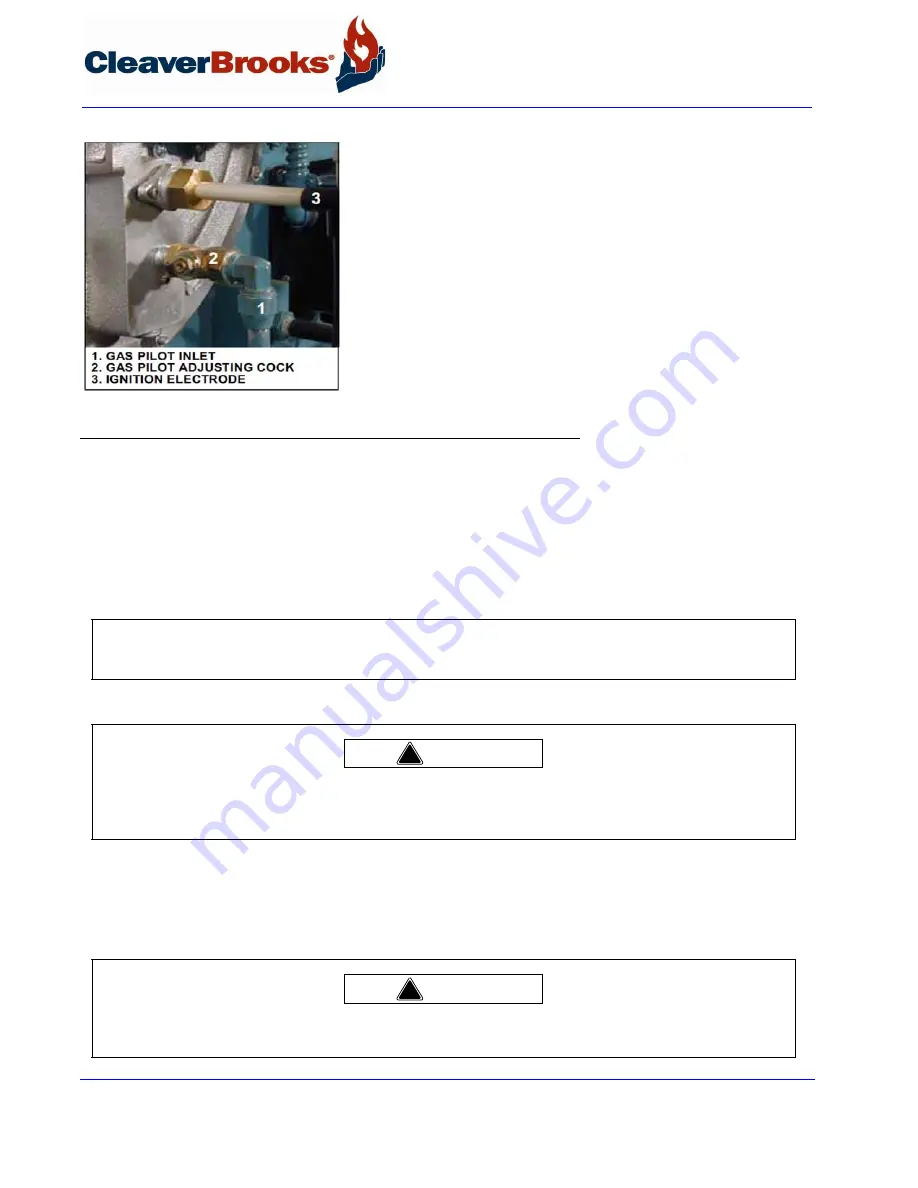
Adjustment Procedures
6-12
750-211 (revised 2009)
Promethean Boilers, Model 4WI Manual
The program relay used may be of the type that provides message infor-
mation that includes a constant flame signal of DC voltage. In this case
a separate DC voltmeter is not required.
To measure and adjust the pilot:
1.
When making a pilot adjustment, turn the manual-automatic switch to
“manual” and the program control to “close.” Open both the pilot cut-
off cock and the pilot adjusting cock. The main gas cock should remain
closed.
The regulator in the pilot line, if provided, is to reduce the gas pressure
to suit the pilot’s requirement of between 5” to 10” WC. Regulator
adjustment is not critical, however, with a lower pressure the final
adjustment of the pilot flame with the adjusting cock is less sensitive.
FIGURE 6-12.
Gas Pilot Adjusting Cock and Electrode
2.
Connect the micro-ammeter.
3.
Turn the burner switch “on.” Let the burner go through the normal pre-purge cycle. When the ignition trial
period is signaled, set the program switch to the “Test” position to stop the sequence.
4.
If the pilot flame is not established within 10 seconds, turn off the burner switch. Repeat the lighting attempt.
5.
When the pilot flame is established, and with the pilot adjusting cock wide open, remove the flame detector
from the burner plate. The pilot flame can then be observed through this opening.
6.
To make the final adjustment, slowly close the gas pilot adjusting cock until the flame can no longer be seen
through the sight tube. Then slowly open the cock until a flame providing full sight tube coverage is observed.
The adjustment must be accomplished within the time limit of the safety switch or approximately 30 seconds
after the detector is removed. If the control shuts down, manually reset it. Replace the detector and repeat the
process from step 5.
NOTE:
On an initial starting attempt, portions of the fuel lines may be empty and require “bleeding” time. It is better
to accomplish this with repeated short lighting trial periods with intervening purge periods than to risk prolonged fuel
introduction. If the pilot does not light after several attempts, check all components of the pilot system.
Wear a protective shield or suitable glasses and keep eyes sufficiently away from the sight tube opening. Never remove
the flame detector while the main burner is firing. Failure to follow these instructions could result in serious injury or
death.
When checking the pilot flame, be aware the electrode is energized. Failure to follow these instructions could result in
serious injury or death.
!
Warning
!
Warning
Summary of Contents for 4WI
Page 46: ...Burner Operation and Control 2 22 750 211 revised 2009 Promethean Boilers Model 4WI Manual...
Page 62: ...Waterside Care and Requirements 3 16 750 211 revised 2009 Promethean Boilers Model 4WI Manual...
Page 70: ...Sequence of Operation 4 8 750 211 revised 2009 Promethean Boilers Model 4WI Manual...
Page 114: ...Adjustment Procedures 6 28 750 211 revised 2009 Promethean Boilers Model 4WI Manual...