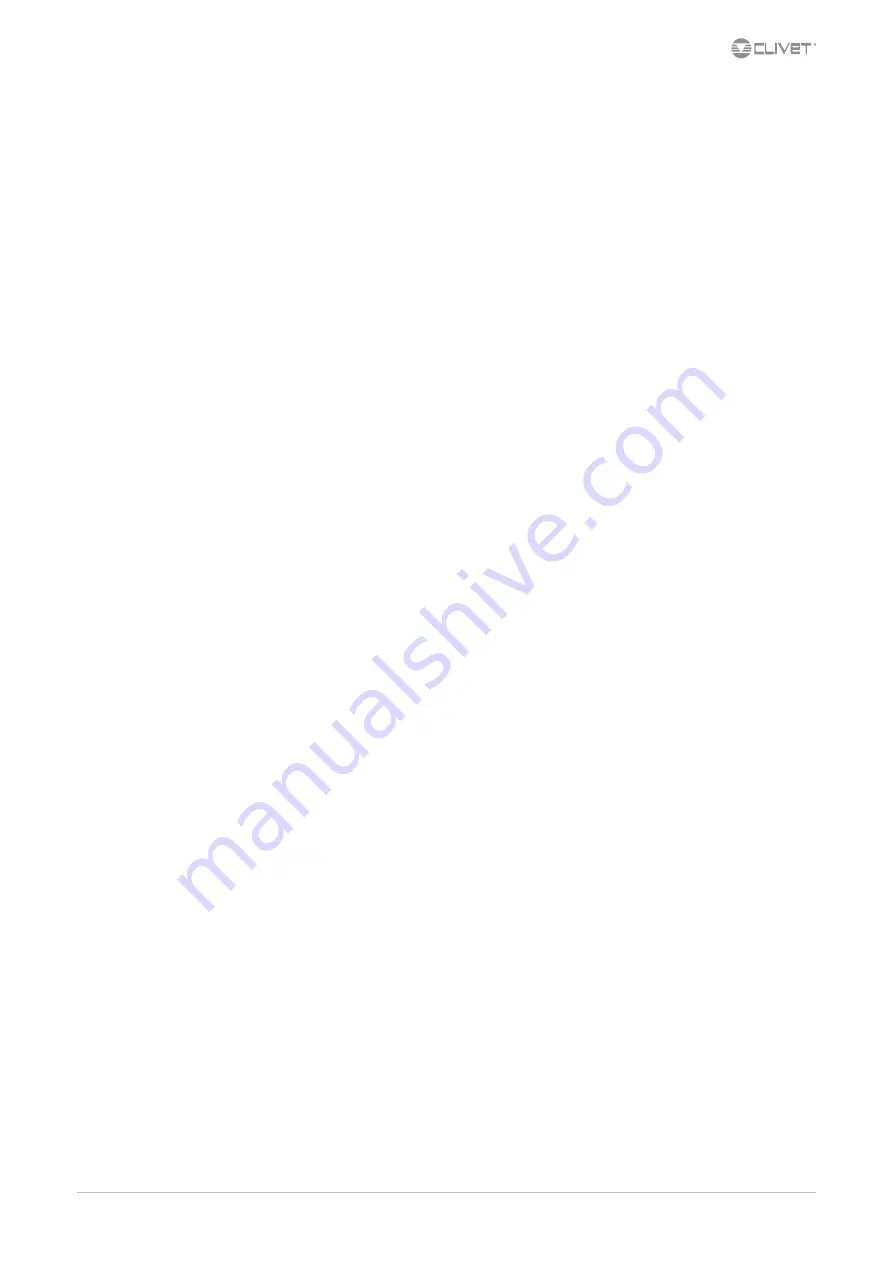
M08R40A15-02
WSHN-XEE2 MF 10.2-120.2
51
11 Residual risks
General description
In this section the most common situations are indicated,as these cannot be
controlled by the manufacturer and could be a source of risk situations for
people or things.
Danger zone
This is an area in which only an authorised operator may work.
The danger zone is the area inside the unit which is accessible only with the
deliberate removal of protections or parts thereof.
Handling
The handling operations, if implemented without all of the protection
necesssary and without due caution, may cause the drop or the tipping of
the unit with the consequent damage, even serious, to persons, things or the
unit itself.
Handle the unit following the instructions provided in the present manual re-
garding the packaging and in compliance with the local regulations in force.
Should the refrigerant leak please refer to the refrigerant “Safety sheet”.
Installation
The incorrect installation of the unit could cause water leaks, condensate
accumulation, leaking of the refrigerant, electric shock, poor operation or
damage to the unit itself.
