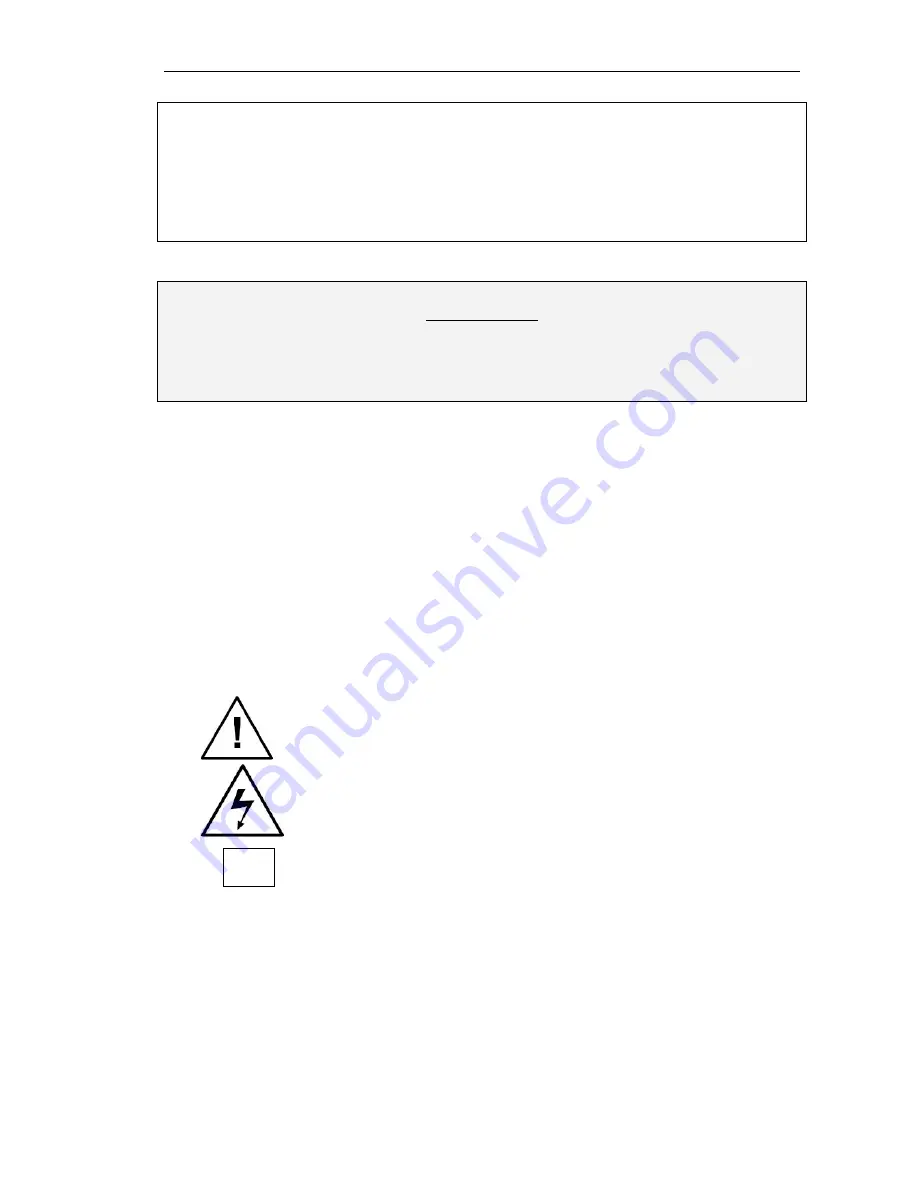
C.M.C. n.v. - Airmaster R1 installation guide – base unit – V1.1 – MANY0317A.00
Page 1 of 41
MANY0317A.00
Airmaster R1 hardware installation guide
for the base unit
Version 1.1
© Compressor & Machine Controls n.v. 2001-2003
safety warning!
Do not operate the Airmaster R1 until you and all personnel concerned have read and
understood this installation guide.
Important notes
Installation and startup may only be done by trained personnel according to safe engineering
practices and with the observance of all relevant local health and safety requirements and
regulations.
A requirement of fault-free operation and fulfillment of any rights to claim under guarantee
is that the documentation is observed. In case of doubt please contact CMC.
This document could be subject to changes. Please contact our factory in case of doubt in
order to ensure that you have received the latest version.
Signs:
Hazardous or harmful situation
Possible consequences: Slight or minor injuries.
Possible damage to the unit and the environment.
Electrical hazard:
Possible consequences: Severe or fatal injuries
Specific for the American (US) market
UL
Summary of Contents for Airmaster R1
Page 30: ...C M C n v Airmaster R1 installation guide base unit V1 1 MANY0317A 00 Page 30 of 41 ...
Page 31: ...C M C n v Airmaster R1 installation guide base unit V1 1 MANY0317A 00 Page 31 of 41 ...
Page 32: ...C M C n v Airmaster R1 installation guide base unit V1 1 MANY0317A 00 Page 32 of 41 ...
Page 33: ...C M C n v Airmaster R1 installation guide base unit V1 1 MANY0317A 00 Page 33 of 41 ...
Page 34: ...C M C n v Airmaster R1 installation guide base unit V1 1 MANY0317A 00 Page 34 of 41 ...