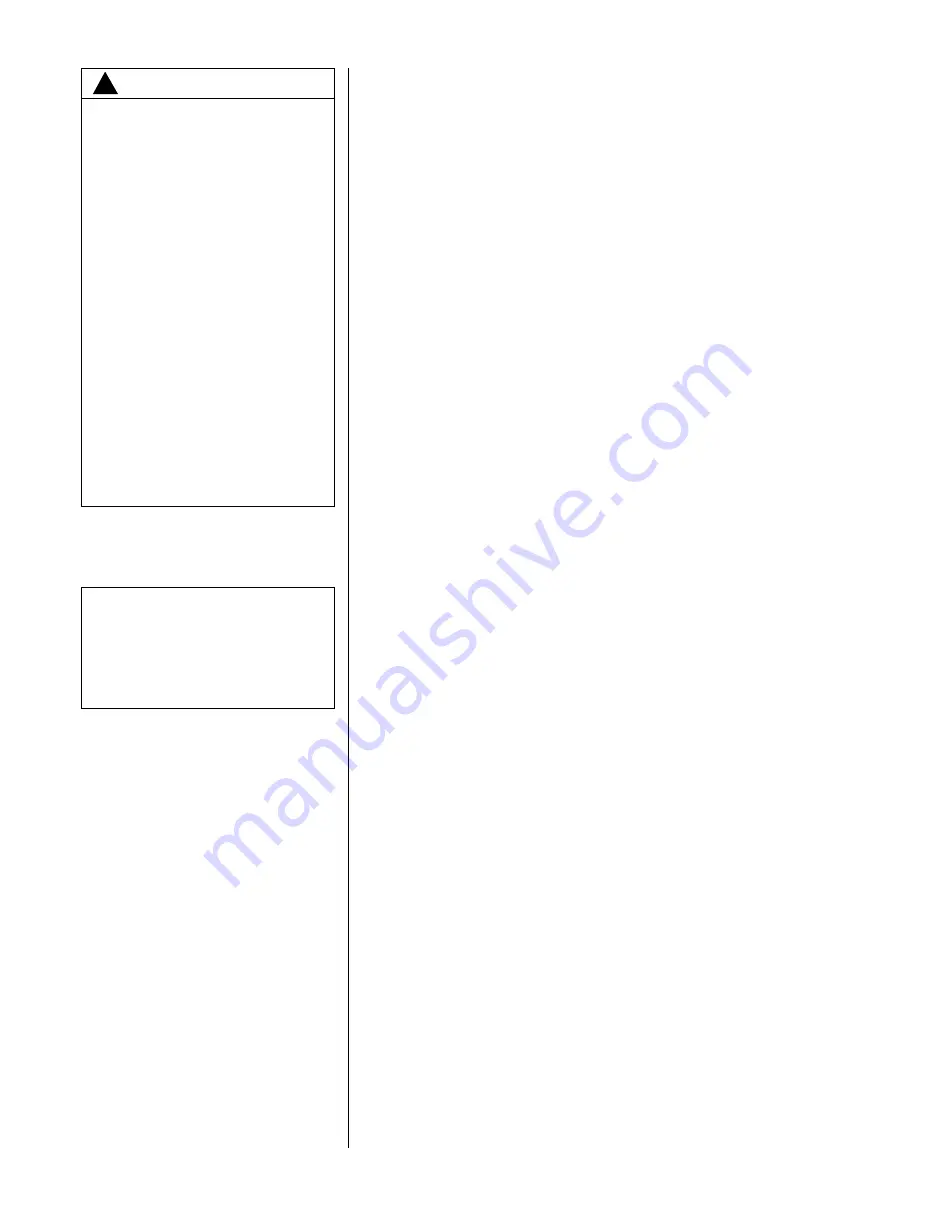
5
2.0 GENERAL INFORMATION
The (-)PRL-series of heat pump are designed to operate using the
Comfort Control
2
System™
or traditional 24VAC controls. These units are equipped with the
Comfort
Control
2
System™
. To take full advantage of the
Comfort Control
2
System™
, the
preferred method of installation is using the
Comfort Control
2
. Your installation must
have these components to use the
Comfort Control
2
System™
:
• (-)PRL heat pump with the
Comfort Control
2
System™
• Air handler or furnace equipped with the
Comfort Control
2
System™
•
Comfort Control
2
thermostat
If your installation does not meet the above requirements, you must use traditional
24VAC controls.
