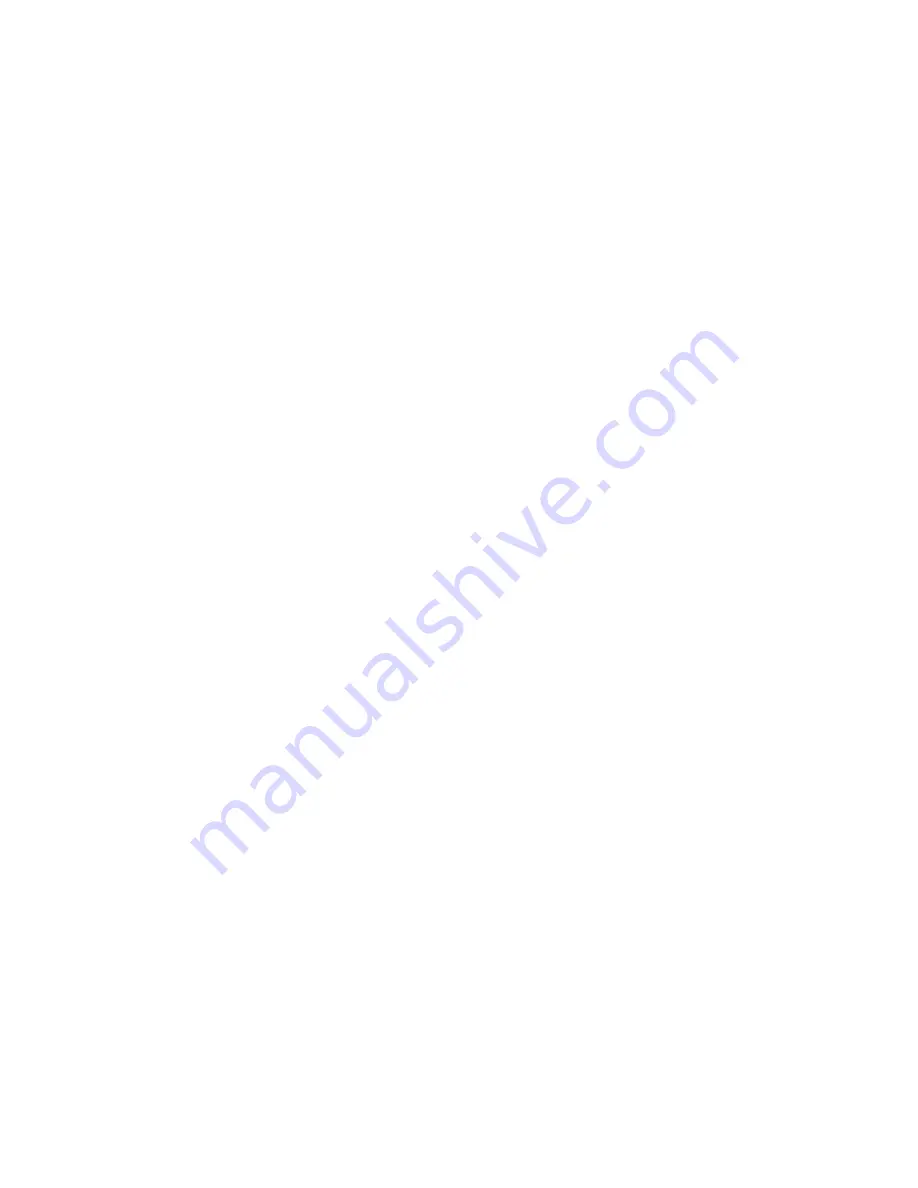
Output:
Pump Speed:
35 to 321 rpm
Torque output, maximum:
1100 oz-in (104 kg-cm)
Tubing compatibility:
Sizes B/T 87 or B/T 91
Flow Range:
Up to 10 GPM (37.85 LPM)
Input:
1750 rpm maximum
1/2 hp (0.37 kW)
293 oz-in minimum
NEMA 56C motor for 77111-50 or
IEC 72 71-14F130 frame for 77111-55
Construction:
Dimensions (L × W × H):
27.63 in × 15.88 in × 15.13 in
701 mm × 403 mm × 384 mm
Weight:
63 lbs (28.5 kg)
Enclosure Rating:
IP65 per IEC 60529
Environment:
Temperature, Operating:
1°C to 40°C (34°F to 104°F)
Temperature, Storage:
–10°C to 65°C (–14°F to 149°F)
Humidity:
(non-condensing)
20% to 80%
Altitude:
Less than 2000 m
Chemical Resistance:
Exposed materials are powder coated
aluminum, CRS, plastic, and vinyl
Compliance
(for CE mark):
EN809 (EU Machine Directive)
5-6
B/T
®
RAPID-LOAD
®
Peristaltic Pumps and Drive Operating Manual
Cole-Parmer
Section 5
Specifications
Models 77111-50
and 77111-55