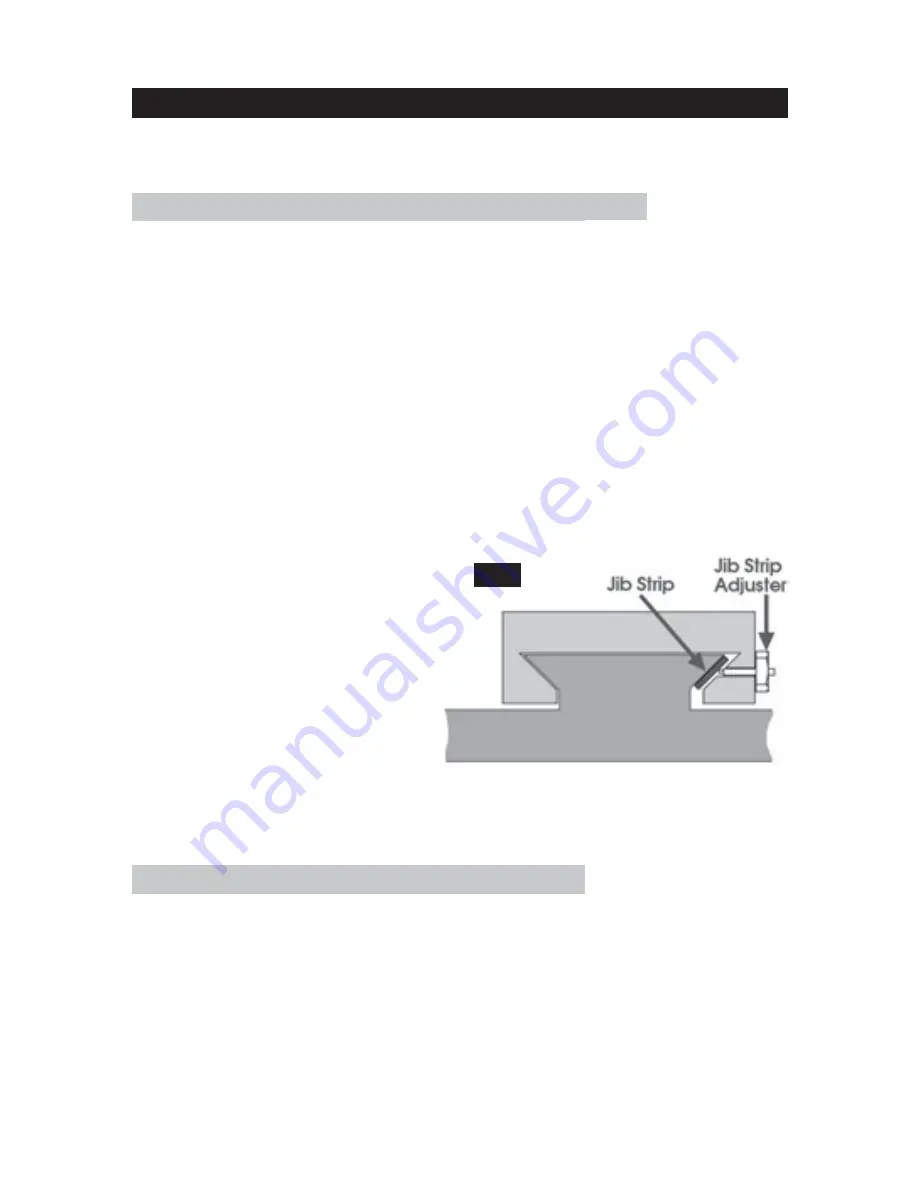
17
SETTINGS AND ADJUSTMENTS
4.
If the movement is too slack, screw
all adjusters ‘in’ by one eighth of
a turn, and re-try. Similarly, if the
movement is too stiff, screw ‘out’
the adjusters by one eighth of a
turn until the correct adjustment
is attained.
5
Tighten all lock nuts taking care to
ensure you do not move the jib
screws whilst doing so.
6.
When completed, retract the cross-slide fully and apply oil to all mating surfaces
and the feed screw thread, then wind the slide back to its normal position.
Similarly, apply a light film of oil to the bed at the mating sufaces with the Saddle.
B. FEED HANDLES
The Cross Slide and Saddle feed should run smoothly, and the scale must rotate
with the handle.
If any stiffness occurs, it is probably the result of swarf lodging between the mating surfaces.
Undo the securing hex socket head screw securing the handle. Remove the handle, which
is keyed on the shaft, then pull off the collar with the scale taking great care to retain the
small wire spring which sits in a groove beneath the collar and the key.
Clean the assembly and reassemble in reverse order. It will be necessary to hold
the spring plate in place with a small screwdriver, or similar tool, and pushing down
on it to allow the collar to be correctly located on to the shaft.
Occasionally, it may be necessary to readjust various components in order to maintain
optimum performance. The adjustments that may be performed are as follows:
A. CROSS-SLIDE AND SADDLE ADJUSTMENTS
The Cross-Slide and Saddle are mounted on dovetail slides,illustrated in FIG. 10. Between
the sloping surfaces on one side of the dovetail, a ‘jib strip’ is inserted, which may be
tightened against the dovetail under the influence of adjuster, or ’jib’ screws.
The jib screws are to be found on the right hand side of the Cross-Slide, and at the
rear of the Saddle. In time, wear will occur on the mating surfaces resulting in a
‘sloppiness’ of action.
To adjust the jib strip, to account for wear and ensure the slide moves evenly and
smoothly, proceed as follows:
1.
Slacken off all lock nuts and screw inthe jib screws evenly, i.e. use the same
torque for each screw. The slide should be held firmly. Test by trying to turn the
handle, but do not force it.
2.
Screw out each jib screw by one quarter of a turn ONLY, and nip up the lock nuts
3.
Test again, by turning the handle. The movement should be even and smooth
along its complete length.
FIG.10
Summary of Contents for Metalworker CL250M
Page 19: ...SPARE PARTS DIAGRAM 19...