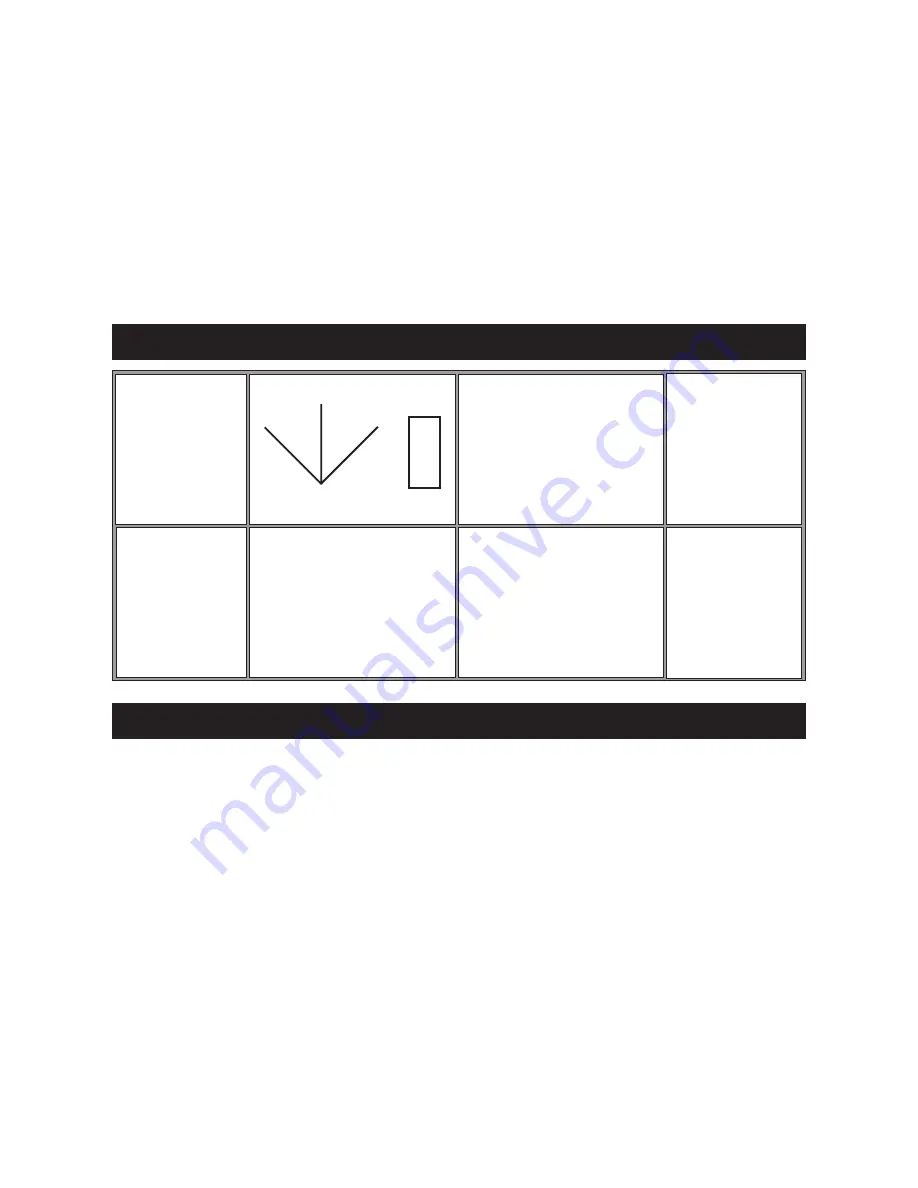
22
A change in wire diameter results in changed parameters. A smaller diameter
wire requires an increase in wire feed speed to reach the same current. If certain
limits are exceeded, a satisfactory weld cannot be obtained. These are:
A) A too high wire feed speed (too high with regard to the welding voltage)
results in pulsing within the torch. This is because the wire electrode dips into
the puddle and cannot be melted off fast enough.
B)
If the welding voltage is set too high, large drops can be seen at the end of
the wire electrode. These drops are often deposited beside the welding seam.
The correct rate of wire feed speed (current) and welding voltage, results in very
little spatter and a continuous, intensive hissing can be heard from the arc.
1.
Always weld clean, dry and well prepared material.
2.
Hold gun at a 45
°
angle to the workpiece with nozzle about 6mm from the surface.
3.
Move the gun smoothly and steadily as you weld.
4.
Avoid welding in very draughty areas. A weak pitted and porous weld will result due to air
blowing away the protective welding gas.
5.
Keep wire and wire liner clean. Do not use rusted wire.
6.
Sharp bends or kinks on the welding hose should be avoided.
7.
Try to avoid getting particles of metal inside the machine since they could cause short circuits.
8.
If available, use compressed air to periodically clean the hose liner when changing wire spools.
IMPORTANT: Disconnect from power source when carrying out this operation.
9.
Occasionally blow dust from the inside welder (LOW PRESSURE AIR). This keeps machine running
cooler. Note:
DO NOT
blow air over the printed circuit board and electronic components.
10. The wire feed roller will eventually wear during normal use. With the correct tension the pressure
roller must feed the wire without slipping. If the pressure roller and the wire feed roller make
contact (when the wire is in place between them), the wire feed roller must be replaced.
11. Check all cables periodically. They must be in good condition and not cracked.
1
2
3
Min
Max
Switches
SWITCH
POSITIONS
Steel wire
diameter
(mm)
Wire Speed
adjustment
1 - MIN
1 - MAX
2 - MIN
3 - MIN
2 - MAX
3 - MAX
0.6
0.6
0.6 - 0.8
0.6 - 0.8
0.8
0.8
LOW
LOW
MED.
MED.
MED. - HIGH
HIGH
WIRE SIZE SPECIFICATION CHART
WELDING TIPS AND MAINTENANCE