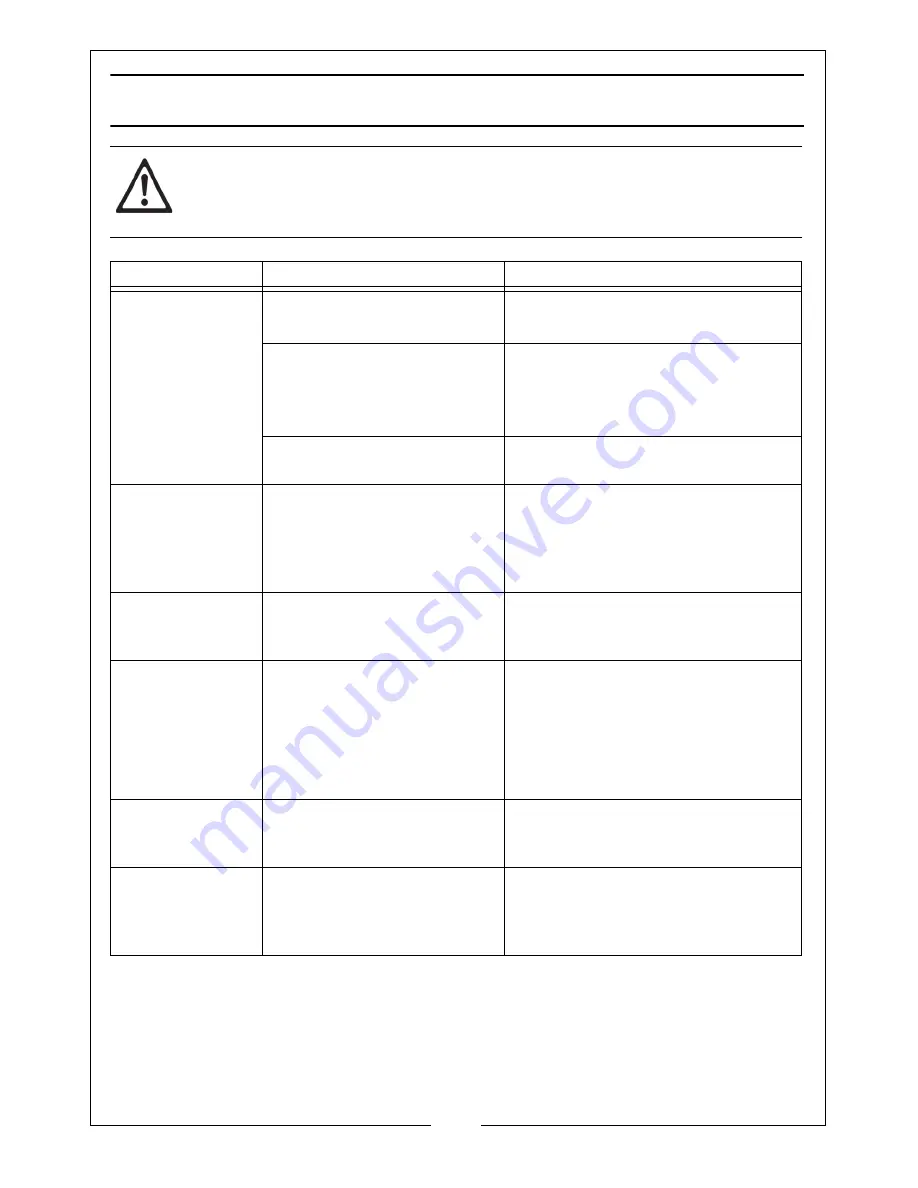
16
Parts & Service: 020 8988 7400 / E-mail: [email protected] or [email protected]
TROUBLESHOOTING
CAUTION: DO NOT TRY TO REPAIR OR ADJUST THIS COMPRESSOR IF YOU
ARE UNCERTAIN. IF YOU HAVE ANY QUERIES, CONTACT YOUR DEALER.
PROBLEM
PROBABLE CAUSE
REMEDY
The compressor
has stopped and
does not start.
Bad electrical connections.
1.
Check electrical connections.
2.
Clean and tighten if necessary.
Overload cutout switch has
tripped.
1.
Switch off and wait approx 5
minutes.
2.
Press the reset button and
switch on again.
Motor windings burnt out.
1.
Contact your Clarke dealer for
a replacement motor.
The compressor
does not reach
the set pressure
and overheats
easily.
Compressor head gasket
blown or valve broken.
1.
Return the machine to your
nearest service agent.
Compressor does
not start.
The reservoir has already fully
pressurised.
1.
Open drain valve to expel air.
Compressor should start again
when pressure reduces.
Air leaking from
the non-return
valve when the
compressor is not
running.
Faulty non-return valve.
1.
Drain receiver completely of
air.
2.
Remove the valve end plug,
3.
Carefully clean the valve seat
and the gasket
4.
Reassemble.
Air pressure from
the regulator will
not adjust.
The diaphragm within the
regulator body is broken.
1.
Replace regulator
The compressor is
very noisy and
makes a metallic
knocking sound.
Compressor damaged and
needs overhaul.
1.
Return the machine to your
nearest service agent.
Summary of Contents for RACER 9/50P
Page 24: ......