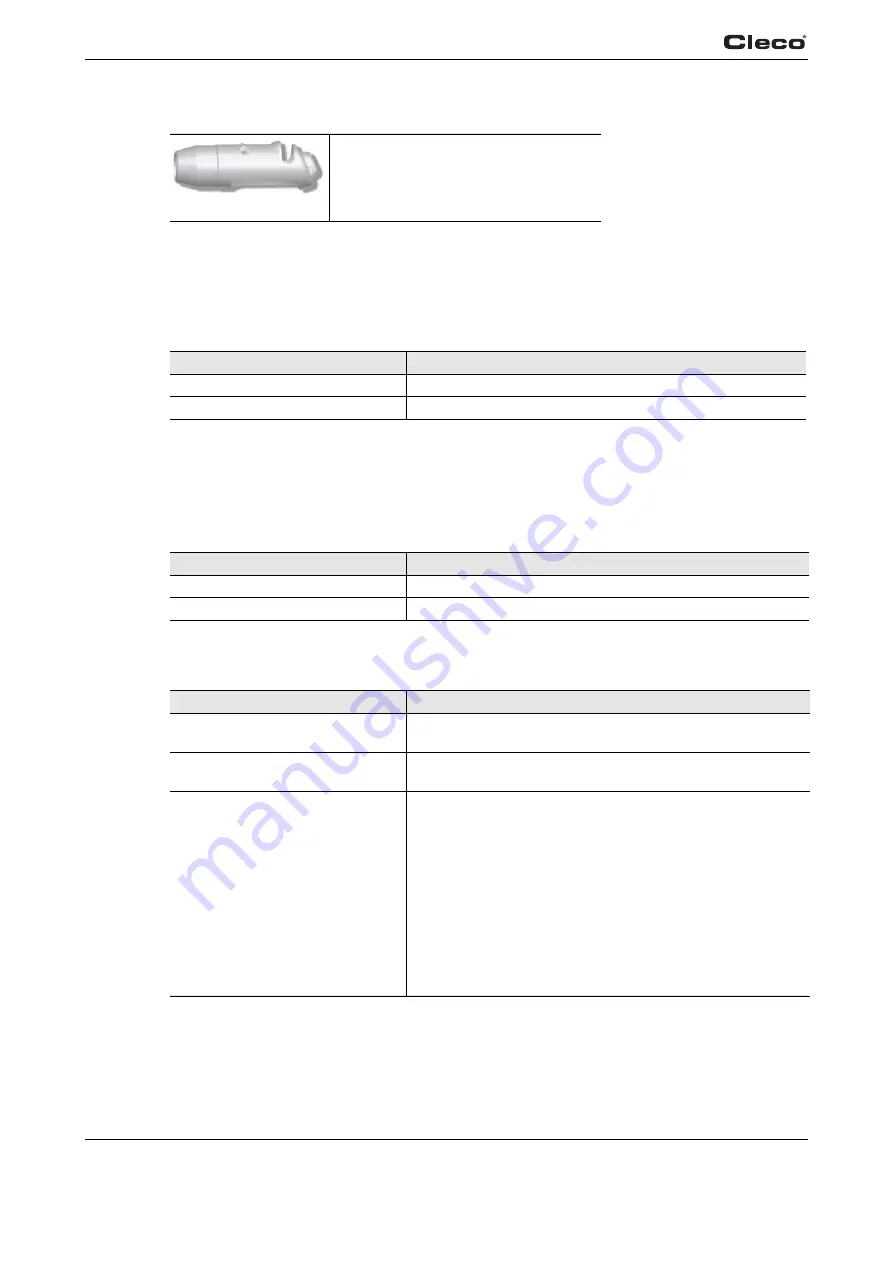
10
P1991BA/EN 2014-06
1994b_1_5_en-bedingt.fm, 12.06.2014
Before initial operation
4
3.2
Options
4
Before initial operation
4.1
Air supply
Make sure that the pressure before the pressure regulator is at least 0.5 bar higher than the required
inlet air pressure at the tool.
Keep the inside of the air hose free of residue; clean it if necessary.
Air quality
In accordance with ISO 8573-1, quality class 2.4.3, compressed air must be dry and clean.
Air preparation units
Our recommendation: air preparation units (filters, regulators, lubricators) should be installed
Protective sleeve
Order No. 937447PT – 11PHH…
Order No. 937442PT – 11PHHA…
Parameter
Data
Air hose
Inner diameter 3/8" (ø 9.5 mm), maximum length 5 m
Air inlet
1/4" NPT, inner diameter
7.5 mm
Parameter
Data
Working pressure range
400 … 700 kPa
Max. dew point
+ 10° C
Device
Explanation
Filter
Retention of particles > 15 micrometers.
Removes more than 90% of condensation.
Regulator
To attain constant work results, the working pressure must be
kept constant for every individual tool.
Lubricator
Compressed air requires a small amount of oil and is orientated to
the air consumption of the tool.
Calculate the time (
T
) between two drops of oil and make the
following settings at the lubricator:
F
= Factor for pulse nutsetter = 2
L
= Air consumption of tool at idle m³/min
(see performance data for pulse shut-off nutsetter)
T
60
F
L
-------------
=
Summary of Contents for 11PHH
Page 4: ...4 P1991BA EN2014 06 1991a_ Deckblatt_en fm 12 06 2014...
Page 14: ...14 P1991BA EN2014 06 1994b_1_5_en bedingt fm 12 06 2014 Before initial operation 4...
Page 20: ...20 P1991BA EN2014 06 1994c_Wartung_en bedingt fm 12 06 2014 Maintenance 5 Empty side...
Page 26: ...26 P1991BA EN2014 06 1994d_Reparatur_en bedingt fm 12 06 2014 Assembly instructions 7...