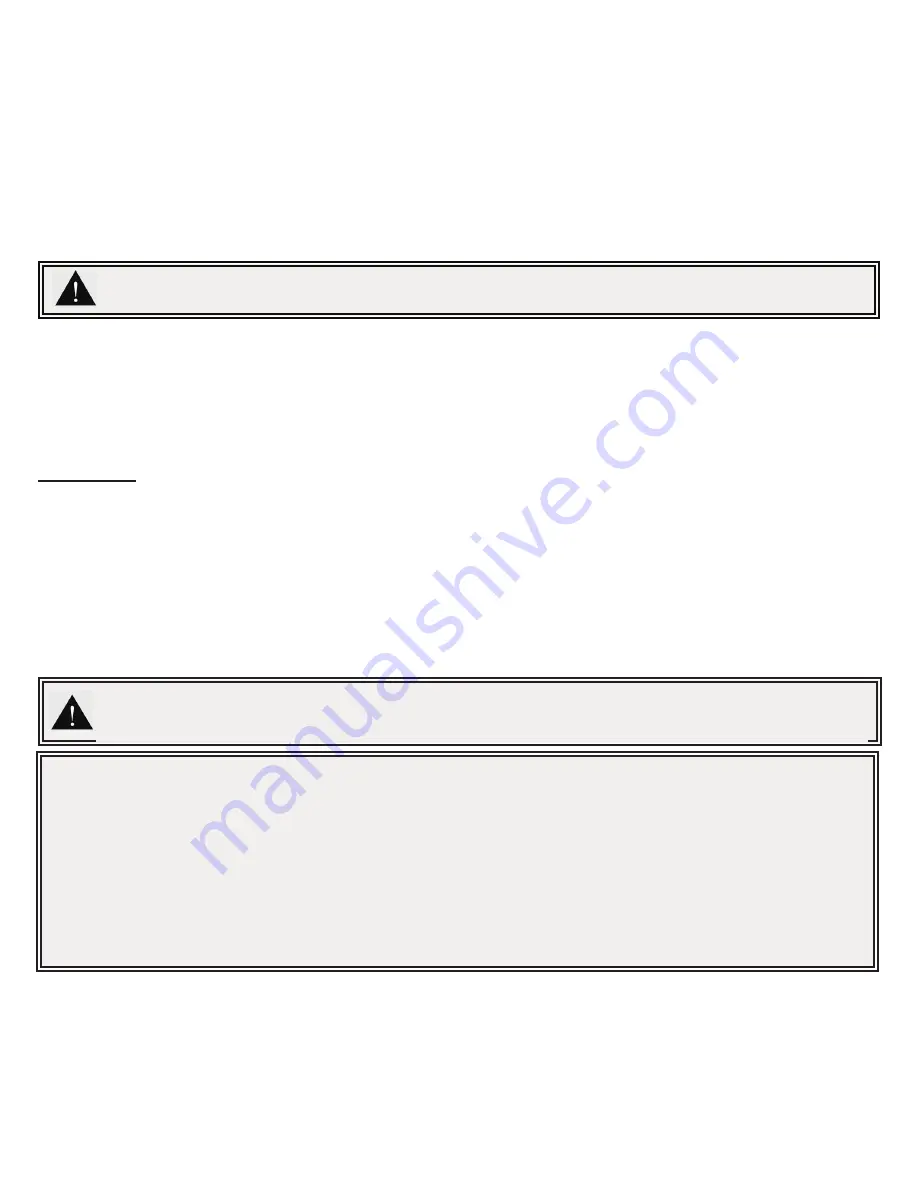
Page 2 of 12
Notes:
1. Larger wires and tight connections will provide longer service life for components. For high current wires it is highly recommended
that terminal blocks or soldered connections be used with shrink tubing to protect the connections. Do not use insulation displacement
connectors (e.g., 3M Scotchlock type connectors).
2. Route wiring using grommets and sealant when passing through compartment walls. Minimize the number of splices to reduce voltage
drop. All wiring should conform to the minimum wire size and other recommendations of the manufacturer and be protected from moving
parts and hot surfaces. Looms, grommets, cable ties, and similar installation hardware should be used to anchor and protect all wiring.
3.
Fuses or circuit breakers should be located as close to the power takeoff points as possible and properly sized to protect the wiring and
devices.
4. Particular attention should be paid to the location and method of making electrical connections and splices to protect these points from
corrosion and loss of conductivity.
5. Ground termination should only be made to substantial chassis components, preferably directly to the vehicle battery.
6. Circuit breakers are very sensitive to high temperatures and will “false trip” when mounted in hot environments or operated close to their
capacity.
Route the Unit’s cable as desired and plug the Unit’s Driver Side Center Cable Connector into the Passenger Side Connector.
Note: It is advisable to leave an extra loop of cable when installing the light bar to allow for future changes or reinstallations.
Single Color Versions:
For wiring the Single Color Versions of the SuperVisor Flex, connect the black lead to a solid frame ground,
preferably the (-) or ground side of the battery, & connect the remaining wires as shown in the Wiring Diagrams Labeled “Single Color
Version Wiring Diagrams” to the +12V terminal of the battery.
Multi Color Versions:
For wiring the Multi Color SuperVisor Flex, see the Wiring Diagram Labeled “Full 18 LED Multi Color Version Wiring
Diagrams” & see the Multi Color SuperVisor CC Controller Wiring Diagram.
Wiring Instructions:
LED Fusing Considerations - Single Color Independant Flashing Versions
Although the average current draw per module is very low, due to the type of circuit used to power each module, the instantaneous peak
current to a module can be significantly higher during low voltage conditions. To avoid prematurely blowing ATO style fuses or tripping
breakers it is recommended the following rule-of-thumb be used to size fuses or breakers. This is especially important in lightbars with many
LED modules running off a single fused source.
Minimum fuse size calculation: (See Wiring Diagrams)
For LED 12 volt electrical current
1.5 X (number of 9LED modules being fused) = Total Electrical Current at 12 VDC Nominal or
0.5 X (number of 3LED modules being fused) = Total Electrical Current at 12 VDC Nominal
LED MODULES
Operating Specifications - directional module: Operating Voltage:
10-16 VDC, Reverse Polarity Protection
Current Draw : Flashing Module
Red/Amber - .25A avg @ 12 VDC Nominal
Blue/White - .40A avg @ 12 VDC Nominal
Steady
Burn
Module
Red/Amber - .50A avg @ 12 VDC Nominal
Blue/White - .80A avg @ 12 VDC Nominal
LED Fusing Considerations - Multi Color CC Versions
NOTE: The Components of the Multi Color SuperVisor Flex System are circuit protected by the Multi Color SuperVisor Flex System
CC Board so the individual wires in the System do not require fusing.
WARNING!
Do not apply 12 volts to the wire colors that are not shown in the diagram for the version of the unit
you have purchased as this could potentially cause a direct short circuit.
WARNING!
Do not apply 12 volts directly to the supervisor flex wires after they are connected to the Supervisor
Multi Color CC Box. The Multi Color Supervisor Flex CC Board or the light heads could be damaged by applying 12
volts to the CC outputs.