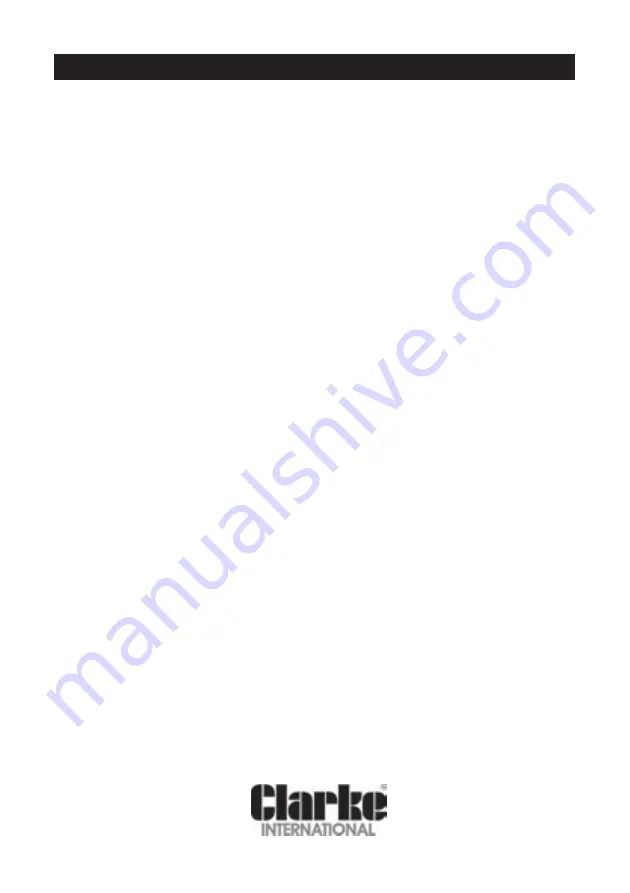
OPERATION
1.
Position the bed to the desired height, so as it will be as close as possible to the
ram when the workpiece is mounted.
Raise one side of the bed, and insert a pin into a locating hole directly
beneath the bed. Repeat the process at the other side, until the bed is level
and at the desired height, with the pins fully ‘home’.
2.
The workpiece is placed on top of the bed, or on top of the arbour, or clover
leaf, plate and must be completely stable. To achieve this you must use
packing or shims where required.
NOTE: Any packing pieces or shims used, MUST be capable of withstanding the
extreme pressure that will be brought to bear, and MUST be of sufficient size with
sufficient surface contact, so as to avoid the possibility of slipping or springing
taking place. Mating surfaces MUST be horizontal so that the force being exerted
will be vertical and NOT at an angle.
3.
Two Mandrels are provided, either of which should be screwed to the end of
the Ram, depending upon the size of workpiece bearing surface. One of
these is ‘stepped’ and is shown fitted at B1, Figs.1 and 2. The other has a larger
bearing surface area and is shown at B2.
3.
Turn the Pump Handwheel, fully clockwise and pump the handle to bring the
ram
very lightly
into contact with the workpiece.
Manoeuvre the workpiece so that the desired point of contact is
directly
beneath the centre of the ram
.
4.
When satisfied that the workpiece is correctly lined up and is completely
stable in that position, slowly pump the handle so that the ram begins to exert
pressure on the workpiece.
Continue to pump the handle, whilst standing to the side of the press (DO
NOT stand directly in front of the work), and constantly monitor the process,
ensuring the ram and work remain completely in line, and there is no risk of
slipping.
5.
When the process is complete, turn the Pump Handwheel anticlockwise to
release ram pressure
7