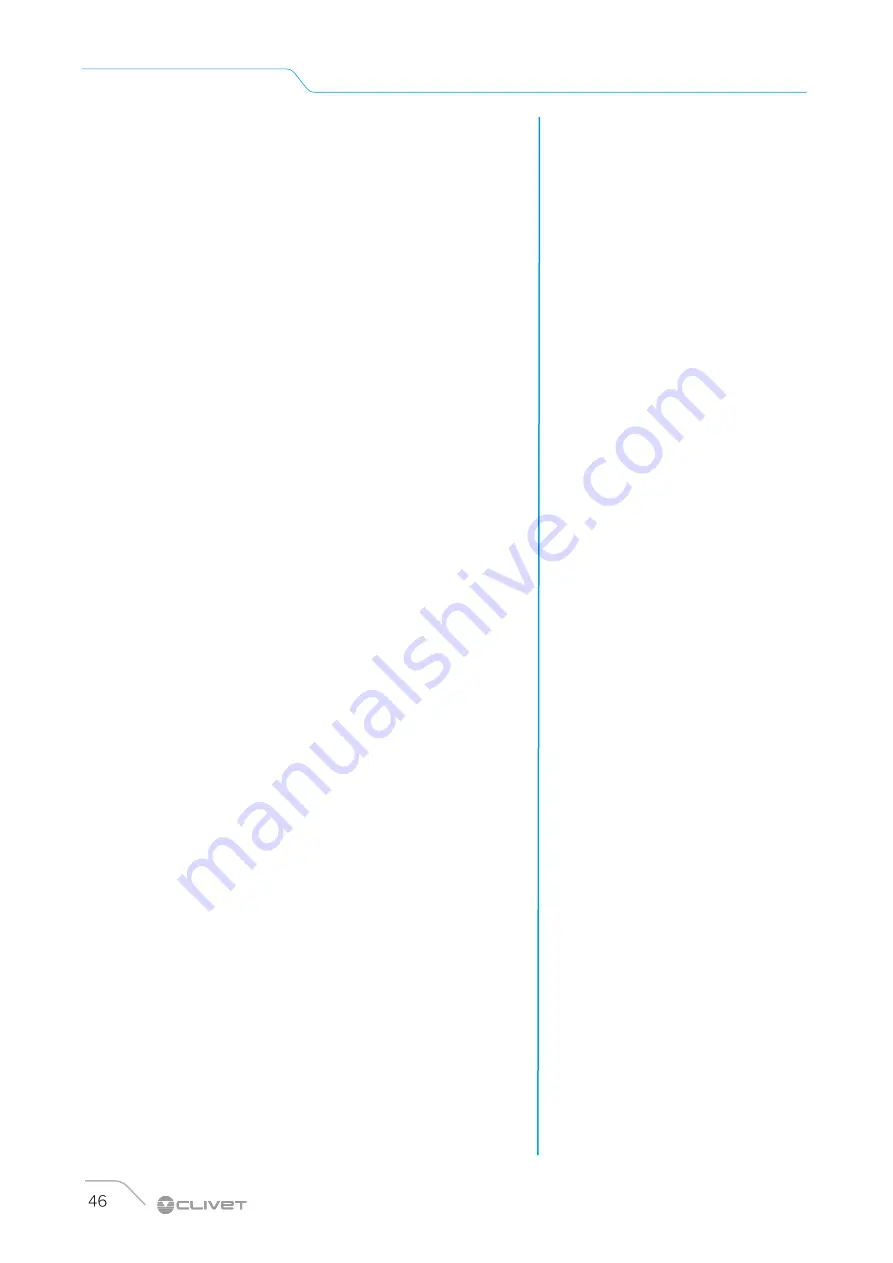
Reduced load operation
The units are equipped with partialisation steps and can therefore
operate with reduced loads.
However, a constant and prolonged operation with reduced load
with frequent compressor(s) stops and start-ups can cause
irreparable damages due to the absence of oil return.
The above-described operating conditions must be considered
outside the operating limits.
In the event of a compressor breakdown due to operating in the
above-mentioned conditions, the warranty shall not be valid and
Clivet spa declines any responsibility.
Periodically check the average operating times and frequency of
compressor start-ups: indicatively the minimum thermal load
must be such as to require a compressor to operate for at least
ten minutes.
If the average times are close to this limit, take the proper
corrective actions, for example, increasing the water content of
the system is not enough in this application.
Start-up report
To detect the objective operational conditions is useful to control
the unit over time.
With unit at steady state, i.e. in stable and close-to-work
conditions, identify the following data:
total voltages and absorptions with unit at full load
absorptions of the different electric loads (compressors, fans,
pumps etc)
temperatures and flows of the different fluids (water, air) both
in input and in output from the unit
temperatures and pressures in the feature points of the
cooling circuit (compressor, liquid, suction drain/unload)
The detections must be kept and made available during
maintenance interventions.
Directive 2014/68EU PED
Directive 2014/68EU PED also sets out the regulations for unit
installers, users and maintenance operators.
Refer to local regulations; briefly and as an example, see the
following:
Compulsory verification of the first installation:
only for units assembled on the installer's building site (for ex.
condensing c direct expansion unit)
Commissioning declaration:
for all units
Periodical checks:
to be executed with the frequency indicated by the
Manufacturer (see the “maintenance inspections” paragraph)