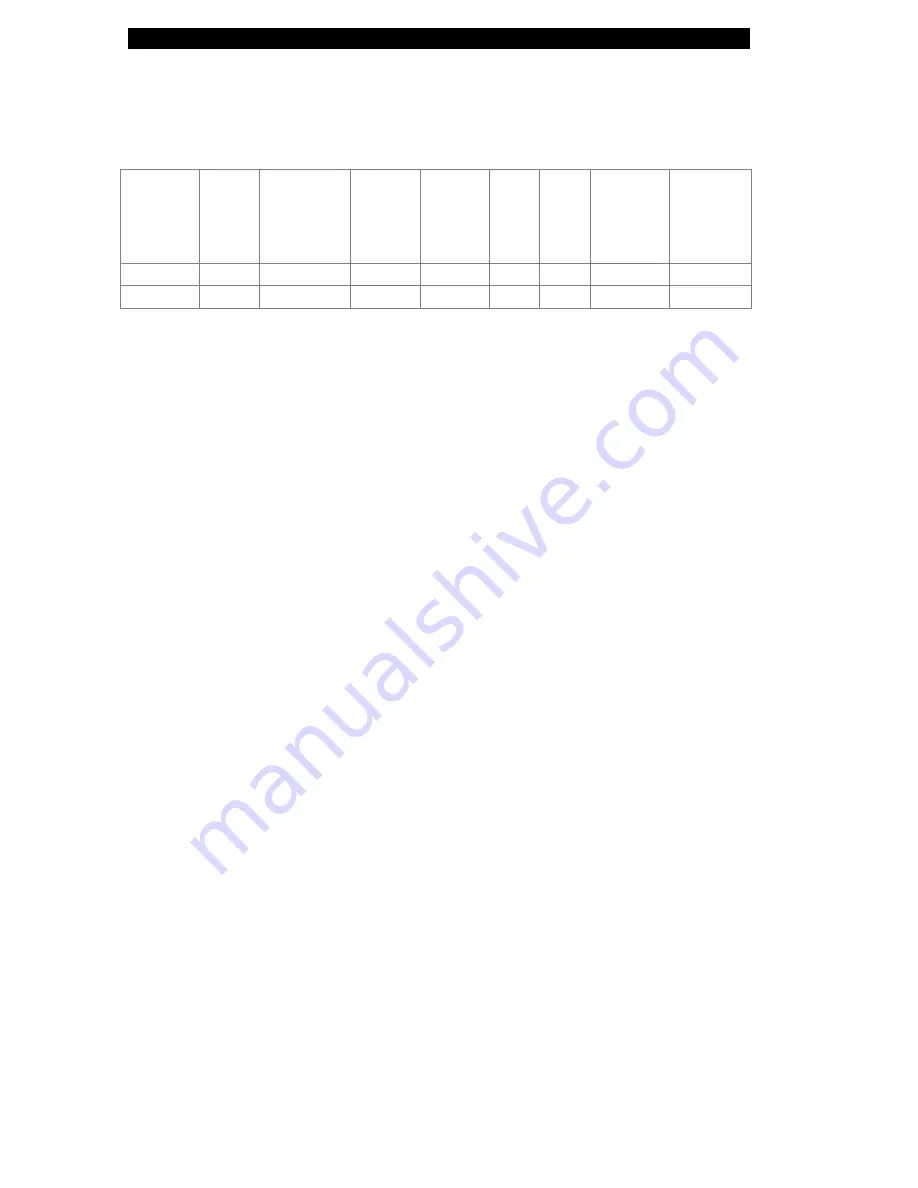
INSTRUCTIONS FOR TECHNICAL PERSONNEL
33
ENERGY CONSUMPTION
Mod.
Tank
capacity
(l)
Water
consumption
per cycle (l)
Tank
heater (W)
booster
heater (W)
Pump
(W)
Total
power
(W)
Max hourly
production
racks with
inlet water
at 55°C
Max hourly
production
racks with
inlet water at
12°C
FC54-E
15
3.5
2000
3000
450
3450
30/20
10
FC54-EA
15
3.5
2000
3000
450
3450
30/20
10
In the event of low water supply temperature, the will be a subsequent
machine output drop.
Summary of Contents for FC54-E
Page 3: ...19 INSTRUCTIONS FOR USE ...
Page 18: ...05 2001 CODICE 900173 ...