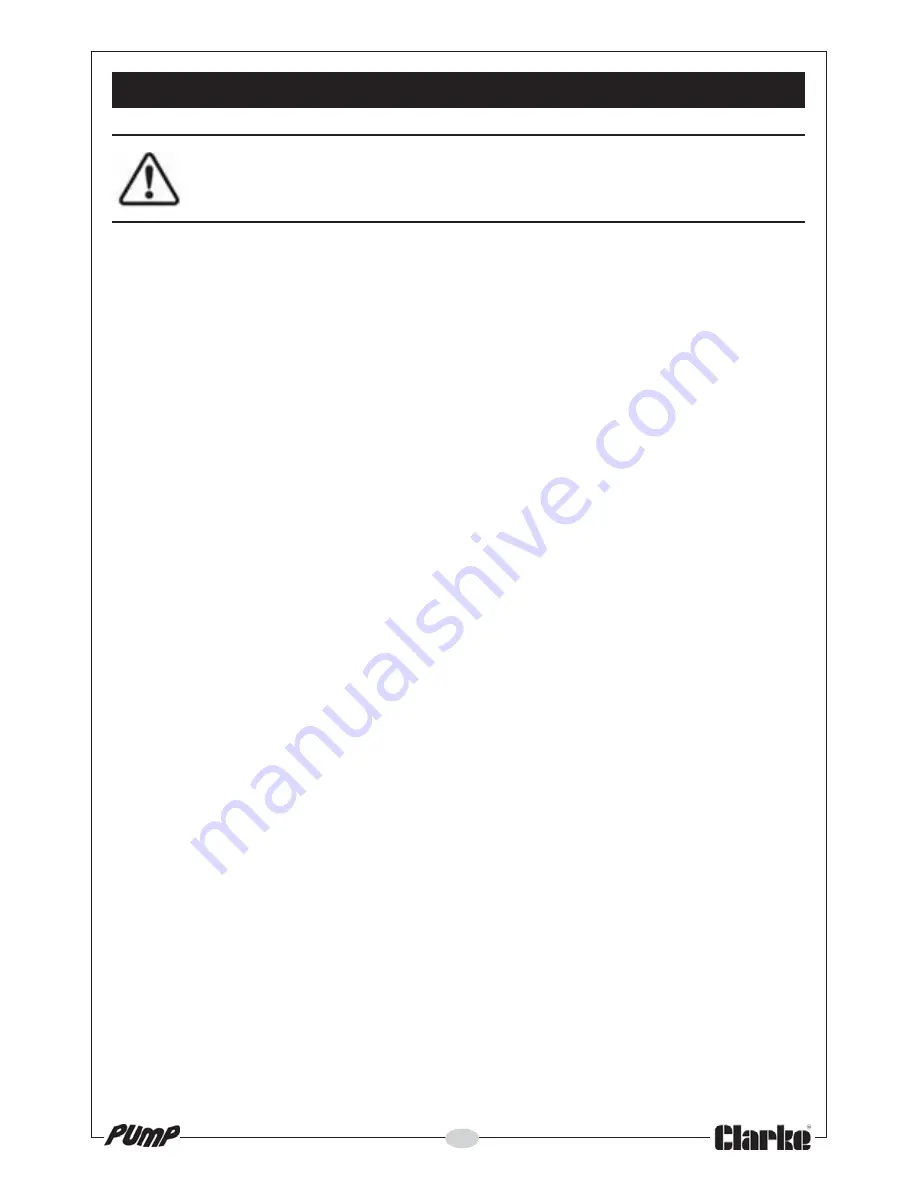
7
OPERATION
(REFER TO THE ILLUSTRATION ON PAGE 4)
WARNING: WHEN THE ENGINE IS RUNNING, THE EXHAUST MUFFLER IS
VERY HOT, TAKE CARE TO AVOID BURNS.
WARNING: NEVER RUN THE ENGINE IN AN ENCLOSED SPACE - ENSURE
THERE IS ADEQUATE VENTILATION.
Ensure the site and pump is prepared as detailed on page 6, then proceed as follows:
PRIMING & CONTROL
1.
With the fuel cock open, pull the starter recoil rope slowly two or three times, to allow fuel to
reach the carburettor.
2.
To start a cold engine, set the choke lever to the closed position, but if the engine is already
warm, the choke should be in the open position.
3.
Set the throttle about one third open. Turn the engine switch to ON.
4.
Pull the starter recoil rope firmly until the engine starts. Do not snatch at the starter rope and
allow it to retract slowly after each pull.
5.
Once the engine starts, gradually return the choke to the open position as the engine warms
up and use the engine throttle to gradually increase engine speed.
STARTING
After starting the engine, move the throttle to the open position for priming of the pump and
checking for pump output. Output is controlled by adjusting the engine speed.
NOTE:
With a suction lift of 5 to 10ft, the pump should begin discharging liquid in less than a
minute. A lift of 25ft (at sea level) should require not more than 2 minutes for initial prime. To
further reduce priming time the engine speed may be increased, after the engine is properly run
in. If pumping does not start within this time, shut off engine and check carefully to find the
problem. (See TROUBLESHOOTING on page 9).
NOTE:
Filling the suction pipe with water will speed up the priming process, and it is
recommended that a non-return valve be fitted to the end of the suction pipe.
On higher vertical lifts, a higher engine speed is necessary but on shallow lifts or when there is
little water to pump, preserve fuel and engine wear by reducing engine speed.
In the event of blockages, where debris has entered the suction chamber, the suction chamber
can be opened and cleaned out by removing the bolts shown in the layout on page 4.
SHUTTING DOWN
1.
Gradually reduce engine speed to minimum using the throttle lever.
2.
Stop the engine by switching OFF the ignition switch.
3.
Close the fuel cock.
Summary of Contents for PW2
Page 12: ...12 PUMP PARTS DIAGRAM MODEL PW2...
Page 14: ...14 ENGINE PARTS DIAGRAM MODEL PW2...
Page 16: ...16 PUMP PARTS DIAGRAM MODEL PW3...
Page 18: ...18 PARTS DIAGRAM PW3 ENGINE...
Page 20: ...20 DECLARATION OF CONFORMITY PW2...
Page 21: ...21 DECLARATION OF CONFORMITY PW2...
Page 22: ...22 DECLARATION OF CONFORMITY PW3...
Page 23: ...23 DECLARATION OF CONFORMITY PW3...
Page 24: ......