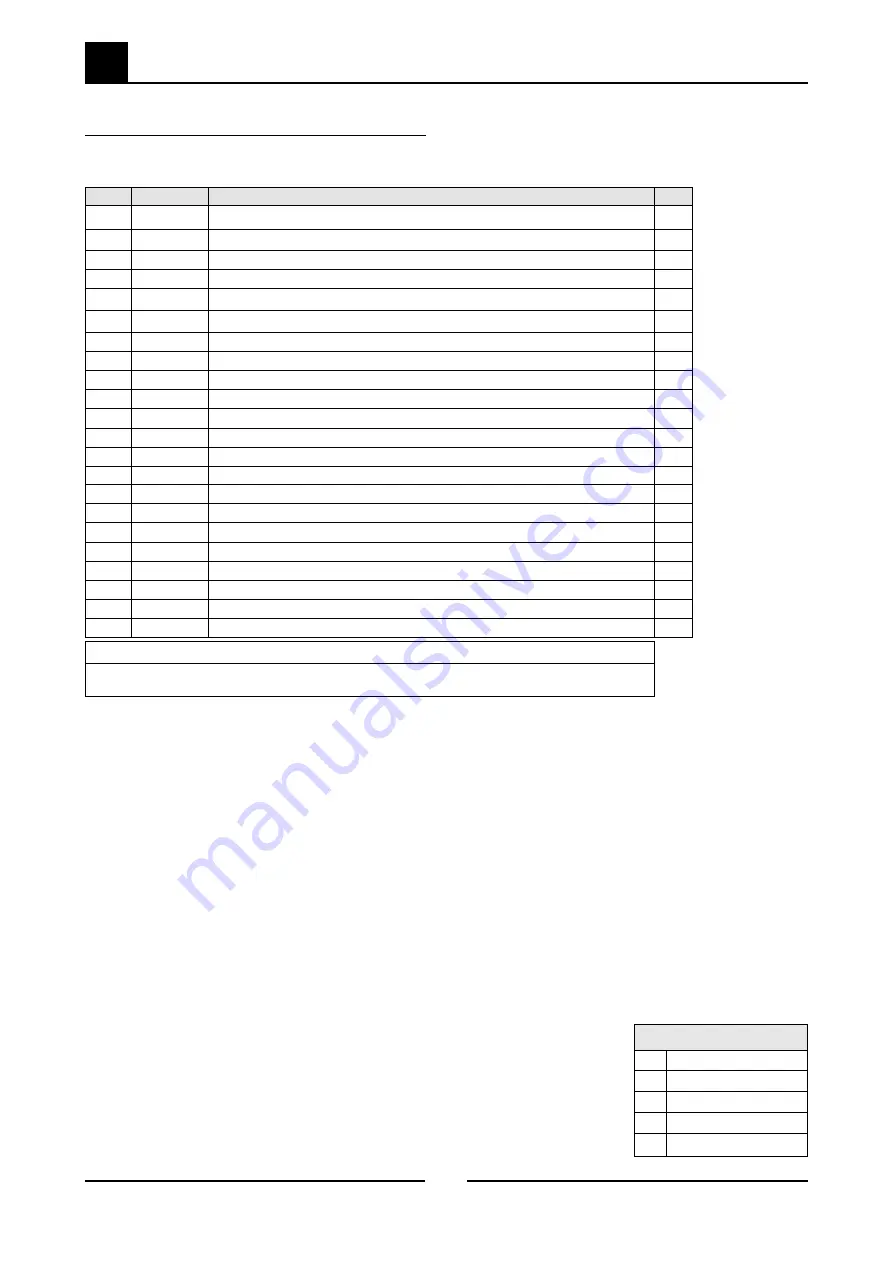
20
8
Exploded Parts Diagrams
Revision 2
©
Moffat Ltd, August 2012
Cobra Series Gas Barbeque
8.1 CB6
Gas
Barbeque
8.1.1 CB6 - Main Assembly
* Recommended Parts Level
RPL
Number of units in service
B 5-10
C 10-50
A 1-5
D 50+
Item Part No.
Description
*RPL
1
229883
SIDE PANEL LH
D
2
229882
SIDE PANEL RH
D
3
229879
FRAME WA
D
4
230585
SPLASHBACK
D
5
227445
BURNER SUPPORT
1)
D
5
233729
BURNER SUPPORT
2)
D
6
231479
BACK PANEL
D
7
229870
RADIENT CASTING COBRA
D
8
230587
COBRA BADGE
D
9
229869
GRATE COBRA
D
10
229860
INNER RADIATION PANEL
D
11
230584
HOB FRONT WA
D
12
230513
CONTROL PANEL
D
13
230586
PIZEO IGNITOR
A
14
228047
HT LEAD
A
229731 HT LEAD 250mm RING TERMINAL
(from serial# 472383)
A
15
229951
DRIP TRAY
C
16
230579
BASE PANEL
D
17
230577
LEG MTG PLATE COBRA
D
18
234059
LEG 2INCH ASSEMBLY COBRA
D
19
229674
REAR ROLLER ASSEMBLY
D
20
229671
LEG RING PLATE THREADED
D
1)
Up to Lot.No 0924xxx (Not interchangeable)
2)
From Lot.No 0925xxx (Not interchangeable)
Summary of Contents for CB6
Page 3: ...Revision 2 Moffat Ltd August 2012 Cobra Series Gas Barbeque ...
Page 34: ......