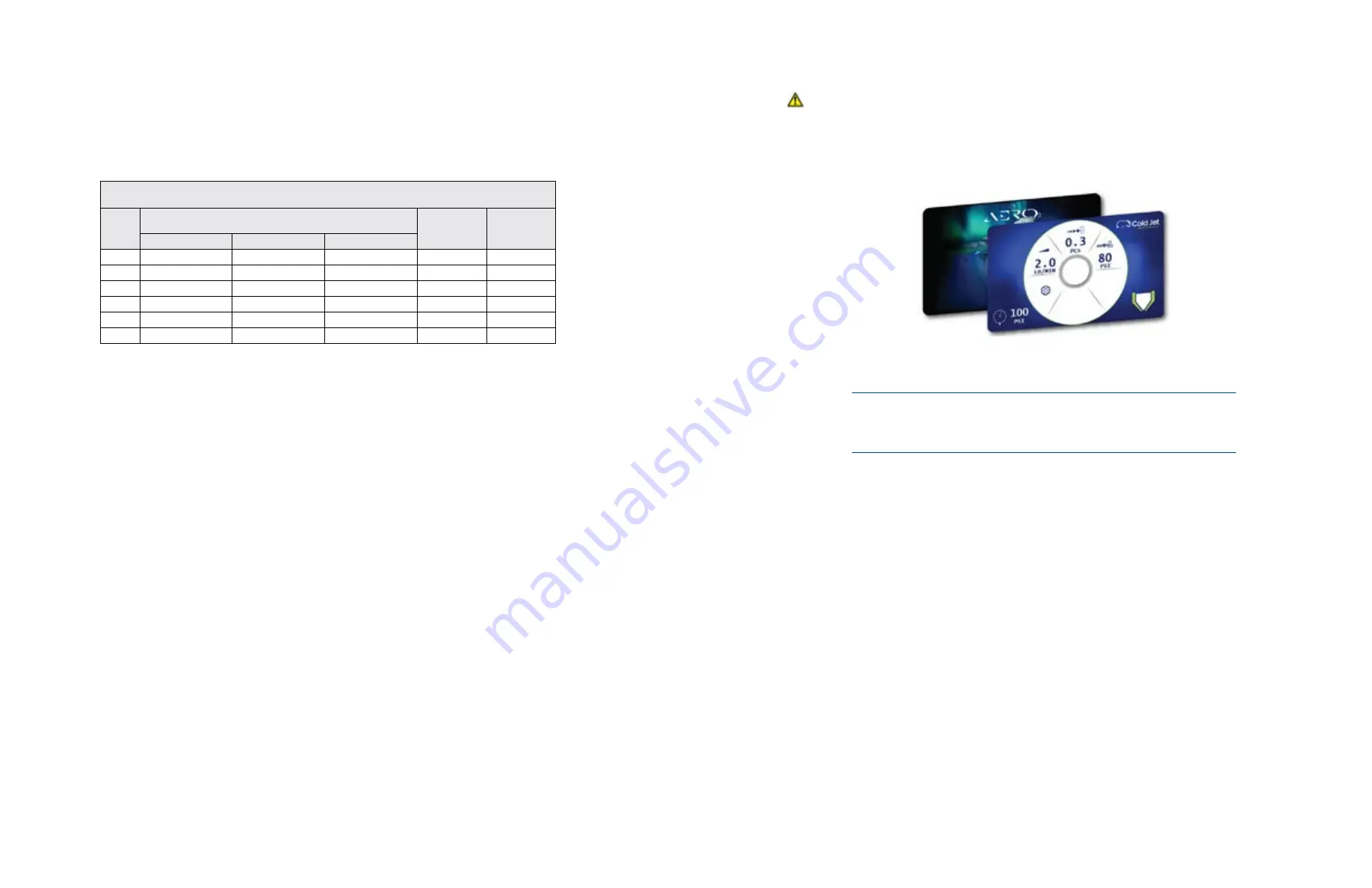
26
27
Compressed Air Supply
For best results while blasting, incoming air supply must be as free of oil and dirt as possible.
