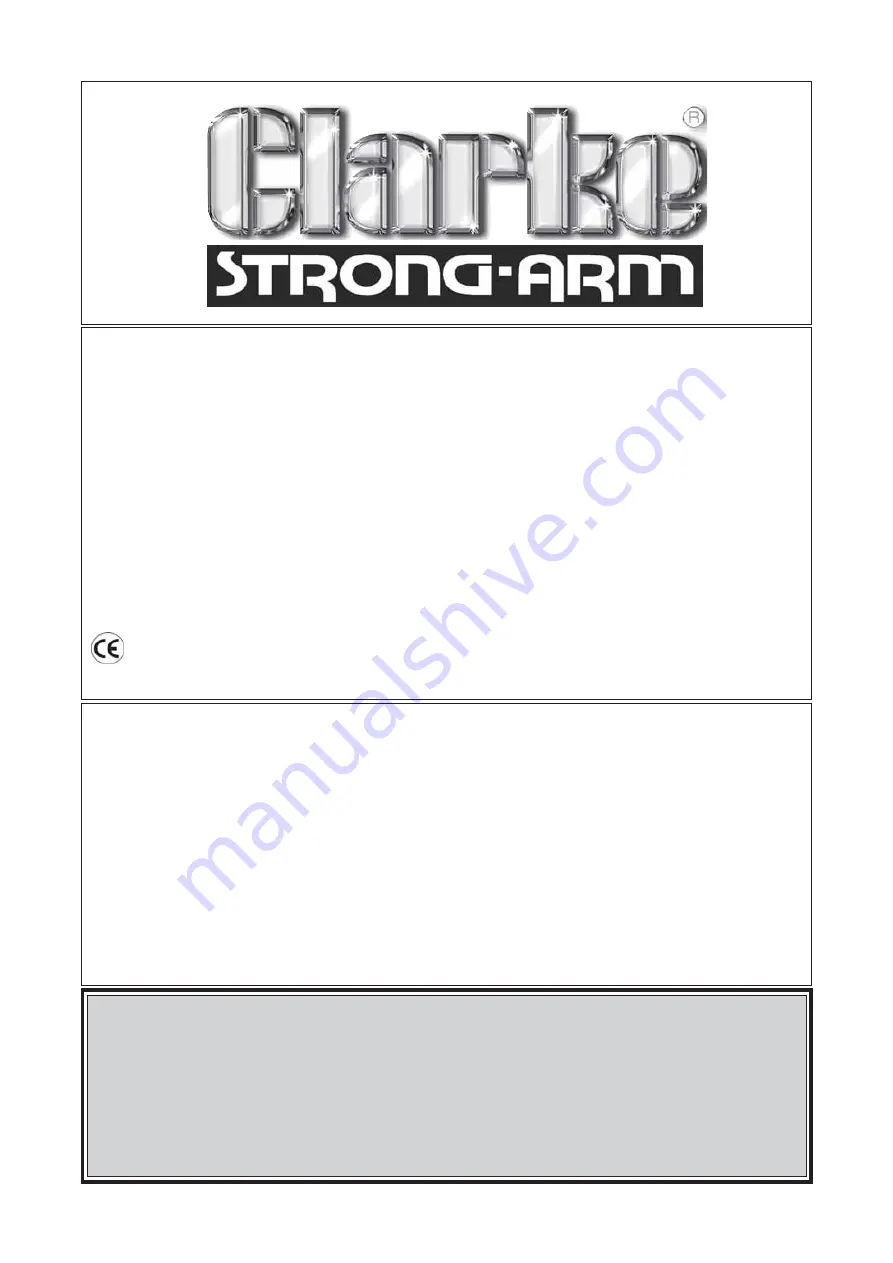
International
1
TWO POST VEHICLE LIFT
Model No: CPL30T
OPERATING & MAINTENANCE
INSTRUCTIONS
0703
Thank you for purchasing this CLARKE 2-Post Vehicle Lift which has been designed with safety in mind
and complies with all relevant European safety standards.
Before installation, it is important that you read this manual thoroughly and ensure the instructions are
carefully followed.
All operators of this equipment MUST read this manual before being allowed to use it. They must
ensure that all safety, operating and maintenance instructions are fully complied with, thus ensuring
the safety of themselves and others in the vicinity.
You can look forward to the Vehicle Lift giving you long and satisfactory service, provided the
instructions and maintenance schedules are carefully followed, .
Please note, that this manual is an integral part of the equipment, and should be kept with it at all
times. even in the event of re-sale.
GUARANTEE
This CLARKE product is guaranteed against faulty manufacture for a period of 12 months from
the date of purchase. Please keep your receipt as proof of purchase. This guarantee is invalid
if the product is found to have been abused, modified or tampered with in any way, or not
used for the purpose for which it was intended.
Faulty goods should be reported to your Clarke dealer immediately.
This guarantee does not effect your statutory rights.
Summary of Contents for Strong-Arm CPL30T
Page 2: ...International 2...
Page 22: ...International 22 Figure 1 MAIN COMPONENTS...
Page 23: ...International 23 Figure 2 DIMENSIONS...
Page 24: ...International 24 Figure 3 GROUND PLAN DIMENSIONS SWIVEL RANGE...
Page 25: ...International 25 Figure 4 CIRCUIT DIAGRAM...
Page 26: ...International 26 Figures 5 6 CONTROL BOX CONTROL CABLE...
Page 27: ...International 27 Figure 7 POWER SUPPLY 1...
Page 28: ...International 28 Figure 8 CONTROL ROD...
Page 29: ...International 29 Figure 9 OIL TANK for spindle lubrication...
Page 30: ...International 30 Figure 10 SUPPORTING SAFETY NUT...
Page 31: ...International 31 Figure 11 CARRIAGE...
Page 32: ...International 32 CARRIAGE Figure 12...
Page 33: ...International 33 Figure 13 SWIVEL ARM SHORT...
Page 34: ...International 34 Figure 14 SWIVEL ARM LONG...
Page 35: ...International 35 Figure 15 PARTS DIAGRAM...
Page 40: ...International 40...