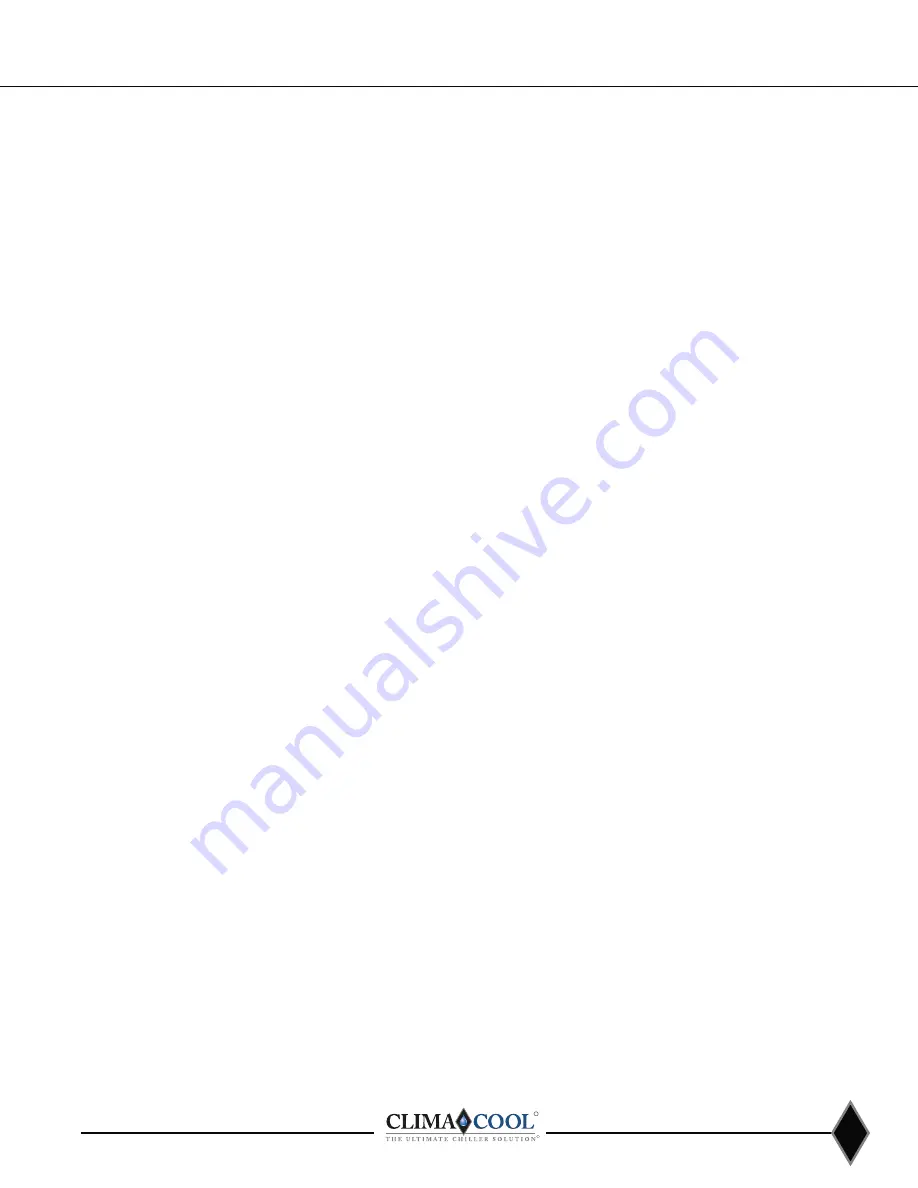
43
R
R
www.climacoolcorp.com
Conforming to local and national codes is the responsibility
of the service technician or installing contractor. The service
technician should be familiar with the following codes:
•
ASHRAE Standard Safety Code for Mechanical
Refrigeration, ANSI/ASHRAE 15-1978
•
American National Standard Code for Pressure Piping,
ANSI B31.5-1974
Factory Tested
ClimaCool modular chillers have been pressure-tested,
evacuated, fully charged and run tested at design water
ƪǤ
a refrigerant leak is detected at startup, the following
guidelines should be consulted before reprocessing the
refrigeration systems.
Refrigerant System Reprocessing
Debris and moisture can enter copper tubing in a matter
of minutes. All tubing, coil connections or any refrigerant
containing portions should be temporarily capped or sealed
to keep contaminants to a minimum. Filter driers should
Ƥǡƪ
system with dry nitrogen while brazing to prevent oxidation
inside the copper piping.
After all of the repairs have been made to the refrigeration
system, a pressure test using refrigerant and nitrogen
should be performed. Pressurize the system with dry
nitrogen to 20 psi and check for any obvious leaks. If no
leaks are present, introduce a “trace” amount of refrigerant
to the system (raise system pressure to 30-40 psi). With a
dry nitrogen tank equipped with a regulator set to 150 psi,
continue to pressurize the system to 150 psi. Using a leak
detector, carefully check the system for any remaining leaks.
If the system is free of leaks you may release the pressure.
Evacuating the System
The compressors should never run while the system is
in a vacuum.