Check that the installation has been implemented by qualified technical
personnel only and that the instructions contained in the present manual
and the local regulations in force have been adhered to.
The installation of the unit in a place where even infrequent leaks of inflam-
mable gas and the accumulation of this gas in the area surrounding the area
occur could cause explosions or fires.
Carefully check the positioning of the unit.
The installation of the unit in a place unsuited to support its weight and/or
guarantee adequate anchorage may result in consequent damage to things,
people or the unit itself.
Carefully check the positioning and the anchoring of the unit.
Easy access to the unit by children, unauthorised persons or animals may be
the source of accidents, some serious.
Install the unit in areas which are only accessible to authorised person and/or
provide protection against intrusion into the danger zone.
General risks
Smell of burning, smoke or other signals of serious anomalies may indicate a
situation which could cause damage to people, things or the unit itself.
Electrically isolate the unit (yellow-red isolator).
Contact the authorised service centre to identify and resolve the problem at
the source of the anomaly.
Accidental contact with exchange batteries, compressors, air delivery tubes
or other components may cause injuries and/or burns.
Always wear suitable clothing including protective gloves to work inside the
danger zone.
Maintenance and repair operations carried out by non-qualified personnel
may cause damage to persons, things or the unit itself.
Always contact the qualified assistance centre.
Failing to close the unit panels or failure to check the correct tightening of all
of the panelling fixing screws may cause damage to persons, things or the
unit itself.
Periodically check that all of the panels are correctly closed and fixed.
If there is a fire the temperature of the refrigerant could reach values that in-
crease the pressure to beyond the safety valve with the consequent possible
projection of the refrigerant itself or explosion of the circuit parts that remain
isolated by the closure of the tap.
Do not remain in the vicinity of the safety valve and never leave the refriger-
ating system taps closed.
Electric parts
An incomplete attachment line to the electric network or with incorrectly
sized cables and/or unsuitable protective devices can cause electric shocks,
intoxication, damage to the unit or fires.
Carry out all of the work on the electric system referring to the electric layout
and the present manual ensuring the use of a system thereto dedicated.
An incorrect fixing of the electric components cover may lead to the entry of
dust, water etc inside and may consequently electric shocks, damage to the
unit or fires.
Always fix the unit cover properly.
When the metallic mass of the unit is under voltage and is not correctly
connected to the earthing system it may be as source of electric shock and
electrocution.
Always pay particular attention to the implementation of the earthing
system connections.
Contact with parts under voltage accessible inside the unit after the removal
of the guards can cause electric shocks, burns and electrocution.
Open and padlock the general isolator prior to removing the guards and
signal work in progress with the appropriate sign.
Contact with parts that could be under voltage due to the start up of the unit
may cause electric shocks, burns and electrocution.
When voltage is necessary for the circuit open the isolator on the attachment
line of the unit itself, padlock it and display the appropriate warning sign.
Moving parts
Contact with the transmissions or with the fan aspiration can cause injuries.
Prior to entering the inside of the unit open the isolater situated on the con-
nection line of the unit itself, padlock and display the appropriate warning
sign.
Contact with the fans can cause injury.
Prior to removing the protective grill or the fans, open the isolator on the
attachment line of the unit itself, padlock it and display the appropriate
warning sign.
Refrigerant
The intervention of the safety valve and the consequent expulsion of the gas
refrigerant may cause injuries and intoxication.
Always wear suitable clothing including protective gloves and eyeglasses for
operations inside the danger zone.
Should the refrigerant leak please refer to the refrigerant “Safety sheet”.
Contact between open flames or heat sources with the refrigerant or the
heating of the gas circuit under pressure (e.g. during welding operations)
may cause explosions or fires.
Do not place any heat source inside the danger zone.
The maintenance or repair interventions which include welding must be
carried out with the system off.
Hydraulic parts
Defects in tubing, the attachments or the removal parts may cause a leak
or water projection with the consequent damages to people, things or
shortcircuit the unit.
Summary of Contents for WSHN-XEE2 MF 10.2
Page 13: ...M08R40A15 02 WSHN XEE2 MF 10 2 120 2 13 5 5 Connections performer by customer...
Page 46: ...46 WSHN XEE2 MF 10 2 120 2 M08R40A15 02 9 4 Source side 3 way modulating valve...
Page 47: ...M08R40A15 02 WSHN XEE2 MF 10 2 120 2 47 9 5 Source side 2 way modulating valve...
Page 48: ...48 WSHN XEE2 MF 10 2 120 2 M08R40A15 02 9 6 VALVE FOR DOMESTIC HOT WATER...
Page 63: ...Page intentionally left blank...