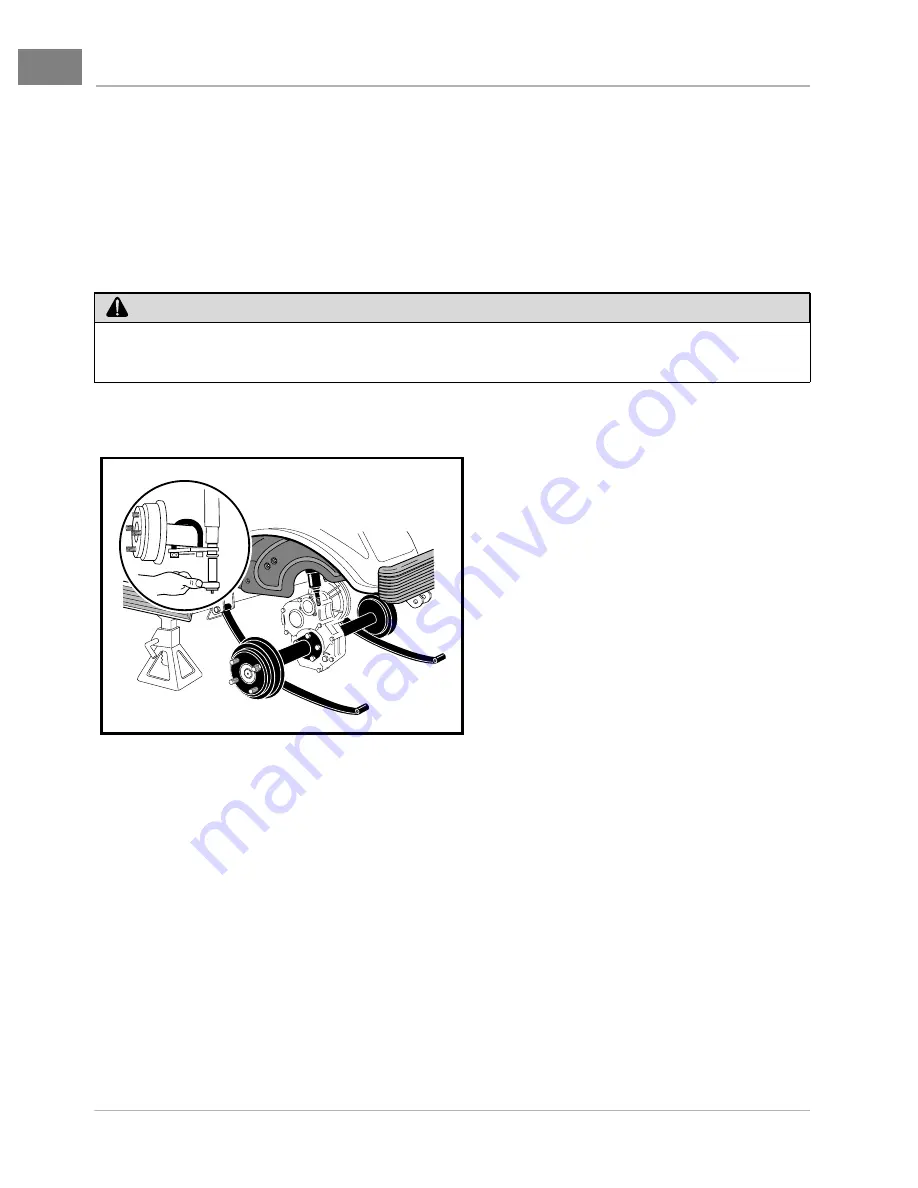
MOTOR
Motor
Page 15-4 1998/1999 PowerDrive Plus Maintenance and Service Supplement
15
Motor Removal, Continued:
5. Remove both rear wheels.
6. Remove the nut, cup washer, and bushing from the bottom side of the shock absorber. Compress the shock
absorber (pushing upwards) to move it out of the way.
7. Remove the nuts and bolts mounting the rear leaf springs to the shackles
(Figure 15-4, Page 15-4)
.
8. To gain easier access to the motor, lower the transaxle as low as it will go. If more room is needed, remove the
jack from beneath the transaxle and allow the springs to rest on the floor
(Figure 15-4, Page 15-4)
.
9. Remove the four bolts that mount the motor to the transaxle
(Figure 15-17, Page 15-13).
10. Carefully slide the motor away from the transaxle until the motor spline disengages the pinion and then
remove the motor from the vehicle.
Motor Disassembly
1. Before beginning disassembly, place match marks on the motor end shield and stator shell, then place the
motor in a vice with wooden blocks as shown
(Figure 15-5, Page 15-5)
.
2. Remove the four bolts (8) securing the end shield (10) to the stator shell (2)
(Figure 15-5, Page 15-5)
.
3. Remove the two screws (9) attaching the end shield to the bearing retainer
(Figure 15-5, Page 15-5)
.
4. Slide the armature (17) out of the opposite end of the stator shell
(Figure 15-5, Page 15-5)
.
5. Remove two screws (11) attaching brush rigging (12) to the stator shell (2)
(Figure 15-8, Page 15-7)
.
6. Mark the brush terminal posts (A1 and A2) (13) to identify their positions in the stator shell and winding assembly,
then remove the nuts (6) and flat washers (5)
(Figure 15-8, Page 15-7)
. From the outside, push the posts through
the stator shell wall into the interior of the stator shell and winding assembly.
7. Carefully remove the brush rigging and the terminal posts from the stator shell.
8. To remove brush springs (14)
from the rigging, lift the spring extensions out and over the brush mounts and
then slide the springs off their mounting tabs
(Figure 15-6, Page 15-5)
.
•
DO NOT PLACE FINGERS OR HANDS UNDER MOTOR DURING REMOVAL. SEVERE INJURY COULD RESULT IF
FINGERS OR HANDS ARE CAUGHT BETWEEN MOTOR AND AXLE TUBE.
Figure 15-4 Lower Axle
CAUTION
Summary of Contents for 1998 DS
Page 2: ......
Page 8: ...Page vi 1998 1999 PowerDrive Plus Vehicle Maintenance and Service Supplement...
Page 56: ...12...
Page 72: ...13...
Page 98: ...14...
Page 128: ...16...
Page 129: ...Club Car R NOTES...
Page 130: ...Club Car R NOTES...
Page 131: ......