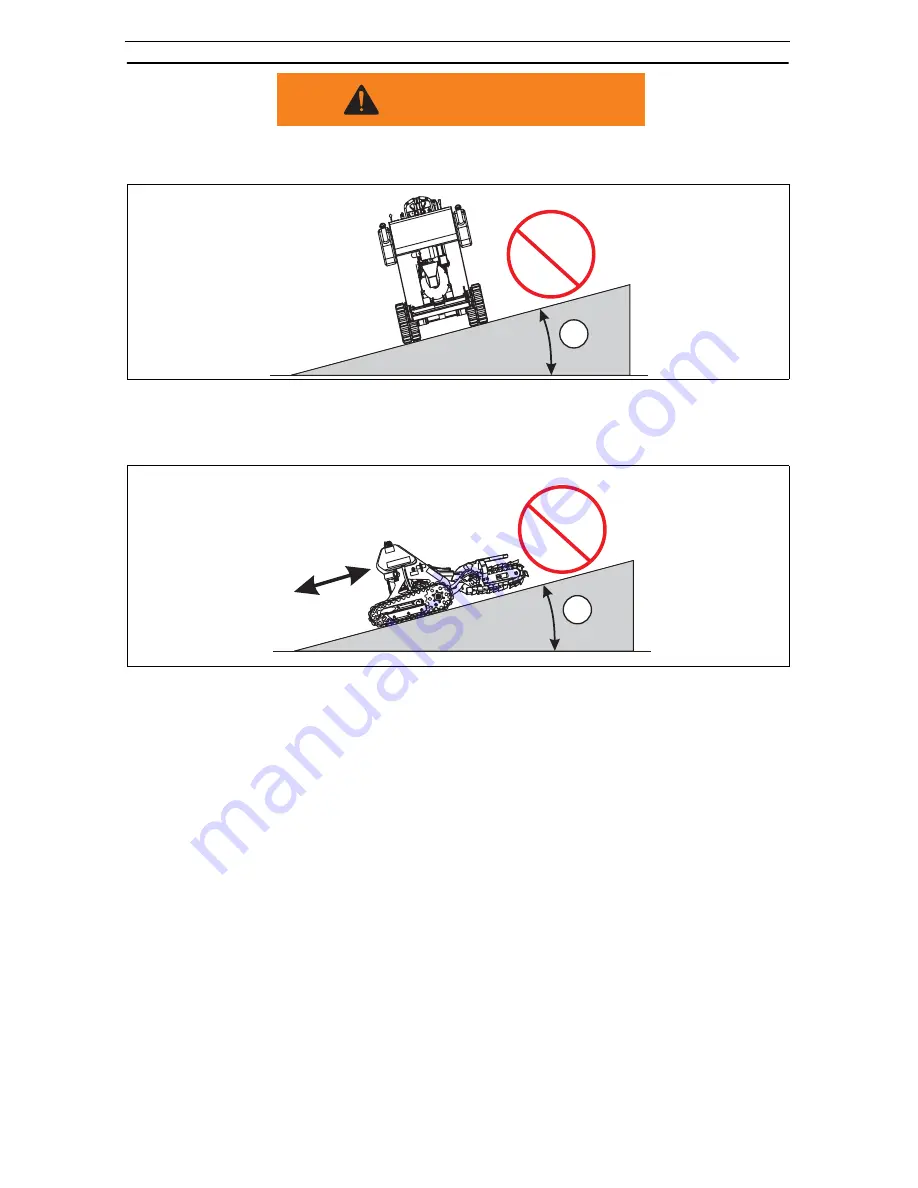
3-14
Pre-Start Inspection and Operation
• Do not travel up or across a slope steeper than 15°. See
Figure 3–15
.
• Keep boom as low as possible when traveling on slopes or rough terrain.
Figure 3–15 Slide Slope Travel
• Keep the heavy end of the machine towards the uphill direction when traveling up
or down a slope. See
Figure 3–16
.
Figure 3–16 Uphill/Downhill Travel
WARNING
P
15
°
>15
°
1
6
16
2437
P
15
°
>15
°
2438
Summary of Contents for BOXER 118
Page 3: ......
Page 4: ......
Page 10: ...vi Mertz Manufacturing LLC P O Box 150 Ponca City OK 74602 Affix Stamp Here...
Page 12: ...viii...
Page 22: ...1 8 Safety Precautions...
Page 48: ...3 20 Pre Start Inspection and Operation...
Page 84: ...5 4 Troubleshooting...