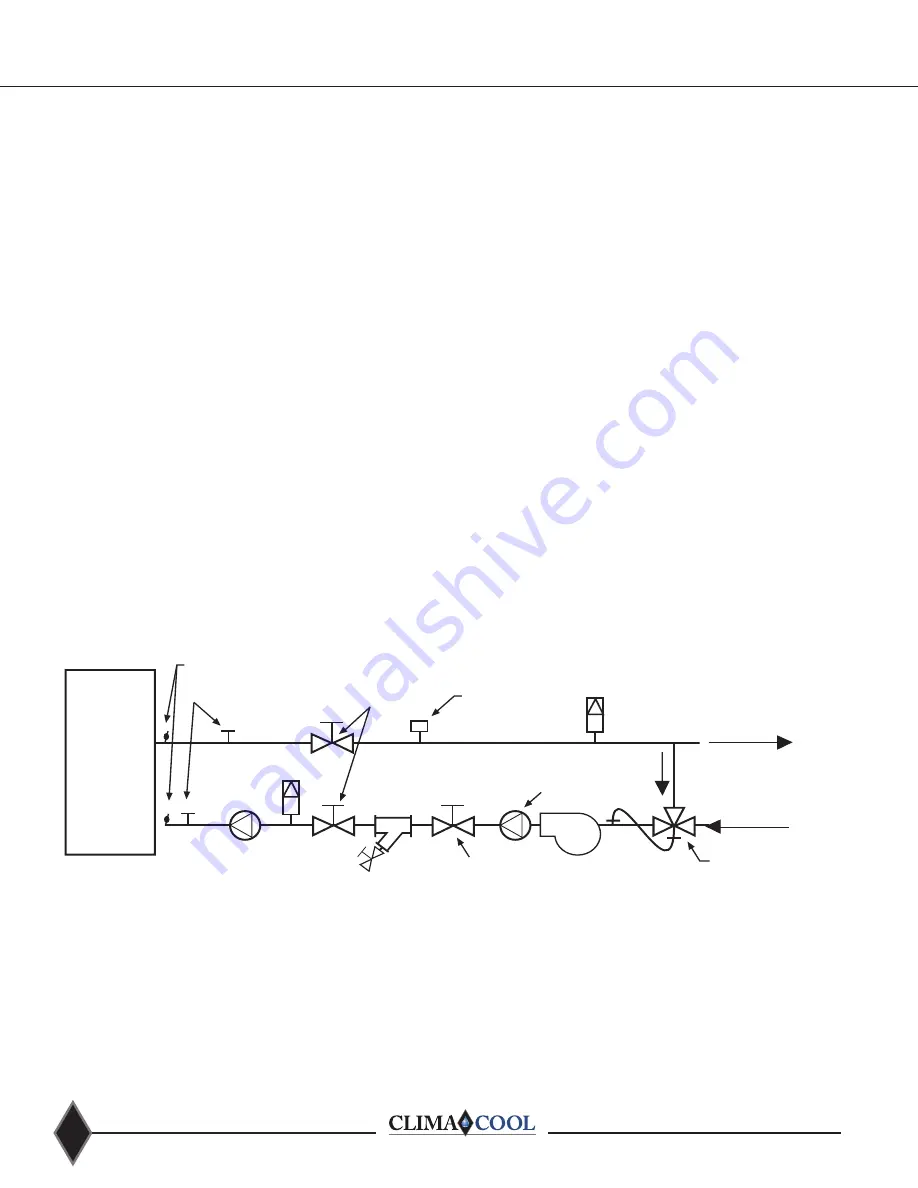
®
www.climacoolcorp.com
22
Chilled Water Temperature
Modules are designed for a leaving water temperature
range from 40°F to 62°F . All cataloged modules can operate
safely in this range without the need of special controls or
glycol additives . Leaving water temperatures below 40°F
can result in evaporator suction temperatures below the
freezing point of water . Therefore, a glycol solution additive
is required that will protect the evaporator from freeze ups
at lower operating suction temperatures . The full range of
leaving chiller fluid using glycol is 20°F to 62°F.
Condenser Water Temperature
The condensers are designed to operate most efficiently
at lower entering water temperatures for lower power
consumption . The expansion valve, however, relies on
the pressure difference across the valve to drive the liquid
refrigerant through . It is necessary to maintain a minimum
pressure differential across the thermal expansion valve
(equivalent to a 30°F difference between saturated
liquid temperature in the condenser and saturated vapor
temperature in the evaporator) to avoid loss of efficiency
and system performance. This pressure differential is most
commonly ensured by cycling the fans on the cooling tower
to maintain the entering condenser water temperature
above the minimum temperature of 60°F . An alternate
method to maintain the minimum entering condenser water
temperature above 60°F is to employ a bypass arrangement
as shown in Figure 24 below . This valve is an automatic
3-way bypass valve, which senses the temperature of the
mixed water entering the condenser . If this mixed water
temperature falls below 60°F the valve will re-circulate
the leaving condenser water and mix it into the entering
condenser water stream (bypassing the cooling tower).
The full range of entering condenser water is 60°F to 95°F
for standard applications and maximum leaving hot water
temperature of 135°F for high temperature applications .
For entering water less than 60°F refer to Motorized Water
Isolation Valves under Options and Accessories on page 41 .
Figure 24 - Condenser Water System
Note: Only required for equipment without motorized condenser valves.
Pressure Taps
Thermometer
Wells
Isolation Valves
Condenser Water
Flow Sensor or
Switch
Pressure Relief Valve
Flow to Tower Load
Flow from Tower
Cooling Tower
Bypass Valve
Strainer Isolation
Valve
Pump
Backflow
Preventer
Strainer
Drain
Valve
Backflow
Preventer
Pressure
Relief Valve
Water Temperature Requirements
Summary of Contents for UCH 30
Page 16: ... www climacoolcorp com 14 Voltage Phase Monitor Wiring ...
Page 21: ...19 www climacoolcorp com Figure 23 Part Load Performance Advantage ...
Page 57: ...55 www climacoolcorp com Wiring Diagrams 030 050 070 Cooling Only ...
Page 58: ... www climacoolcorp com 56 Wiring Diagrams 030 050 070 Cooling Only ...
Page 59: ...57 www climacoolcorp com Wiring Diagrams 030 050 070 Heat Pump ...
Page 60: ... www climacoolcorp com 58 Wiring Diagrams 030 050 070 Heat Pump ...
Page 61: ...59 www climacoolcorp com Wiring Diagrams 085 Cooling Only ...
Page 62: ... www climacoolcorp com 60 Wiring Diagrams 085 Cooling Only ...
Page 63: ...61 www climacoolcorp com Wiring Diagrams 085 Heat Pump ...
Page 64: ... www climacoolcorp com 62 Wiring Diagrams 085 Heat Pump ...
Page 65: ...63 www climacoolcorp com Wiring Diagrams Master Panel ...
Page 66: ... www climacoolcorp com 64 Wiring Diagrams Master Panel ...
Page 70: ... www climacoolcorp com 68 Notes ...