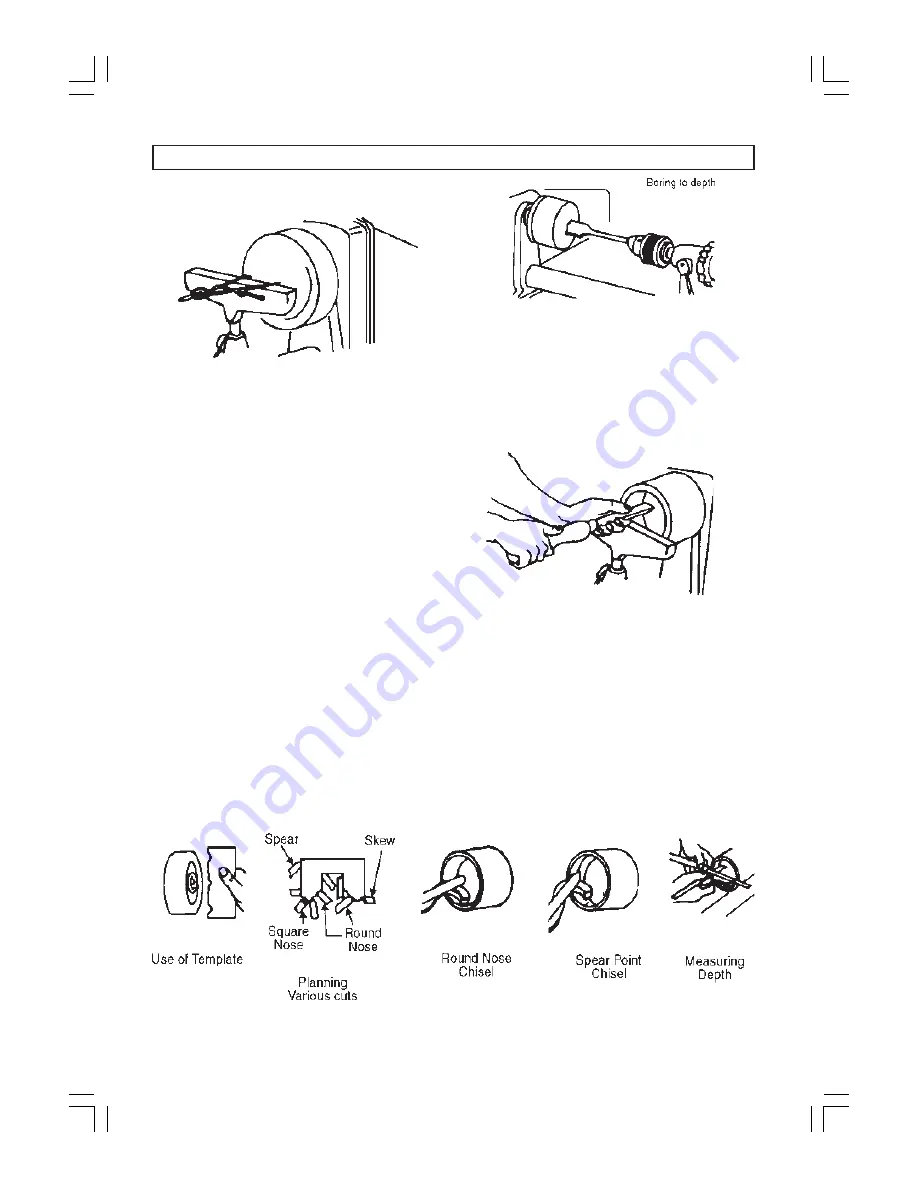
FACEPLATE & CHUCK TURNINGS
1.
PLANNING THE WORK
wood bit available. This can be accomplished
as illustrated above, or in any of the ways shown
on pages 18 & 19. Be careful to measure in
advance the depth to which the drill can be
allowed to go.
Now remove the bulk of the waste (to rough-
out the desired recess), by scraping with the
round-nose chisel or the gouge. Remove up to
within 1/8” of finished size in this manner.
Make a layout first, to provide a visual pattern
to follow while working the turning. Patterns can
be laid out in the same manner as spindle
patterns, or templates can be made which can
be held against the work for visual comparison.
Circles to locate the various critical points (at
which the contours of the faceplate take distinct
form) can be quickly scribed on the rotating
work by using dividers (see above).
2
PLANNING VARIOUS CUTS
The circumference of a faceplate turning is
roughed-out and finished in the same manner
as that for a spindle. Practically all of the
balance of the operations however, are done
by using scraping methods.
A few of the standard contours which are often
turned are illustrated in fig.56, which also shows
the proper chisels for shaping these contours.
Any roughing out to depth that must be done is
generally accomplished with the gouge held in
the scraping position.
3.
DEEP RECESSES
The first step is to remove as much wood as
possible by boring into the centre with the largest
Finish off the inside circumference by scraping
with the spear point chisel or skew. Smooth the
bottom of the recess by scraping it flat with the
flat nose chisel.
Proper support must be provided at all times for
the scraping chisels. Several tool rest positions
are shown in the accompanying illustrations.
Always endeavour to position the part of the rest
that supports the tool as close to the working
surface as possible.
The depth and squareness of the sides of the
recess can be quickly checked by holding one
of the straight sided chisels and a combination
square as shown.
29
Fig. 56
Fig. 57
Fig. 55
Fig. 58