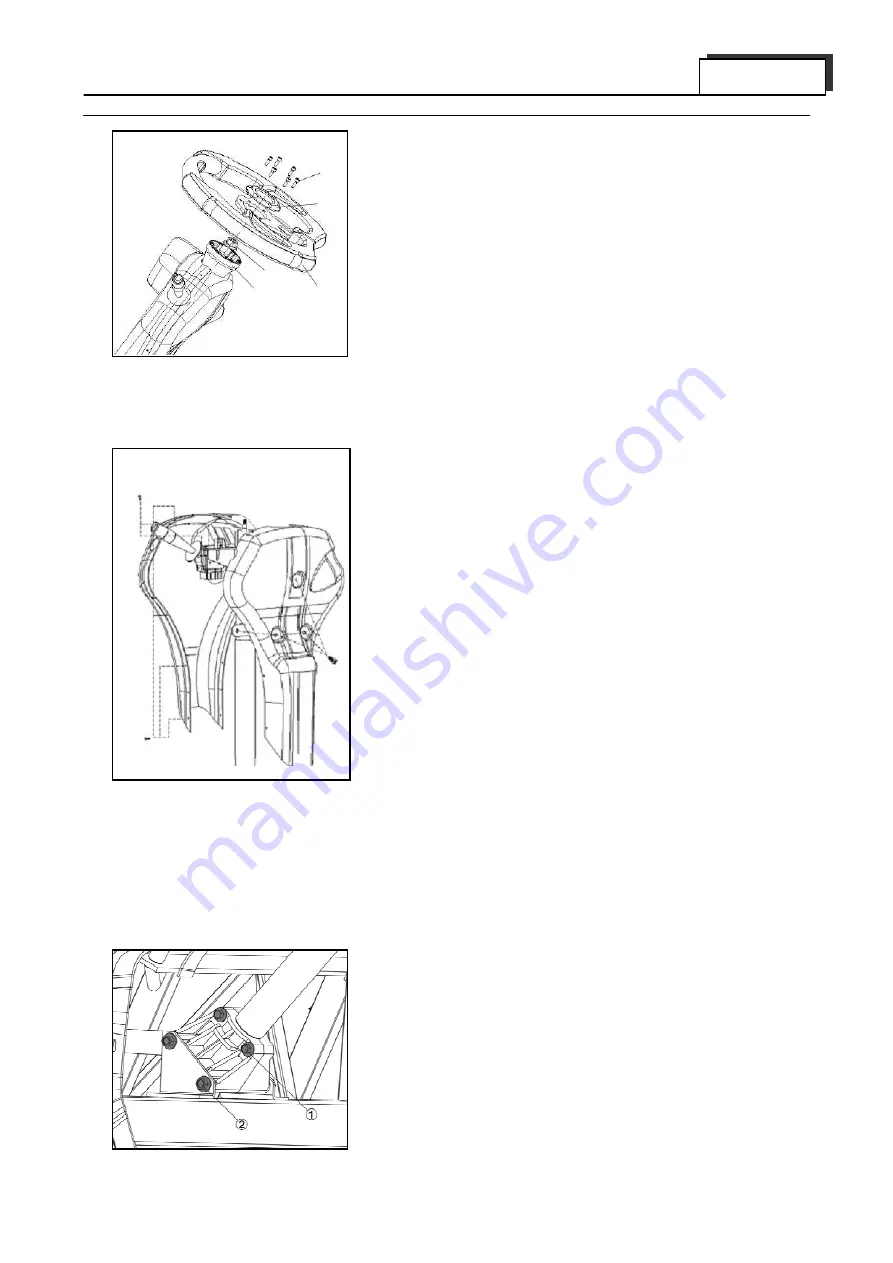
Steering System
8-3
Chapter 8
Removal of the Steering System
1. Park the vehicle on level ground.
3. Put a suitable bracket under the frame and lift
up the front wheels with lifting jack.
Refer to Chapter 1 "Recommendation for Use
of Lifting Jack".
4. Remove:
· Bolts
· cover
②
· Steering wheel
③
5.
Remove:
· Dashboard
Please refer to Chapter 4 "Removal of the
Dashboard".
· Disconnect the connecting line of turn signal
stalk
·Sleeve of turn signal stalk cable
· Bolt
· Turn signal stalk
6. Remove:
· Upper fixing bolt of the block of steering
column
①
Tightening torque
20N·m (14.8 ft·1b)
· Lower fixing nut of the block of steering
column
②
2. Assure that the E-Brake switch is in the middle
possition(Normal).
· Steering covers.
· Main switch and Combination switch.
①
②
③
④
⑤
· Nut
④
· holder,Steering wheel
⑤
①