This could cause immediate failure to the
compressors. After the system has been leak tested and
sealed, any moisture that entered the system should be
dehydrated and removed. While the pressure is reduced
under a vacuum, the boiling point of moisture trapped
inside the lines is also reduced. A pressure of .0095 psia,
or 500 microns absolute pressure or better must be reached
and sustained for several hours in order for the system to
be considered free from moisture. It is necessary to use a
micron meter equipped with an absolute pressure gauge
(or transducer) to take this reading. ClimaCool recommends
the double evacuation process to ensure the proper
removal of moisture and contaminants from the
refrigeration system. After the initial vacuum is reached and
held on the system, allow dry nitrogen back into the system
until the pressure reaches zero psig or slightly higher. Then,
repeat the entire evacuation process described above. The
evacuation process is considered complete
ONLY
after a
DzǦơdzǤ
DzǦơdzƤǣ
•
Pulling a vacuum level less than 500 microns on the
system and holding it for several hours.
•
Record the vacuum level in the system in microns,
ơ
15 minutes, and continue to monitor the micron level
inside the refrigeration system.
•
If the vacuum level inside the system does NOT rise
more than 400 microns above the recorded vacuum
level at the start of the 15 minute period, then the
evacuation process is complete.
If the vacuum level rises more than 400 microns in 15
minutes, then continue to evacuate the system for 1-2 hours,
DzǦơdzǤ
Recharging the System
After all repairs have been completed, the system has
been leak tested and proper vacuum pressures have been
reached and maintained, refrigerant may be recharged
into the system. With a known weight of refrigerant in
the cylinder, use the gauge manifold set to connect the
cylinder’s liquid charging port to the charging access port
near the refrigerant liquid line valve. Gradually meter the
appropriate weight of liquid refrigerant into the condenser
Ƥǡ
dispensed. Accurate refrigerant charge per circuit may be
found in the Physical Data information on pages 3-5. Then
Ƥ
of the system with refrigerant. Close the refrigerant cylinder
charging port, close all gauge manifold ports and start the
compressor. Be careful when continuing to charge the
balance of the refrigerant, constantly maintaining a positive
compressor suction pressure (>25 psig) at all times.
Refrigeration System Re-Processing and Charging
Summary of Contents for UCA 20
Page 18: ...R R www climacoolcorp com 16 Wiring Diagram Voltage Phase Monitor ...
Page 27: ...25 R R www climacoolcorp com Evaporator Water Pressure Drop Charts ...
Page 61: ...59 R R www climacoolcorp com Wiring Diagram UCA020 Cooling Only 208 230v 460v ...
Page 62: ...R R www climacoolcorp com 60 Wiring Diagram UCA020 Cooling Only 208 230v 460V ...
Page 63: ...61 R R www climacoolcorp com Wiring Diagram UCA020 HeatPump 208 230v 460v ...
Page 64: ...R R www climacoolcorp com 62 Wiring Diagram UCA020 HeatPump 208 230v 460v ...
Page 65: ...63 R R www climacoolcorp com Wiring Diagram UCA020 Heat Pump 575v ...
Page 66: ...R R www climacoolcorp com 64 Wiring Diagram UCA020 Heat Pump 575v ...
Page 67: ...65 R R www climacoolcorp com Wiring Diagram UCA020 SHC Heat Pump 208 230v 460v ...
Page 68: ...R R www climacoolcorp com 66 Wiring Diagram UCA020 SHC Heat Pump 208 230v 460v ...
Page 69: ...67 R R www climacoolcorp com Wiring Diagram UCA030 Cooling Only 208 230v 460v ...
Page 70: ...R R www climacoolcorp com 68 Wiring Diagram UCA030 Cooling Only 208 230v 460v ...
Page 71: ...69 R R www climacoolcorp com Wiring Diagram UCA030 Cooling Only 575v ...
Page 72: ...R R www climacoolcorp com 70 Wiring Diagram UCA030 Cooling Only 575v ...
Page 73: ...71 R R www climacoolcorp com Wiring Diagram UCA030 Heat Pump 208 230v 460v ...
Page 74: ...R R www climacoolcorp com 72 Wiring Diagram UCA030 Heat Pump 208 230v 460v ...
Page 75: ...73 R R www climacoolcorp com Wiring Diagram UCA030 Heat Pump 575v ...
Page 76: ...R R www climacoolcorp com 74 Wiring Diagram UCA030 Heat Pump 575v ...
Page 77: ...75 R R www climacoolcorp com Wiring Diagram UCA030 SHC Heat Pump 208 230v 460v ...
Page 78: ...R R www climacoolcorp com 76 Wiring Diagram UCA030 SHC Heat Pump 208 230v 460v ...
Page 79: ...77 R R www climacoolcorp com Wiring Diagram UCA030 SHC Heat Pump 575v ...
Page 80: ...R R www climacoolcorp com 78 Wiring Diagram UCA030 SHC Heat Pump 575v ...
Page 81: ...79 R R www climacoolcorp com Wiring Diagram UCF030 Free Cooling 208 230v 460v ...
Page 82: ...R R www climacoolcorp com 80 Wiring Diagram UCF030 Free Cooling 208 230v 460v ...
Page 83: ...81 R R www climacoolcorp com Wiring Diagram UCF030 Free Cooling 575v ...
Page 84: ...R R www climacoolcorp com 82 Wiring Diagram UCF030 Free Cooling 575v ...
Page 85: ...83 R R www climacoolcorp com Wiring Diagrams UCA070 Cooling Only 208 230v 460v ...
Page 86: ...R R www climacoolcorp com 84 Wiring Diagrams UCA070 Cooling Only 208 230v 460v ...
Page 87: ...85 R R www climacoolcorp com Wiring Diagrams Master Control Panel ...
Page 88: ...R R www climacoolcorp com 86 Wiring Diagrams Master Control Panel ...
Page 89: ...87 R R www climacoolcorp com Wiring Diagrams Expansion Board SHC Heat Pump ...