It is recommended that the incoming supply air— filters, oil filters, and water separators are
continuously monitored to ensure the PCS 60 receives the air your machine use is specified for. The
compressed air must have a low moisture level for optimal and continued performance. The air
quality and standards are as follows:
ISO 8573.1 (2001) Compressed Air Quality Standard
Air Quality Classes
Class
Solid Particle
Maximum number of particles m
3
Water
Pressure
Dewpoint
°
C
Oil
(Incl. Vapour)
mg/m
3
0.1 - 0.5 micron
0.5 - 1 micron
1.0 - 5 micron
1
100
1
0
-70
0.01
2
100,000
1,000
10
-40
0.1
3
-
10,000
500
-20
1
4
-
-
1,000
3
5
5
-
-
20,000
7
-
6
-
-
-
10
-
Cold Jet Blasting Conditions and Minimum Recommended Air Quality Classes
(ISO 8573.1:2010(E) Pressure Dewpoint Requirement Only)
1.
Manual blasting, intermittent operation, with .12 inch (3mm) pellets (any density) - Class 4 or
lower.
2.
Manual blasting, intermittent operation, with .04 inch (1mm) micropellets or smaller particles
(Particle Control System) - Class 2 or lower.
3.
Automated blasting, continuous blasting 1 hour or more, with .12 inch (3mm) pellets (any
density) - Class 2 or lower.
4.
Automated blasting, continuous blasting for any amount of time, with .04 inch (1mm)
micropellets or smaller particles (Particle Control System) - Class 1.
The air purity classification given in this part of ISO 8573 is intended to provide a guide to the air
purity expected in the compressed air system rather than resulting from the inclusion of a single
air treatment component. It should be recognized that achieving any given air purity specification
cannot be done exclusively by a combination of equipment; the specification of the correct
lubricants/coolants and the correct control of physical parameters, such as temperature, are also
required. The correct control of such parameters as temperature has an effect on the physical
state of the liquids, which can become aerosols or vapours. To maintain the air purity within a
compressed air system, it is considered essential that suppliers’ recommendations regarding
maintenance intervals be followed.
Starting the PCS 60
WARNING
Never blast the display screen area of the PCS 60 with dry ice as this will cause
permanent damage to the screen.
Follow these instructions to start the blasting job:
1.
On the control panel, press the power button to turn the PCS 60 on.
Figure 9: Power Button ON Status
2. Purge the system:
Always purge the system with compressed air during start-up, after
breaks, and before loading dry ice. This will remove any accumulated
moisture, water, and ice in the system.
a.
On the Performance and Precision applicator, press the air+ice button (II) to activate
(green light indicates ON and pressing the II button again will set the system to OFF).
3. Using the rotary encoder dial, navigate to the feed rate indicator on the home screen and
adjust it to the maximum setting. The maximum feed rates in the PCS 60 change on the HMI
depending on what sized particle is selected. Max dry ice feed rates per particle size:
a.
0.3 & 0.4 mm - 2.5 lbs/min (1.13 kg/min)
b. 0.5 mm - 2.7 lbs/min (1.22 kg/min)
c.
0.6 mm - 2.8 lbs/min (1.27 kg/min)
d.
0.7 mm - 2.9 lbs/min (1.31 kg/min)
e.
0.8 to 2.9 lbs/min - 3.0 lbs/min (1.31-1.36 kg/min)
f.
3 mm - 4.0 lbs/min (1.81 kg/min)
4.
If no ice has been loaded into the hopper for an extended period of time (days), then press
the air + ice button (II) and pull the trigger and blast for 2 minutes.
a.
If ice has recently been loaded into the hopper but a break or delay in blast periods
has occurred, then press the air button (I) and pull the trigger for 2 minutess.
b.
Set the feed rate to its minimal setting.
Summary of Contents for AERO 2 PCS 60
Page 1: ...Original Instructions English 2202060730 REV D PCS 60 Operator Manual...
Page 27: ...46 47...
Page 28: ...48 49...
Page 29: ...50 51...
Page 30: ...52 53...