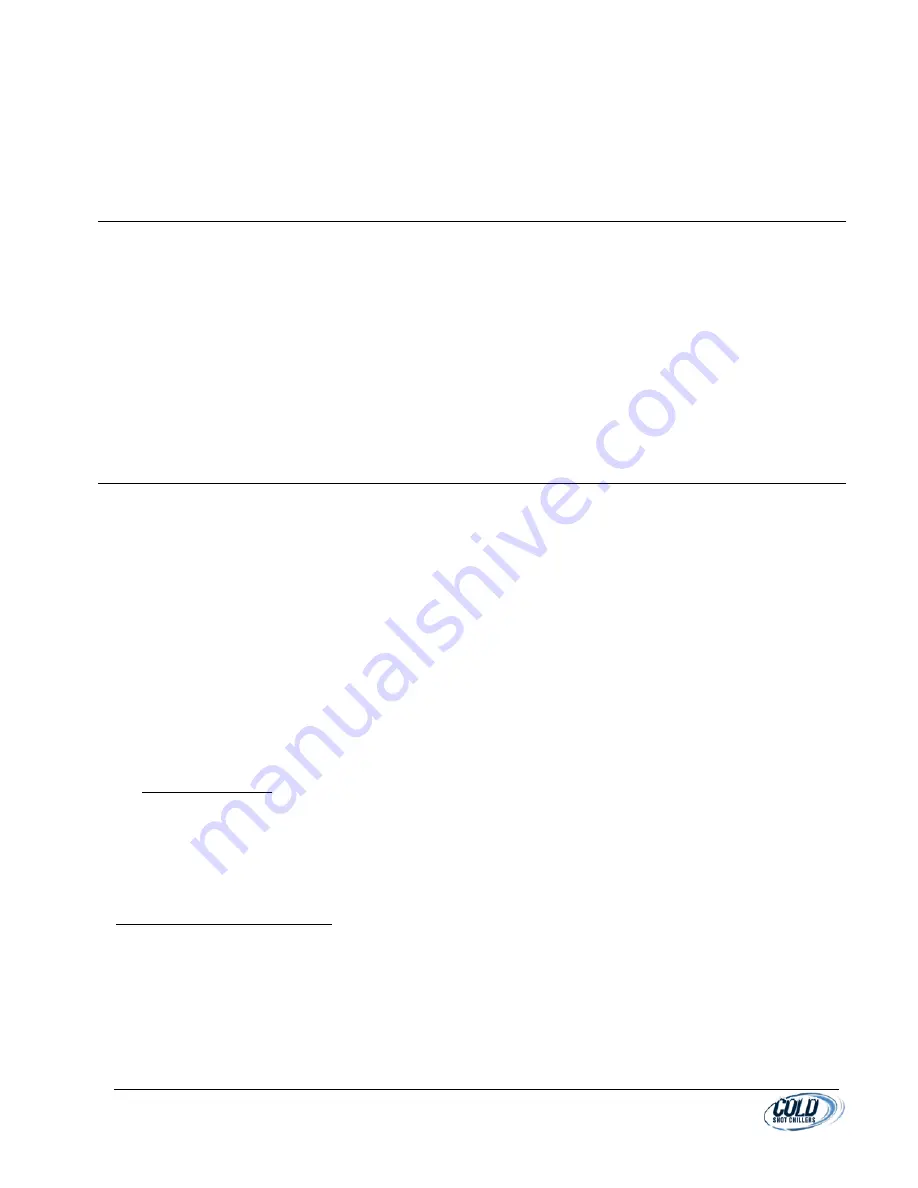
MNL_Standard-NoSpecs_ACWC-18to240-E-_(0713).docx
- 5 -
(6)
Heat-trace cable. Protect any fluid system exposed to freezing ambient conditions.
e)
Systems with the process piping located above the chiller, should be aware of possible fluid returning to
the chiller when the system is turned off. Typically, the chiller inlet/outlet piping is below the tank
water level which will limit draining fluid to tank, however if the process piping is opened, the fluid may
return to the tank and overflow. Recommend isolation valves
D.
SPLIT SYSTEMS (Remote Condenser or Condensing Unit)
1.
Conform to all local codes and standard practices for systems with refrigerant.
2.
Systems with split refrigerant systems are typically shipped without refrigerant, however, are it is charged with
nitrogen to maintain a positive pressure (typically 10-15 psi).
3.
Verify and remove the nitrogen charge. Each marked section should have a positive charge (see tag/decal noted
at connection point).
a)
If no pressure is present, reapply pressure and check for leaks before charging with refrigerant.
4.
Pipe the refrigerant lines of the two units together as required.
5.
Pressure test the system, pull vacuum, and degas. Use proper industry practices with system.
a)
Split systems need to be evacuated prior to charging with refrigerant.
6.
Add refrigerant to the liquid line service port. See the equipment label plate for the type of refrigerant and
typical amount of initial charge or check the specification sheet. Adjust as needed to set the appropriate charge
as noted in Startup section.
E.
ELECTRICAL POWER AND CONNECTIONS
1.
POWER SUPPLY: Field wiring must comply with national and local codes.
a)
Install a branch circuit fused disconnect of adequate size to handle starting current. The disconnect must
be within sight from the unit and readily accessible, in compliance with National Electrical Code (NEC),
Section 440-14.
b)
Verify electrical power on the Cold Shot Chillers label plate with actual voltage.
c)
Connect line power supply to terminal block or as noted in machine; typically, connect power leads to
terminals L1, L2 and L3 on compressor contactor.
d)
Ensure Ground wire is connected appropriately.
e)
208/230V/3Ø systems with high or “stinger” leg, connect this leg to L2 or middle terminal. Failure to do
so will cause early control component malfunction.
(1)
If 208V, verify that the control circuit voltage out of the transformer is the proper amount. If not,
check the transformer for additional tap wires for changing to 208V, when available.
2.
ACCESSORIES/EXTRA EQUIPMENT
a)
Field-installed accessories refer to the accessory literature for installation instructions.
b)
Wiring connections for field-supplied equipment are shown on wiring diagrams.
3.
Verify that the chiller selector switch is in “Off” position before applying power.
4.
ROTATION (3-PHASE) If using a phase sequence tester, electrical phase direction is clockwise.
1
Electrical Notes:
•
Factory wiring is in compliance with NEC. Any field modifications or additions must be in compliance with all applicable codes. Use copper,
copper-clad aluminum for field power supply only.
•
Field power supply wiring must be 75 C minimum.
•
If any of the original wiring furnished must be replaced, it must be replaced with 90 C wire or its equivalent.
•
Compressor thermally protected. Three-phase motors are protected against primary single-phasing condition.
•
60 Hz units have 120 volt control circuit. 50 Hz units have 230 volt control circuit. A separate source of supply at the correct voltage
•
Must be field supplied through a fused disconnect device with a maximum rating of 15 A to TB2 connections L1 (Hot Side) and L2 (Neutral).
•
Open control circuit disconnect switch for servicing only. Disconnect must remain closed for crankcase heater to operate.
•
Transformers must be fused and grounded per applicable codes.