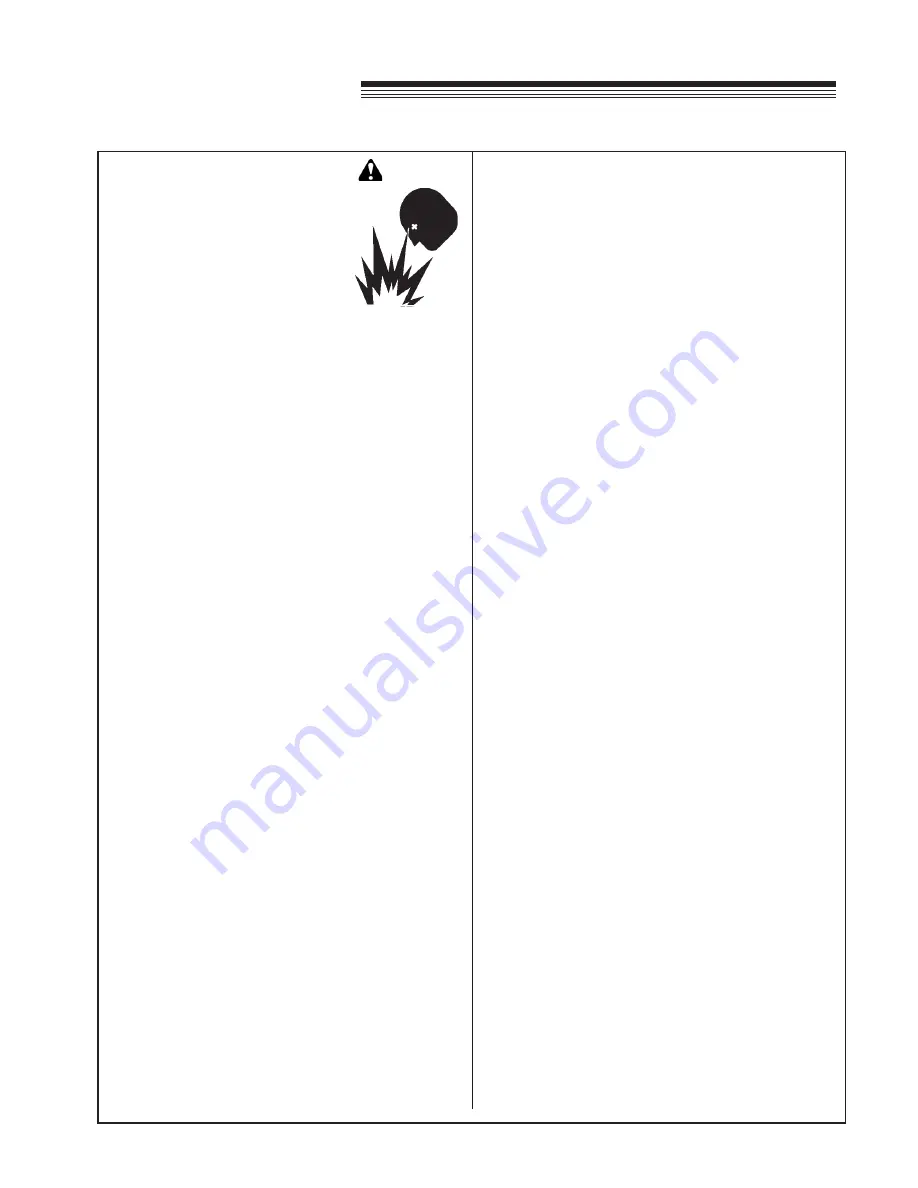
7
SA-30
SAFETY
BATTERY
Battery acid is caustic and fumes
are explosive and can cause seri-
ous injury or death.
To reduce the risk of personal in-
jury when working near a battery:
– Use protective equipment
such as, but not limited to,
goggles, face shield, rubber
gloves and apron when working
with battery acid.
– Avoid leaning over a battery.
– Do not expose a battery to open flames or
sparks.
– Be sure batteries with filler caps are properly
filled with fluid.
– Do not allow battery acid to contact eyes or skin.
Flush any contacted area with water immediately
and get medical help.
– Charge batteries in an open, well ventilated area,
away from sparks and flames. Unplug charger
before connecting or disconnecting from bat-
tery.
– Your unit is factory equipped with an AGM type
battery . An AGM type battery charger should be
used on these when charging.
STORAGE SAFETY
– Stop the engine and allow to cool before storing.
– Drain the fuel tank outdoors only.
– Store fuel in an approved container in a cool, dry
place.
– Keep the machine and fuel containers in a
locked storage place to prevent tampering and to
keep children from playing with them.
– Do not store the machine or fuel container near
heating appliances with an open flame such as a
water heater or an appliance with a pilot light.
– Keep gasoline storage area free of grass, leaves
and excessive grease to reduce fire hazard.
– Clean grass and debris from aerating units,
drives, mufflers and engine to help prevent fires.
JUMP STARTING
1. Be sure the jumper cables are in good condition.
Turn off the ignition and all electrical accessories
on both machines.
2. Position the machine with a good (charged) bat-
tery next to but not touching the machine with the
dead battery so jumper cables will reach.
3. When making cable connections:
- make sure the clamps do not touch anywhere
except to intended metal parts,
- Never connect a positive ("+" or red) terminal
to a negative ("–" or black) terminal.
- Make sure the cables won't get caught in any
parts after the engines are started.
4. Connect one end of the first jumper cable to the
positive
terminal on one battery. Connect the
other end to the
positive
terminal on the other
battery.
5. Connect one end of the other cable to the
negative
terminal of the machine with a good
(charged) battery. Make the final connection on
the engine of the machine to be started, away
from the battery.
6. Start the vehicle with the good battery, then the
machine with the discharged battery.
7. Remove the cables in the exact reverse order of
installation. When removing each clamp, take
care it does not touch any other metal parts while
the other end remains attached.
WARNING