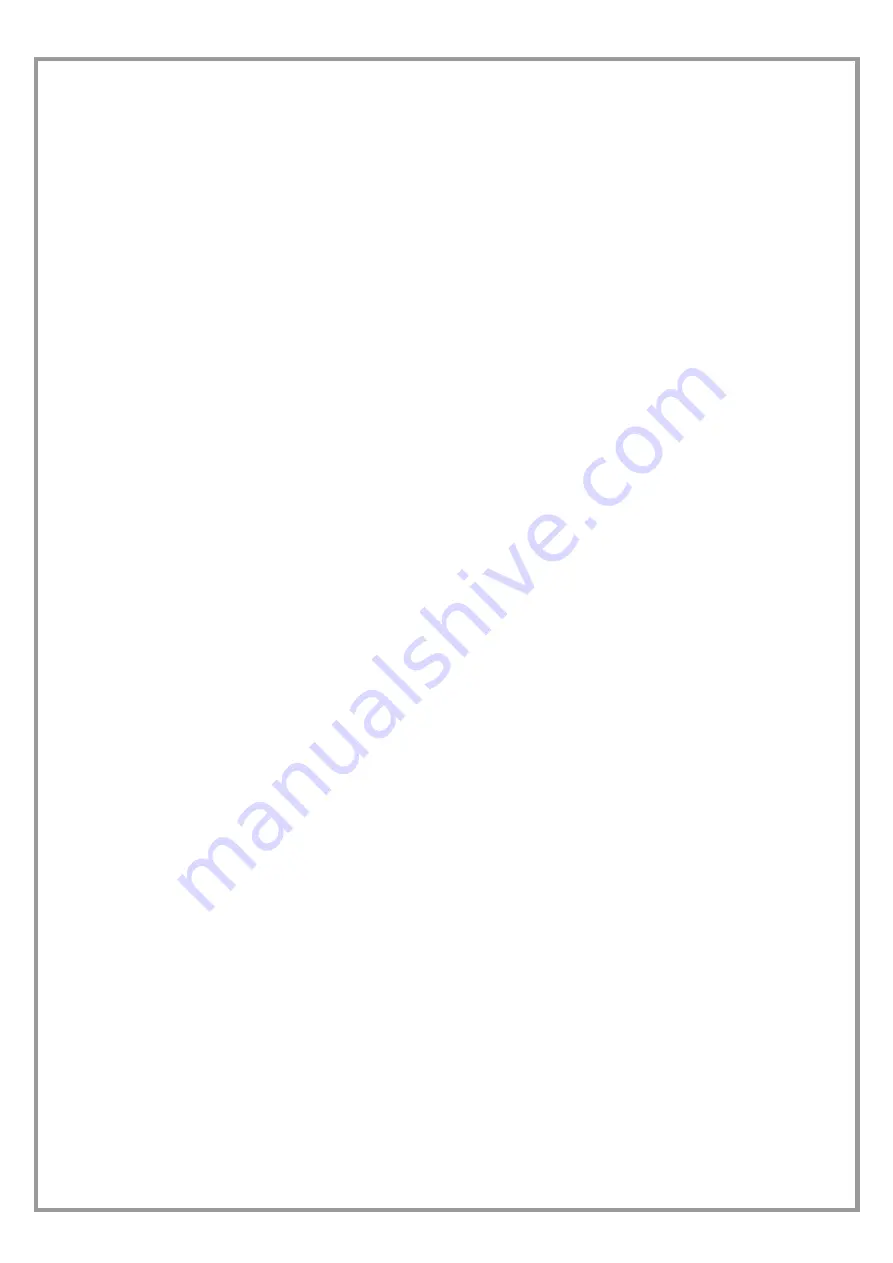
pag
39
ROUTINE MAINTENANCE
BEFORE UNDERTAKING ANY SORT OF MAINTENANCE OR CLEANING, DISCONNECT THE ELECTRICAL POWER
SUPPLY TO THE UNIT, AND ENSURE THAT OTHER PEOPLE CANNOT RE-CONNECT IT .
All equipment is subjected to wear out.
The maintenance makes :
1. keeps the unit efficiency
2. the components last longer
3. keeps their efficiency and limits breakdowns
Therefore, it is fundamental to perform periodical checks: a
few controls can be performed by the user
(AUTONOMOUS MAINTENANCE) and they are mainly
cleaning activities; otherwise, controls have to be
performed by specialized technicians (INSPECTIONS).
The machine should have a log book used to keep track of
the performed controls. This will make fixing up
breakdowns easier.
Take note of the date, type of control (autonomous
maintenance, inspection or fixing up), description of the
control, actions taken and so on.
SERVICES
Parts subject to intervention:
•
WATER CONDENSER
•
STRUCTURE
WATER EXCHANGER
It is very important for the exchanger to be able to provide
the maximum thermal exchange. Therefore, it is essential
for the inner surfaces to be clean of dirt and incrustations.
Periodically check the difference between the temperature
of the outlet water and the condensation temperature. If
the difference is greater than 8 °C – 10 ° C it is advisable
to clean the exchanger.
STRUCTURE
Check the condition of the parts making up the structure.
Paint so as to eliminate or reduce oxidation at the points in
the unit where this problem may occur. Check that the
panelling is fastened correctly. Poor fastening may give
rise to malfunctions and abnormal noise and vibration.
MAINTENANCE INSPECTIONS
Foresee inspection assistance carried out by authorized
centers or by qualified personnel.
The inspections should be carried out at least:
•
- Every year for only the cooling units
•
- Every six months for the cooling and warming
units
The frequency, however, depends on the use: in the event
of frequent use (continuous or very intermittent use, near
the operating limits, etc) or critical use (service necessary)
it is recommended to plan inspections at close intervals.
The inspections to be performed are as follows:
•
verify the power supply tension (when emptied or filled)
•
inspect the electrical board (status of solenoid starter
contacts, terminal closings, the status of wiring and
relevant insulations)
•
inspect the absorption of the single electrical loads
•
verify the cleaning and the efficiency of the exchangers
•
inspect the cleaning of the filters (air/water)
•
verify the leakage from the refrigerating circuit
•
Verify the protection devices (safety valves, pressure
switches, thermostats, etc.), the adjustment systems,
the control devices (alarm signalizations, probes,
manometers, etc)
•
check the operating parameters of the refrigerating
circuit (see the following REFRIGERANT TABLES and
the START-UP section)
For units equipped with safety valves, follow the
Manufacturer’s instructions.
Verify periodically the cleaning of the safety valves and
that oxidative / corrosive phenomena are not present, in
particular for installations near the sea, in industrial areas
or in rooms with a corrosive atmosphere.