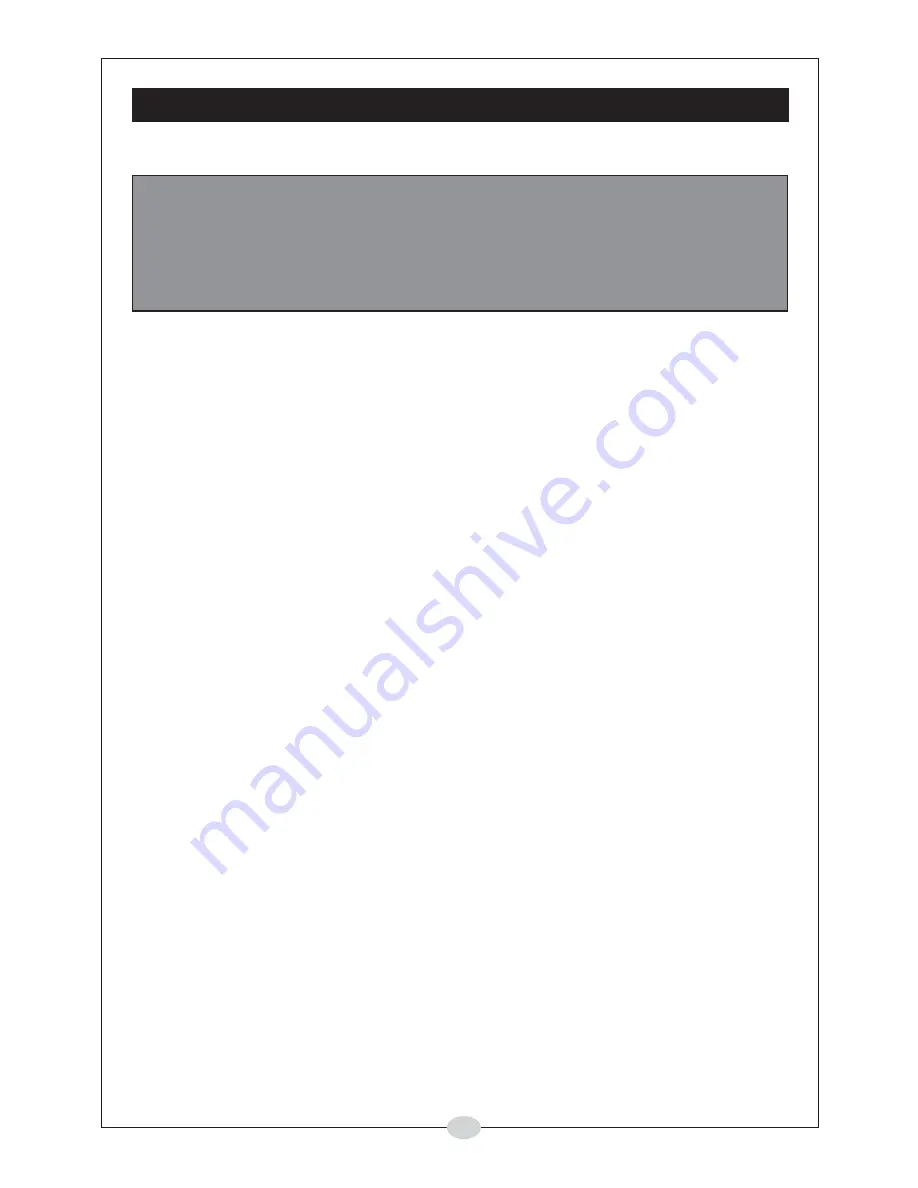
GENERAL SAFETY PRECAUTIONS
FOR OPERATING MACHINERY
WARNING
As with all machinery, there are certain hazards involved with their operation and
use. Exercising respect and caution will considerably lessen the risk of personal
injury. However, if normal safety precautions are overlooked, or ignored,
personal injury to the operator, or damage to property may result.
1.
KNOW YOUR MACHINE. Read the manual carefully. Learn the machines applications
and limitations, as well as the specific potential hazards peculiar to it.
2.
KEEP GUARDS IN PLACE and in working order.
3.
EARTH ALL MACHINES. If the machine is equipped with three-pin plug, it should be
plugged into a three-pin electrical socket. Never remove the earth pin.
4.
REMOVE ALL ADJUSTING KEYS AND WRENCHES. Before starting, form the habit of checking
to ensure that keys, wrenches and tools are removed from the machine.
5.
KEEP WORK AREA CLEAN. Cluttered areas and benches invite accidents.
6.
DON’T USE IN DANGEROUS ENVIRONMENT. Don’t use machinery in damp or wet locations,
or expose them to rain. Keep work area well lit.
7.
MAKE WORKSHOP CHILDPROOF - with padlocks, master switches or by removing starter
keys.
8.
KEEP CHILDREN AND VISITORS AWAY. All children and visitors should be kept a safe
distance from work area
9.
DON’T FORCE THE MACHINE. It will do the job better and safer, at the rate for which it
was designed.
10. USE THE RIGHT TOOL. Don’t force a tool or attachment to do a job for which it was not
designed.
11. WEAR PROPER APPAREL. Loose clothing, gloves, neckties, rings, bracelets, or other
jewellery may get caught in moving parts. Nonslip footwear is recommended. Long hair
should be contained.
12. USE SAFETY GLASSES. Everyday eyeglasses only have impact resistant lenses, they are
NOT safety glasses.
13. USE EAR DEFENDERS.
14. DON’T OVERREACH. Keep proper footing and balance at all times.
15. MAINTAIN TOOLS IN TOP CONDITION. Keep tools sharp and clean for best and safest
performance. Follow instructions for lubricating and changing accessories.
16. ALWAYS DISCONNECT THE MACHINE before servicing or changing accessories.
17. AVOID ACCIDENTAL STARTING. Ensure machine is switched OFF before plugging in.
18. CHECK FOR DAMAGE. If part of the machine (eg. A cover or guard), is damaged, it
should be carefully inspected to ensure that it can perform its’ intended function
correctly. If in doubt, the part should be renewed. Damage to moving parts or major
components should be Inspected by a qualified technician before operating the
machine. Contact your local dealer for advice.
4
Summary of Contents for Metalworker CL251MH
Page 15: ...PARTS DIAGRAM 15 ...
Page 16: ......