This installation instruction manual contains complete instructions for installation
and setup with using the
Comfort Control
2
or conventional 24VAC controls. Please
refer to the Engineering Specification Sheets for complete performance data, ther-
mostat, and accessory listings.
The information contained in this manual has been prepared to assist in the proper
installation, operation and maintenance of the air conditioning system. Improper
installation, or installation not made in accordance with these instructions, can
result in unsatisfactory operation and/or dangerous conditions, and can cause the
related warranty not to apply.
Read this manual and any instructions packaged with separate equipment required
to make up the system prior to installation. Retain this manual for future reference.
To achieve optimum efficiency and capacity, the indoor cooling coils listed in the
condensing unit specification sheet should be used.
2.1 Checking Product Received
Upon receiving unit, inspect it for any shipping damage. Claims for damage, either
apparent or concealed, should be filed immediately with the shipping company.
Check heat pump model number, electrical characteristics and accessories to
determine if they are correct. Check system components (evaporator coil, condens-
ing unit, evaporator blower, etc.) to make sure they are properly matched.
2.2 Application
Before specifying any heat pump equipment, a survey of the structure and a heat
loss and heat gain calculation must be made. A heat loss calculation involves iden-
tifying all surfaces and openings that lose heat to the surrounding air and quantify-
ing that heat loss. A cooling heat gain calculation makes similar measurements and
determines the amount of heat needed to be removed. A heat gain calculation also
calculates the extra heat load caused by sunlight and by humidity removal. These
factors must be considered before selecting a heat pump system to provide year
round comfort. The Air Conditioning Contractors of America (ACCA) J Manual
method of load calculation is one recognized procedure for determining the heating
and cooling load.
The cooling load calculation determines the heat pump size. There are two capaci-
ties that enable the equipment to provide comfort. The first is sensible capacity.
Sensible heat is the heat energy measured on the dry bulb thermometer.
The second form of heat is called latent or hidden heat. This is heat held in the
humidity in the air. Removing this heat does not affect a thermometer. However,
removing the heat held in the moisture in the air greatly increases comfort. A prop-
erly sized unit removes both forms of heat, producing a comfortable living space. An
oversized system cycles on and off too quickly and does not properly remove
humidity, producing an uncomfortable living space. Select the indoor and outdoor
equipment combination based on the manufacturer's engineering data.
After the proper equipment combination has been selected, satisfying both sensible
and latent requirements, the system must be properly installed. Only then can the
unit provide the comfort the manufacturer built into it.
There are several factors that installers must consider.
•
Outdoor unit location
•
Indoor unit blower speed
•
Proper equipment evacuation •
Supply and return air duct design and sizing
•
Refrigerant charge
•
System air balancing
•
Indoor unit air flow
•
Diffuser and return air grille location and sizing
!
WARNING
THE MANUFACTURER’S WAR-
RANTY DOES NOT COVER ANY
DAMAGE OR DEFECT TO THE
AIR CONDITIONER CAUSED BY
THE ATTACHMENT OR USE OF
ANY COMPONENTS. ACCES-
SORIES OR DEVICES (OTHER
THAN THOSE AUTHORIZED BY
THE MANUFACTURER) INTO,
ONTO OR IN CONJUNCTION
WITH THE AIR CONDITIONER.
YOU SHOULD BE AWARE THAT
THE USE OF UNAUTHORIZED
COMPONENTS, ACCESSORIES
OR DEVICES MAY ADVERSELY
AFFECT
THE
OPERATION
OF THE AIR CONDITIONER AND
MAY ALSO ENDANGER LIFE
AND PROPERTY. THE MANUFAC-
TURER
DISCLAIMS
ANY
RESPONSIBILITY FOR SUCH
LOSS OR INJURY RESULTING
FROM
THE
USE
OF
SUCH
UNAUTHORIZED COMPONENTS,
ACCESSORIES OR DEVICES.
MATCH ALL COMPONENTS:
• OUTDOOR UNIT
• INDOOR COIL/METERING DEVICE
• INDOOR AIR HANDLER/FURNACE
• REFRIGERANT LINES
Summary of Contents for PRL-series
Page 52: ...FIGURE 11 WIRING DIAGRAM FOR 2 3 4 TON 19 0 WIRING DIAGRAMS 52 ...
Page 53: ...FIGURE 12 WIRING DIAGRAM FOR 5 TON 53 ...
Page 54: ...54 ...
Page 55: ...55 ...
Page 56: ...56 CM 1108 ...