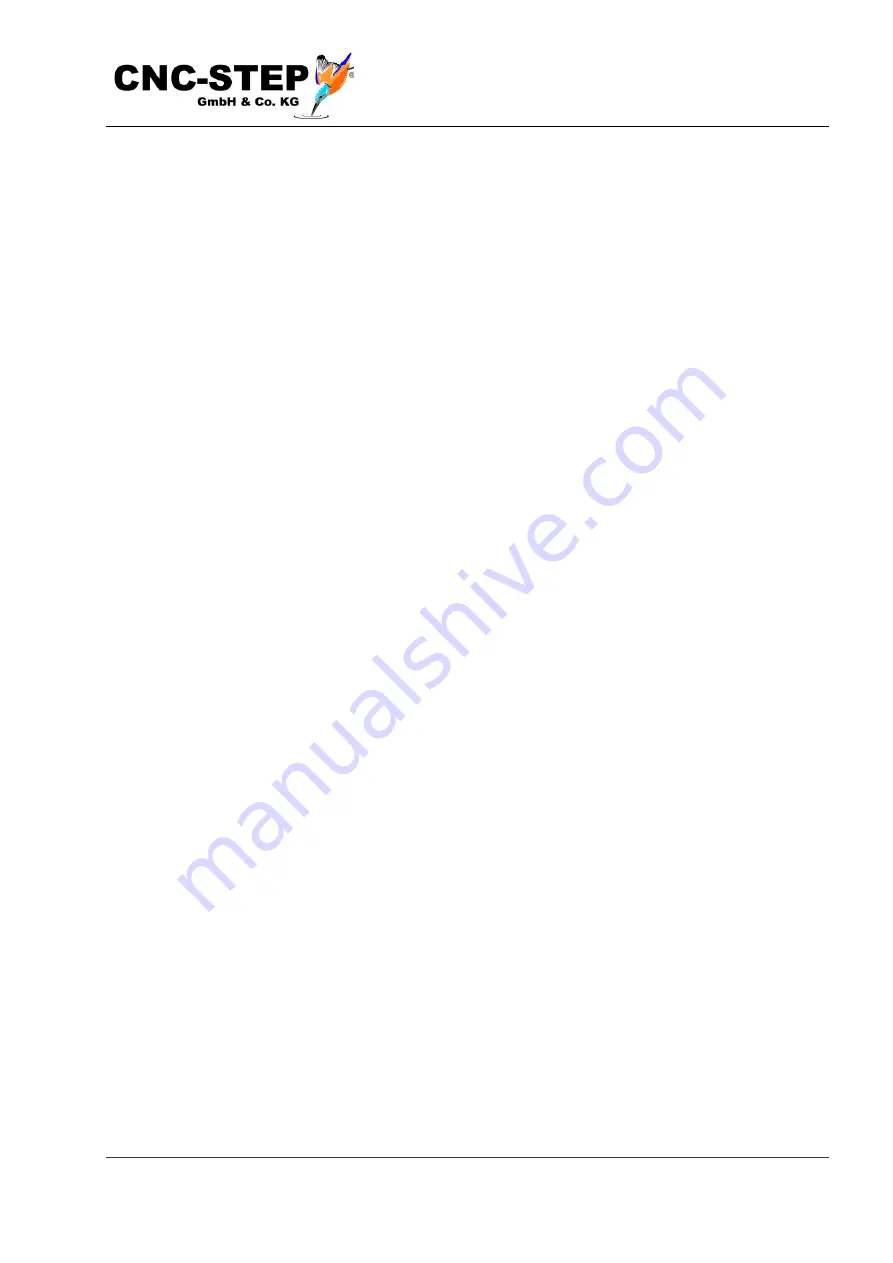
Operating Instructions
Zero-4 / 5-Channel Stepper Controller
CNC-STEP GmbH & Co. KG ▪ Siemensstrasse 13-15 ▪ 47608 Geldern ▪ Germany
Page 6
Support: +49 (0)2831/91021-50
6/16/2021
2
Features
Up to 4 axes or up to 5 stepper motors can be controlled. For one of the axes, two motors can be
used in parallel (X1, X2)
The phase current for the motors of the X, Y and Z axes can be set together to either 2.8 or 3.5A.
The phase current of the C-axis can be set separately in 4 steps between 1.4 and 3.5A. At a
standstill, the motor current is automatically lowered to 66%.
The step resolution can be selected for each axis separately between 1/5 and 1/10 micro step. This
corresponds to 1000 or 2000 steps per revolution for standard stepper motors (1.8° full step).
The 15-pin Sub-D connector of the C-axis has a 24V PWM output and a 12V power supply for
controlling tangential cutting modules. (z.B.TCM-4 or ETO-3) with or without oscillating knives.
If no oscillating knife is used, alternative a holding brake can be connected to the ST plug. By
switching the corresponding DIP switch, the 24V output on the ST connector is activated.
Both together is not possible!
Via a 9-pin Sub-D socket, the 4 reference or limit switches, as well as an emergency stop switch can
be connected. On a 25-pin Sub-D socket at the back, a 0...10V analog signal is available for speed
control with an (external) frequency converter.
Via two relays, the mains voltage for external consumers can be switched on and off by the software
at two sockets on the back. The sockets can each be loaded with 8A and are secured separately.
Via 12 LEDs on the front panel, the current operating status of the controller can be recognized at
any time.